In the realm of industrial and commercial applications, maintaining optimal performance while ensuring safety and compliance with electromagnetic interference standards is crucial. EMI shielded air filters and intake systems, specifically designed to manage these demands, are indispensable. These components not only preserve the integrity and efficiency of electronic systems but also mitigate potential disruptions caused by electromagnetic interference.
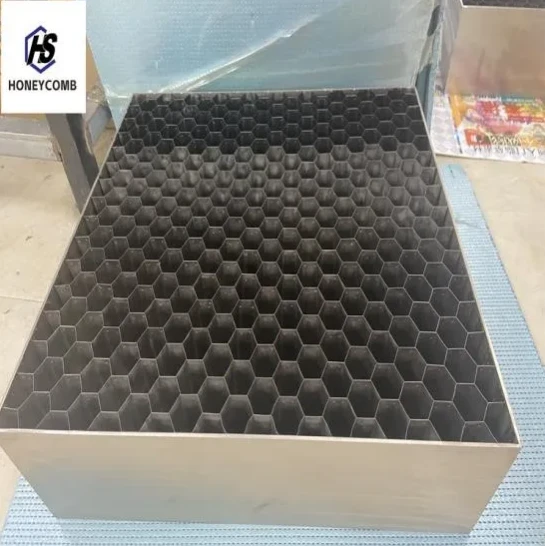
Electromagnetic interference (EMI) can wreak havoc on electronic systems, causing malfunctions, data loss, or even complete system failure. EMI can originate from a myriad of sources, including other electronic devices, motors, and power lines. Therefore, implementing EMI shielded air filters and intake systems is paramount in environments where electronics are critical.
EMI shielded air filters serve the dual purpose of filtering airborne contaminants while providing a conductive barrier that prevents unwanted electromagnetic signals from penetrating sensitive electronic enclosures. The construction of these filters typically involves multilayered materials that combine metallic meshes with traditional filtering media. This layered design ensures that air can flow adequately to cool the system, while the metallic meshes reflect or absorb electromagnetic radiation, effectively shielding the electronic components within.
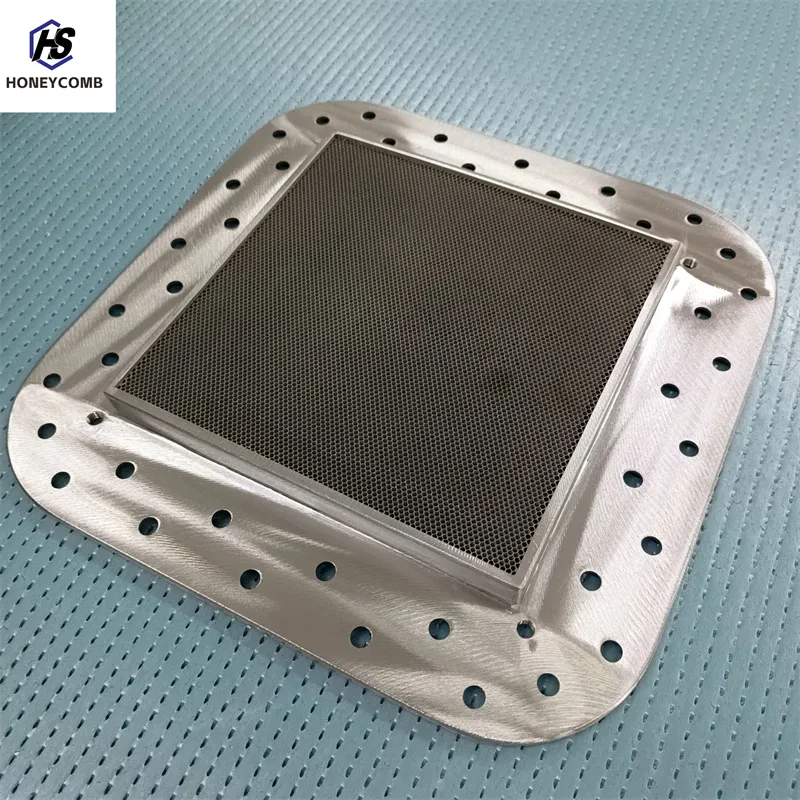
In practice,
these filters are used across a variety of industries. In the telecommunications sector, for example, base stations equipped with sensitive receiver and transmitter hardware utilize EMI shielded filters to maintain signal clarity and prevent cross-channel interference. Similarly, in the defense industry, such filters protect critical systems within military vehicles and command centers from potential electronic warfare attacks, ensuring operational security and effectiveness.
Leading manufacturers of EMI shielded air filters employ rigorous testing and validation protocols to ensure their products meet industry standards such as MIL-STD-461 and DO-160. These standards are essential benchmarks that ascertain a product’s robustness under specific EMI conditions, providing customers with the assurance of quality and reliability.
emi screened filters and air outlets
Selecting the appropriate EMI shielded air filter or intake requires a firm understanding of the specific environmental conditions and EMC requirements of the application. Experienced engineers assess factors such as airflow rates, temperature constraints, and the potential EMI threat level to determine the most effective solution. An oversized filter might unnecessarily restrict airflow, leading to increased energy consumption, while an undersized option may not provide adequate EMI protection.
Innovations in materials science and engineering have led to the development of more advanced EMI shielding technologies. For instance, the introduction of nanomaterials and conductive coatings has enhanced the performance of traditional filters, offering better EMI protection with minimal impact on airflow and system operation.
Moreover, collaborating with reputable manufacturers that prioritize R&D and customer support is critical. These producers not only offer state-of-the-art products but also invest in providing comprehensive guidance and customization services to tailor solutions that precisely fit the unique challenges faced by their clients.
Ultimately, the deployment of EMI shielded air filters and intake systems is a testament to a commitment to system reliability, effectiveness, and longevity. As industries continue to evolve and the density of electronic components increases, the importance of effectively managing EMI will only grow. Organizations that proactively integrate these shielding solutions into their infrastructure not just comply with regulations but also gain a competitive advantage by mitigating risks and enhancing the performance and reliability of their electronic systems.
In conclusion, EMI shielded air filters and intakes are not merely protective components—they are critical investments in quality assurance and operational excellence. Through a combination of advanced engineering, adherence to stringent standards, and forward-thinking adoption of new technologies, these components are pivotal in safeguarding the delicate balance of modern electronic systems.