The innovative integration of cell aluminium honeycomb structures into modern applications illustrates a dynamic advancement in engineering solutions. These honeycomb panels have emerged as a pivotal technology across multiple industries due to their unmatched combination of lightweight construction, superior strength, and energy efficiency.
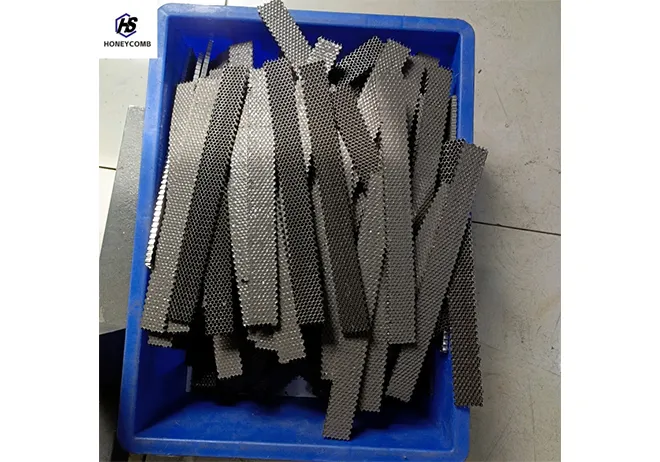
One of the compelling features of cell aluminium honeycomb structures is their exceptional strength-to-weight ratio. This is achieved through the hexagonal lattice configuration that mimics the natural honeycomb's form, offering maximum structural efficacy with minimal material usage. The resulting panels are incredibly robust yet lightweight, fundamentally altering the approach to architectural design, automotive engineering, aerospace applications, and beyond.
Architects and engineers leverage cell aluminium honeycomb panels to create structures that require reduced structural support without compromising on durability and stability. The panels can be used for curtain walls, partitions, and cladding systems, providing an elegant solution that merges aesthetics with functional integrity. The lightweight nature reduces structural load, presents savings in foundation costs, and enables creative freedom in design while maintaining high standards of safety and performance.
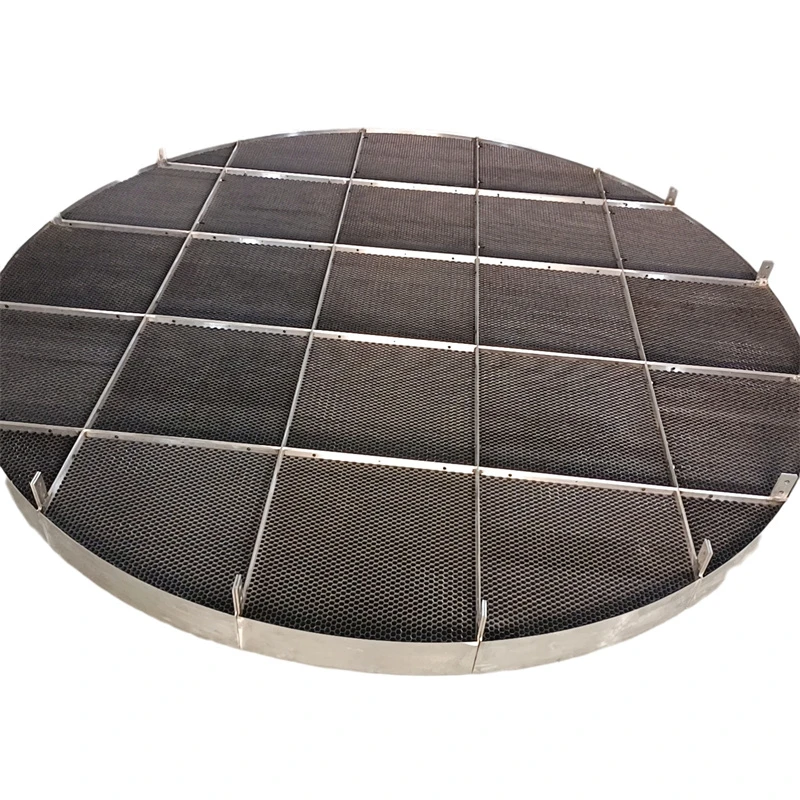
In the automotive industry, these honeycomb structures are gaining traction as manufacturers strive to enhance fuel efficiency and reduce emissions. By replacing heavier materials with aluminium honeycomb panels, vehicles can achieve considerable weight reduction, translating to improved fuel economy and lower environmental impact. Moreover, their excellent energy absorption characteristics make them ideal for crash safety applications, offering enhanced protection in the event of collisions through superior impact resistance.
The aerospace industry epitomizes the necessity for materials that provide reliability while economizing on weight. Here, cell aluminium honeycomb structures are indispensable, facilitating the construction of maneuverable, efficient, and safe flying machines. Their utilization in aircraft interiors, flooring, and bulkheads exemplifies their critical role in weight management and structural reinforcement, underpinning safer and more cost-effective aviation.
cell aluminium honeycomb
Additionally, cell aluminium honeycomb panels contribute to environmental sustainability, a growing priority in design and manufacturing disciplines. The production of these panels is eco-friendly, involving recyclable materials, which aligns with global efforts towards reducing carbon footprints and promoting green economies. This sustainable aspect, combined with their long lifespan and reduced maintenance requirements, positions aluminium honeycomb solutions as a forward-thinking choice for eco-conscious projects.
Expertise in deploying cell aluminium honeycomb structures is crucial. Professionals well-versed in this technology ensure precise engineering applications, maximizing the advantages inherent to the material's properties. Their knowledge aids in overcoming common challenges such as panel joining methods, thermal expansion, and endurance under fluctuating stress conditions. By understanding these nuances, experts can enhance the user experience — from initial design through to deployment and maintenance stages.
Epitomizing authority and trustworthiness,
companies specializing in aluminium honeycomb solutions maintain rigorous quality control standards. Certifications from esteemed bodies affirm compliance with safety norms and manufacturing excellence. This assurance bolsters client confidence, encouraging widespread industry adoption.
As industries inch towards futuristic designs and overall sustainability, cell aluminium honeycomb panels continue to set benchmarks for innovative structural solutions. With their multifaceted applications stretching beyond traditional boundaries, they remain an exemplary embodiment of modern engineering meeting ecological consciousness, reaffirming their indispensable role in the technological paradigm.