The honeycomb structure, known as foche a nido d'ape in Italian, has revolutionized various industries due to its lightweight and robust characteristics. These honeycomb patterns, inspired by nature, are found in materials ranging from aerospace components to everyday packaging. For anyone engaged in product manufacturing or development, understanding and harnessing the potential of the honeycomb structure could significantly boost product innovation and effectiveness.
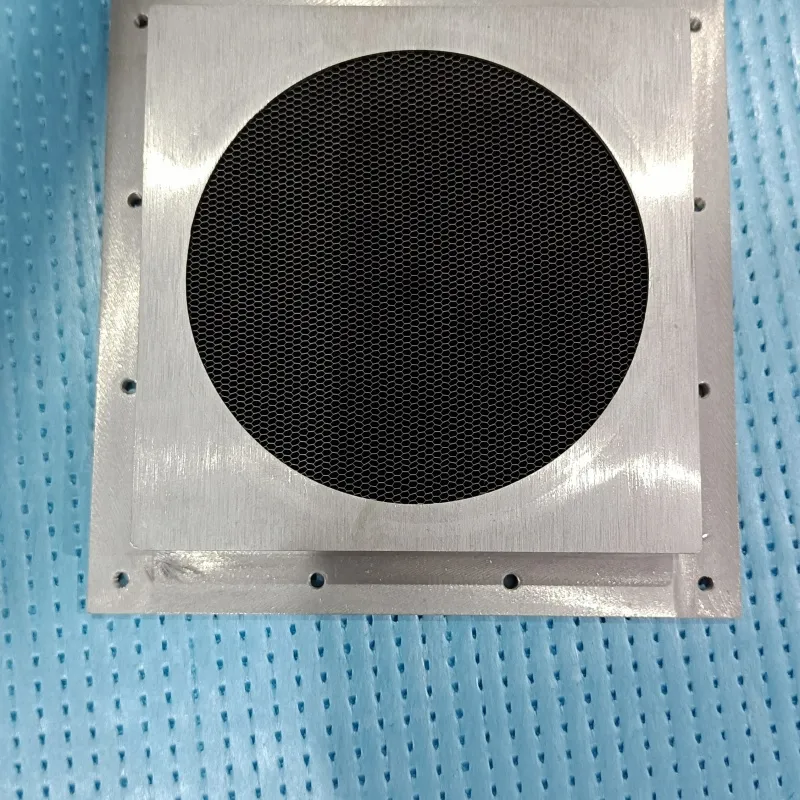
In the realm of product material design, the use of honeycomb structures brings an unparalleled advantage in achieving optimal strength-to-weight ratios. This is crucial,
especially in fields like aerospace engineering, where every gram counts. Engineers and designers have long been fascinated by the geometric efficiency of the hexagonal cells in honeycombs, which offer maximal strength with minimal material usage. By employing advanced materials such as aluminum, Nomex, or Kevlar in these configurations, products can achieve superior mechanical performance while reducing energy and raw material costs.
One of the true tests of the honeycomb structure's efficacy comes from its application in the aerospace industry. Fuselages, wings, and other critical components benefit from the rigidity and durability of honeycomb technology. The structure provides excellent impact resistance and has a natural vibration damping property, which makes flights smoother and more energy-efficient. The aviation sector's stringent demands for safety and reliability are well-matched by the honeycomb’s capacity to withstand extreme conditions, illustrating the structure’s authoritative place in modern engineering solutions.
