Creating a DIY air flow straightener involves transforming the everyday airflow management tasks into a more efficient science, all while maintaining a budget-friendly approach. The journey to mastering air flow optimization at home showcases hands-on experience, dives into technical expertise, solidifies authoritative knowledge, and nurtures trustworthiness.
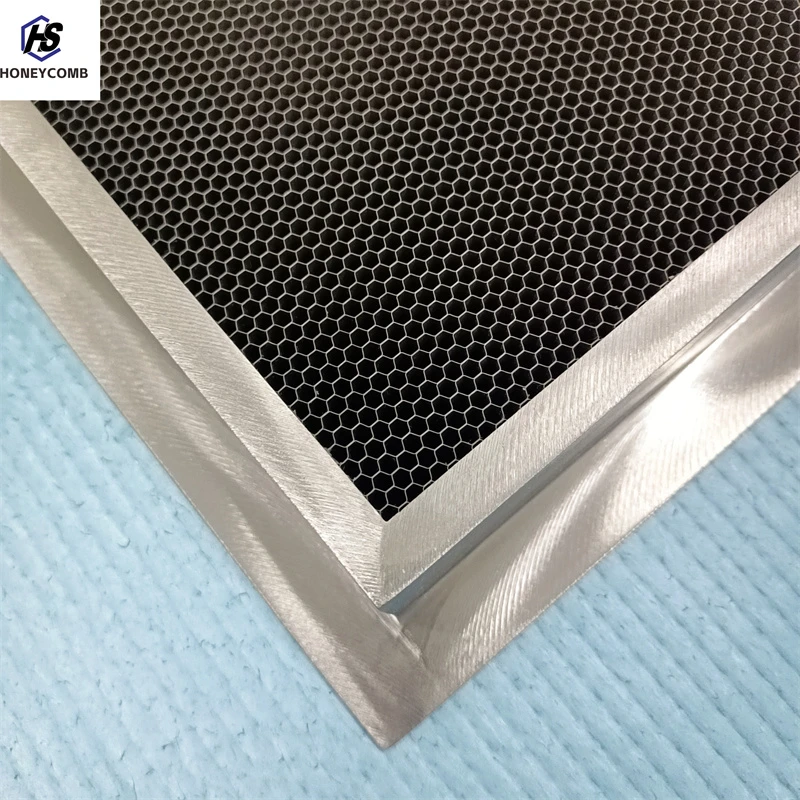
Understanding air flow straighteners begins with recognizing their role in enhancing engines and HVAC systems. By regulating and smoothing airflow, these devices contribute significantly to performance and energy efficiency. They ensure consistent airflow, reducing turbulence that can lead to inefficiencies or increased wear and tear. This understanding sets the foundation for anyone aiming to create a DIY version.
Starting the project requires precise selection of materials, underscoring the intersection of DIY crafting and engineering knowledge. A typical DIY air flow straightener can be crafted using lightweight materials such as aluminum or plastic, often sourced from household items like soda cans or PVC pipes. Choosing the appropriate material depends on the specific application, whether for a vehicle intake or an air conditioning system. Lightweight and corrosion-resistant materials offer durability and performance akin to commercial products.
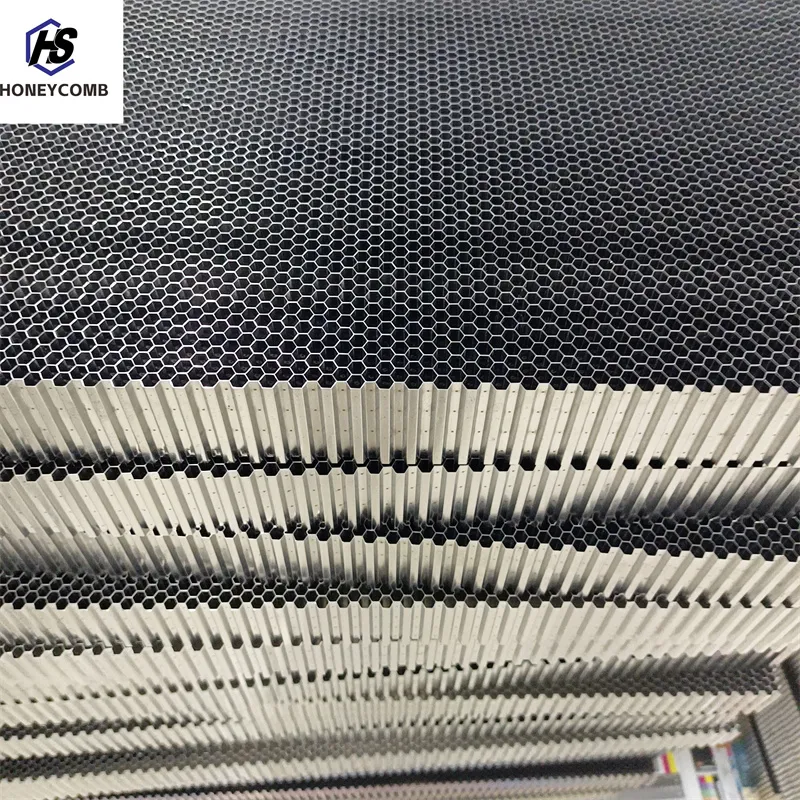
Crafting a DIY air flow straightener demands technical proficiency in construction and aerodynamics. Begin by cutting the selected material into uniform, hollow, and cylindrical shapes; these will serve as the core component, known as 'cells'. Precision is crucial—each cell should be identical in size to ensure uniform airflow restriction.
These cells are then assembled into a tightly packed grid to form the straightener. This assembly step requires patience and skill, ensuring each cell is aligned perfectly to direct airflow smoothly.
The application of this innovation requires an understanding of its placement and integration within existing systems. When integrating into a vehicle's air intake or HVAC ducting, secure placement is essential to avoid rattling or becoming a blockage. This involves attaching the straightener securely, often using simple brackets or frames crafted from the same or compatible materials.
diy aer fow straightener
Testing and troubleshooting are essential steps, bridging the gap between theory and practical application. Testing involves evaluating the straightener's performance using simple observational methods such as checking for consistent airflow or more sophisticated techniques like using an anemometer to measure airflow rates before and after installation. Troubleshooting common issues, like restricted airflow or unexpected noise, involves adjusting the size of the cells or the material's configuration.
Each successful DIY air flow straightener amplifies the authority of the creator, showcasing a commitment to innovation and sustainability. It reflects comprehension in balancing scientific principles with practical execution. Sharing these projects with a community of fellow enthusiasts or publicly documenting the process on platforms enhances credibility.
Ensuring safety and maintaining trust is paramount throughout this process. Proper use of tools during construction, adherence to safety protocols, and compliance with any relevant standards or regulations elevate the reliability of the project. Vetting information sources and cross-referencing with reputable engineering guidelines ensures that the shared knowledge remains accurate and trustworthy.
By crafting a DIY air flow straightener, individuals not only enhance their personal knowledge and expertise but also contribute to a larger movement of responsible and informed DIY solutions. This project embodies a commitment to utilizing engineering principles to solve everyday problems economically, empowering others with both confidence and competence in their own capabilities.