Cellular sheet metal, a versatile and dynamic material, has gained significant attention in recent years due to its unique structure and broad applications. With an intricate design akin to honeycomb, it offers remarkable features that are harnessed in various industries, from construction to automotive. Drawing from a wealth of experience and expertise, this article delves into the intricate facets of cellular sheet metal, underscoring its definitive advantages and the trust it commands within industry-specific applications.
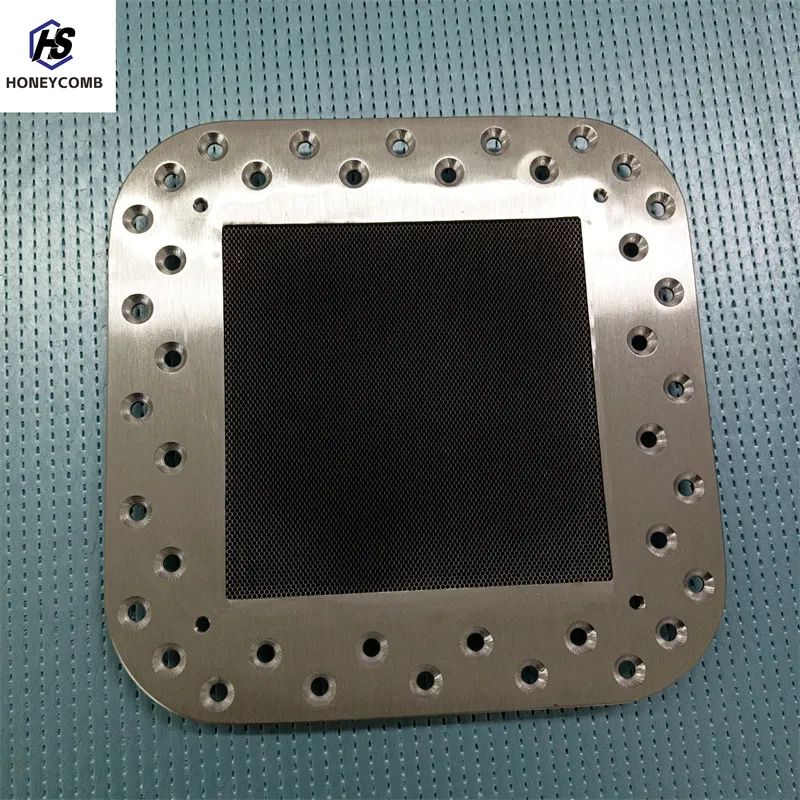
Cellular sheet metal stands apart due to its lightweight nature, which is a primary advantage in sectors requiring material strength without the added weight. In the automotive industry, for instance, there is a growing trend toward producing more fuel-efficient vehicles. By integrating cellular sheet metal into vehicle designs, manufacturers can significantly reduce weight while maintaining structural integrity.
The aviation industry, another sector where weight plays a critical role, has long appreciated the benefits of cellular structured materials. Aircraft components crafted from this metal can offer a reduction in overall mass, enhancing fuel efficiency and reducing emissions. The expertise of aerospace engineers is continually leveraged to optimize the utilization of cellular sheet metal, proving its authority in a field where precision and trust are non-negotiable.
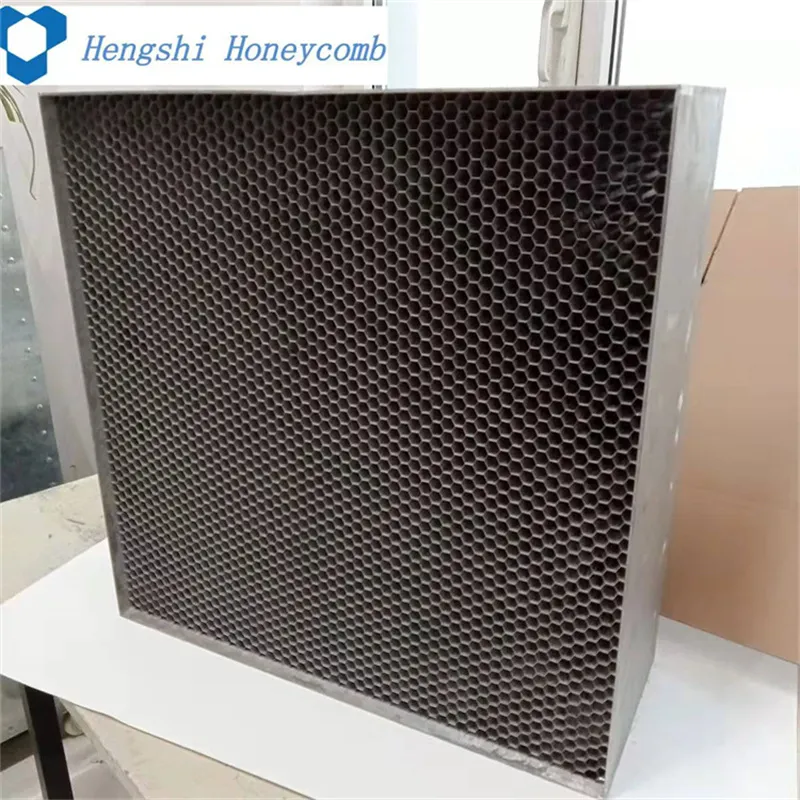
Construction is yet another domain where the authoritative presence of cellular sheet metal is felt. Architects and builders are increasingly incorporating it into designs due to its excellent strength-to-weight ratio and thermal insulation properties. These features contribute to constructing more efficient, sustainable buildings. Real-world experiences have shown that such implementations lead to reduced energy consumption and improved building longevity.
Beyond its practical applications, the production process of cellular sheet metal itself speaks to its expertise-driven design. Created through a meticulous process that involves layering thin metal sheets and bonding them in a grid-like structure, the resultant material displays unparalleled durability and resilience. This sophisticated production process ensures a level of quality that meets stringent industry standards and builds trust among consumers and professionals alike.
Honeycomb metal plate
The environmental benefits cannot be ignored either. Cellular sheet metal is often produced using recyclable materials, thus promoting sustainability. In an age where eco-friendly solutions are increasingly valued, the use of recyclable resources establishes this metal as a trusted material for environmentally conscious companies.
Trustworthiness in product applications is further bolstered by rigorous testing and adherence to international standards. Cellular sheet metal is subjected to extensive research and development, ensuring that its properties meet the demanding expectations of various industries. This continuous innovation is backed by a solid foundation of professional expertise and knowledge, ensuring reliable performance in even the most challenging conditions.
Emphasizing quality and consistency, manufacturers also collaborate with industry experts to develop cellular sheet metal solutions tailored to specific needs. This collaboration results in the creation of customized components that align perfectly with client requirements, reinforcing the trust and authority that cellular sheet metal holds among engineers and designers.
To summarize, cellular sheet metal embodies a perfect blend of innovation, efficiency, and reliability. Its growing prominence across multiple industries highlights its indispensability and the trust it has garnered through proven performance and stringent quality controls. Whether in enhancing fuel efficiency in vehicles, contributing to sustainable architecture, or defining the future of aviation components, cellular sheet metal stands as a testament to the power of expert-driven, authoritative solutions. The industry's continued investment and trust in this material underscore its position as an irreplaceable component of modern engineering and design.