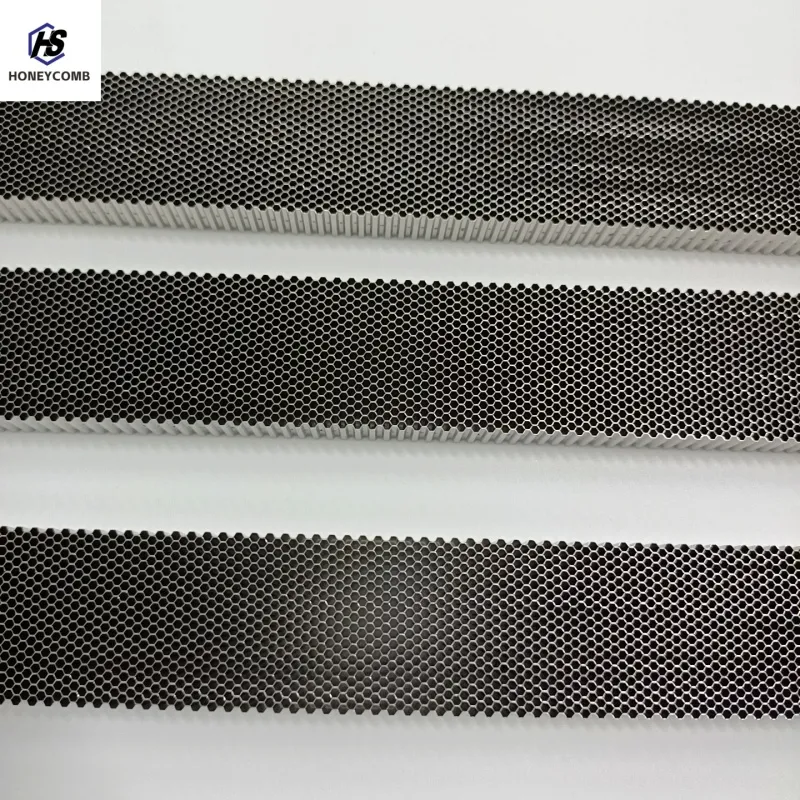
In the automotive sector, the adoption of honeycomb structures is setting new benchmarks for performance. Car manufacturers integrate honeycomb materials in body panels and chassis components, seeking enhanced crash absorption capabilities and weight reduction. The expertise of automotive engineers in tailoring honeycomb materials to specific load-bearing and aerodynamic requirements is pushing the boundaries of vehicle safety and fuel efficiency. Additionally, a lighter vehicle not only reduces emissions but also optimizes handling and accelerates speed, contributing to a more sustainable future.
From a materials science perspective, the versatility of honeycomb structures extends beyond aerospace and automotive applications. These structures are gaining recognition in architectural design and construction. Architects and engineers utilize honeycomb panels to achieve stunning facades that are both aesthetically pleasing and functionally sound. The panels offer exceptional insulation properties and are excellent at soundproofing, enhancing the environmental comfort within buildings. Their inherent ability to distribute stress evenly translates into reduced risk of structural failure and longer-lasting buildings.
seal to ape nest
Furthermore, honeycomb designs have made significant strides in sports goods manufacturing. In fields including cycling and skiing, the need for strong yet lightweight equipment is critical. Gear incorporating honeycomb technology not only boosts athlete performance but also minimizes fatigue and injury risk. The specialized development of these materials demonstrates the industry’s trust in honeycomb solutions to fulfill stringent performance standards.
In the sphere of renewable energy, honeycomb structures also play a part. Wind turbine blades, often subject to extreme stress and varying weather conditions, benefit from the strength and flexibility that these structures provide. Energy companies rely on the durability of honeycombs to maintain operational efficiency and longevity of turbines, fostering the generation of clean energy.
Sustainability is another crucial aspect where honeycomb structures demonstrate significant promise. Their efficient use of materials aligns well with the eco-friendly ethos driving modern manufacturing processes. The ability to recycle and repurpose materials within honeycomb configurations adds to their environmental benefit, presenting a substantial advantage to companies focused on reducing their carbon footprint and supporting circular economies.
For businesses and innovators, integrating honeycomb structures into product design can be transformative. However, it requires a deep understanding of the materials, design principles, and the specific needs of your application. As a leading expert in the field, staying informed on the latest advancements and emerging trends related to honeycomb technology is vital. Embracing these innovations can not only enhance the performance and appeal of your products but also establish a reputation for excellence and trustworthiness within your industry.