Aerodynamic tunnels, unique structures designed to simulate the conditions aircraft experience in flight, have transformed testing methodologies for the aviation industry. The latest innovation in this field is the honeycomb structure, or Соты аэродинамической трубы, which embodies advanced engineering techniques and materials to enhance aerodynamic testing coefficients and optimize performance assessments for various vehicles and components.
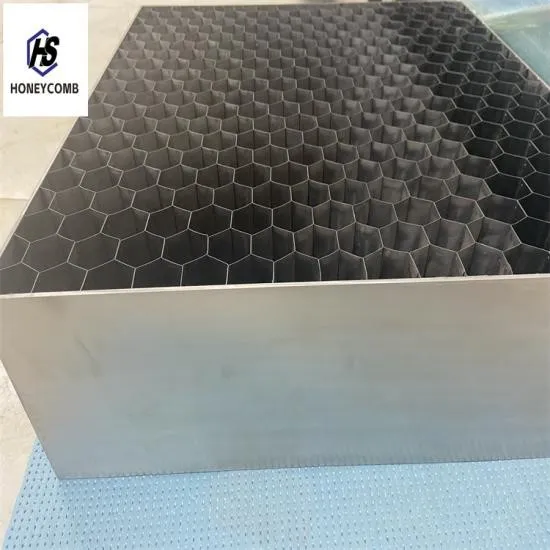
The honeycomb structure's efficacy lies in its design, mirroring natural forms that offer extreme efficiency and strength. When incorporated into aerodynamic tunnels, this structure significantly influences the laminar and turbulent flow characteristics, thereby allowing for more precise control over the testing environment. The meticulous design of these honeycomb cells aids in diminishing airflow disturbances which, if unchecked, can skew measurement data, leading to inaccurate assessments.
A key advantage of utilizing honeycomb cells in aerodynamic tunnels is their ability to facilitate a uniform flow of air. The geometric precision of each cell functions to break down large eddies into smaller, more manageable currents. This transformation is pivotal to sustaining a controlled and predictable flow, which is crucial for accurate data collection on aerodynamic forces such as lift, drag, and turbulence across the surfaces of the test object.
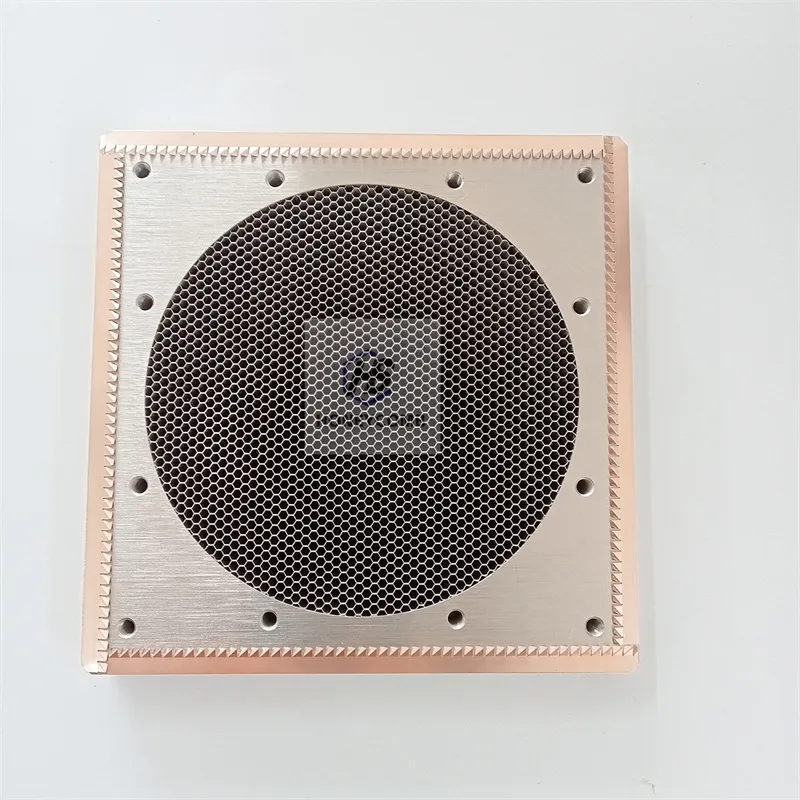
Incorporating honeycomb structures also elevates the aerodynamic tunnel's capacity to simulate high-speed conditions realistically. This capability is essential for industries beyond aerospace, including automotive and civil engineering, where understanding airflow dynamics can influence design decisions and materials selection. For instance, automotive manufacturers utilize these insights to innovate on vehicular form and structure, ultimately enhancing fuel efficiency and performance.
From an engineering expertise perspective, the shift towards honeycomb structures requires an in-depth understanding of fluid dynamics, materials science, and structural engineering. Engineers must consider multiple variables, such as the angle, size, and material of the cells, all of which must be optimized based on the specific parameters of the test scenarios. This complexity underscores the necessity for a collaborative approach, integrating knowledge from physics, engineering design, and materials innovation.
Hundreds of aerodynamic tubes
Material selection is another pertinent factor affecting the performance of honeycomb structures. Traditionally, honeycomb cores were fabricated using materials such as aluminum, which combined lightweight properties with significant strength. However, advances in material science have introduced composites and advanced polymers, enhancing durability while reducing weight. These materials not only withstand the stresses environment but also streamline fabrication processes, cutting down time and cost.
The reputation of firms producing these specialized structures is crucial. Companies boasting a record of reliability and precision engineering instill confidence amongst potential clients, making trustworthiness and authoritativeness key differentiators in the competitive landscape of aerodynamic testing solutions. Such firms often collaborate with academic institutions and industry leaders in research and development initiatives, further solidifying their positions as pioneers of innovation and competence.
In terms of experience, feedback from engineers and scientists who employ honeycomb structures in aerodynamic tunnels highlights several improvements over conventional testing methods. Enhanced data fidelity, lower operational costs due to efficient resource utilization, and broader testing capability for extreme conditions rank among the most prominent benefits reported. This practical evidence positions the honeycomb structure as a transformative innovation within the sector.
Ultimately, the continuous development and refinement of honeycomb structures in aerodynamic tunnels are aligned with broader industry trends towards sustainability and efficiency. By enabling more accurate simulations and testing, these structures contribute significantly to the design and development of future-ready vehicles and technologies. Furthermore, the reliable data generated are pivotal in crafting regulatory standards and certification processes, ensuring safety and performance benchmarks are consistently met.
As industries evolve in search of groundbreaking solutions to meet ever-growing demands, honeycomb structures in aerodynamic tunnels exemplify the convergence of nature-inspired design and cutting-edge engineering. By balancing innovation with proven expertise, manufacturers and researchers can spearhead advancements that will reshape not only theoretical approaches but practical applications in real-world contexts.