The aerospace industry is an ever-evolving field, where innovation and technology continually reshape the boundaries of possibility. Among the numerous advancements that have captured the attention of engineers and manufacturers alike, the honeycomb structure, known in Italian as aerospaziale a nido d'ape, stands out for its unique combination of strength, lightness, and versatility. This remarkable material is central to manufacturing techniques aimed at improving the performance and efficiency of various aerospace components.
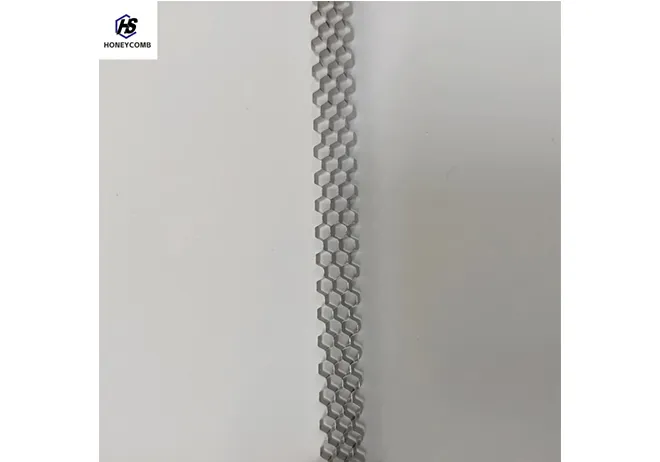
Manufacturers of aircraft, satellites, and spacecraft face the perpetual challenge of balancing weight and structural integrity.
The honeycomb structure provides an elegant solution to this conundrum. It is designed to mimic the natural hexagonal pattern found in beehives, offering substantial benefits in terms of weight reduction and load-bearing capacity. The core material, often made from aluminum, Nomex, or carbon fiber, is sandwiched between two thin, yet incredibly strong, face sheets. This configuration not only provides a significant weight advantage over traditional materials but also maintains the necessary rigidity and strength demanded by aerospace applications.
The beauty of honeycomb structures lies in their capacity to absorb energy during impacts, making them indispensable for aircraft components such as wings, fuselage sections, and interior panels. This energy absorption characteristic is also beneficial in the context of space exploration, where the materials are subjected to extreme conditions during takeoff and landing phases. One of the significant advantages of this structure is its ability to withstand high temperatures, an essential feature when considering the intense heat generated during re-entry to Earth's atmosphere.
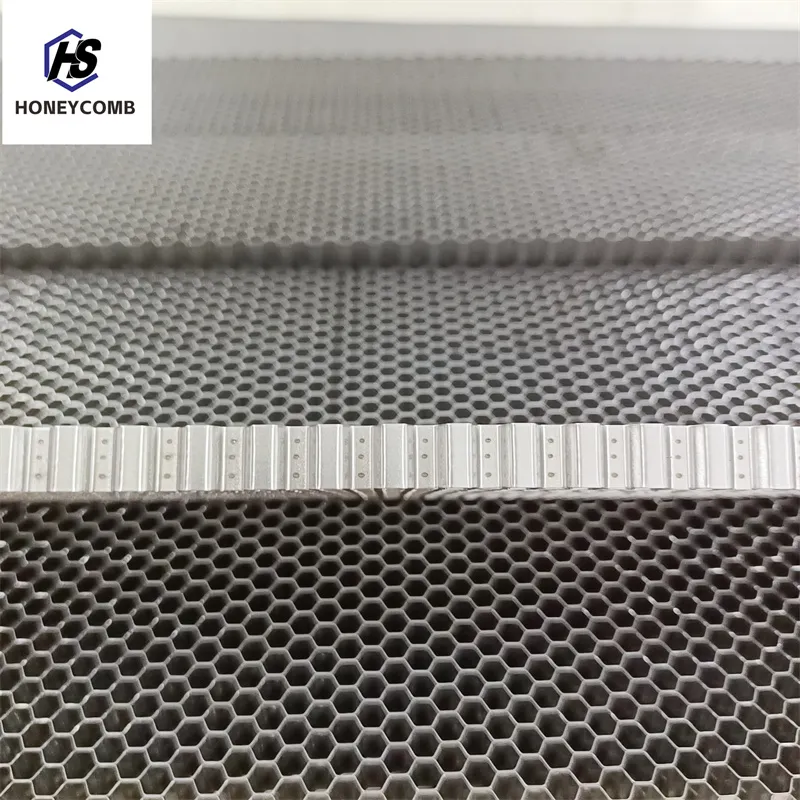
Over the years, significant advancements in manufacturing technology have allowed for even more precise and cost-effective production of honeycomb panels. Automation and computer-aided design have played pivotal roles in refining the process, ensuring that each panel adheres to the stringent quality standards required by aerospace authorities. The implementation of these technologies has also drastically reduced production times and costs, making honeycomb structures more accessible for a broader range of applications within the industry.
Professionals working with honeycomb structures must possess a deep understanding of material science and engineering principles. This expertise ensures that the structures are not only correctly designed but also comply with the safety and performance criteria unique to aerospace applications. Accredited training programs and hands-on experience are crucial for engineers working in this field, equipping them with the knowledge necessary to innovate and optimize these structures further.
honeycomb aerospace
Collaboration and knowledge exchange among aerospace engineers, material scientists, and manufacturers are vital. The complex nature of honeycomb structures demands a multidisciplinary approach to develop cutting-edge solutions that meet the ever-increasing demands for efficiency and performance. Industry conferences and symposiums provide a platform for experts to share their insights, fostering a culture of continuous learning and improvement.
The trustworthiness of honeycomb structures in aerospace applications is bolstered by rigorous testing and certification processes. Each component undergoes extensive evaluation under simulated conditions that mirror real-world scenarios. These tests ensure that the honeycomb panels can withstand the mechanical stresses they will encounter throughout their operational life. Furthermore, certification by recognized aerospace authorities guarantees that these components meet global safety standards, an essential factor in maintaining the trust of manufacturers and operators worldwide.
In addition to their mechanical properties, honeycomb structures are also gaining recognition for their environmental benefits. As the aerospace industry explores ways to reduce its carbon footprint, the lightweight nature of honeycomb panels contributes to more fuel-efficient aircraft designs, which, in turn, result in lower greenhouse gas emissions. This aligns with the industry's goals to enhance sustainability and minimize ecological impact.
In conclusion, the aerospaziale a nido d'ape or honeycomb structure represents a pinnacle of engineering prowess within the aerospace industry. Its blend of lightness, strength, and versatility continues to revolutionize the way we approach aircraft and spacecraft design. By prioritizing expertise, collaboration, and rigorous testing, the industry ensures that honeycomb structures meet the highest standards of reliability and performance. As technological advancements continue to unfold, the potential applications and benefits of this remarkable material are poised to expand even further, setting a new benchmark for innovation in aerospace engineering.