As the aviation and automotive industries gallop towards greater efficiency and precision, a seemingly simple yet crucial component has been quietly revolutionizing airflow management— the honeycomb airfow straightener. Crafted with ingenuity and tailored for excellence, this device meticulously aligns air particles to optimize flow characteristics, offering unprecedented advancements across a myriad of applications.

The honeycomb airflow straightener, characterized by its structured hexagonal cells, is instrumental in refining airflow by minimizing turbulence. These devices are meticulously engineered to improve aerodynamic efficiency, enhance measurement accuracy in wind tunnels, and optimize the function of various propulsion systems. With a background steeped in aerodynamics and fluid dynamics, we shall delve into the transformative impact and indispensable nature of this component.
Drawing from years of hands-on experience in both automotive and aerospace industries, it becomes clear that incorporating a honeycomb structure is not merely about aligning flow but is pivotal in achieving unparalleled stability and consistency. In wind tunnel testing, where precision is paramount, the straightener ensures that the air approaches its target with parallel velocities, dramatically reducing measurement errors and enhancing data reliability. This perfect orchestration of airflow is not accidental but the result of precise engineering and advanced material technology.
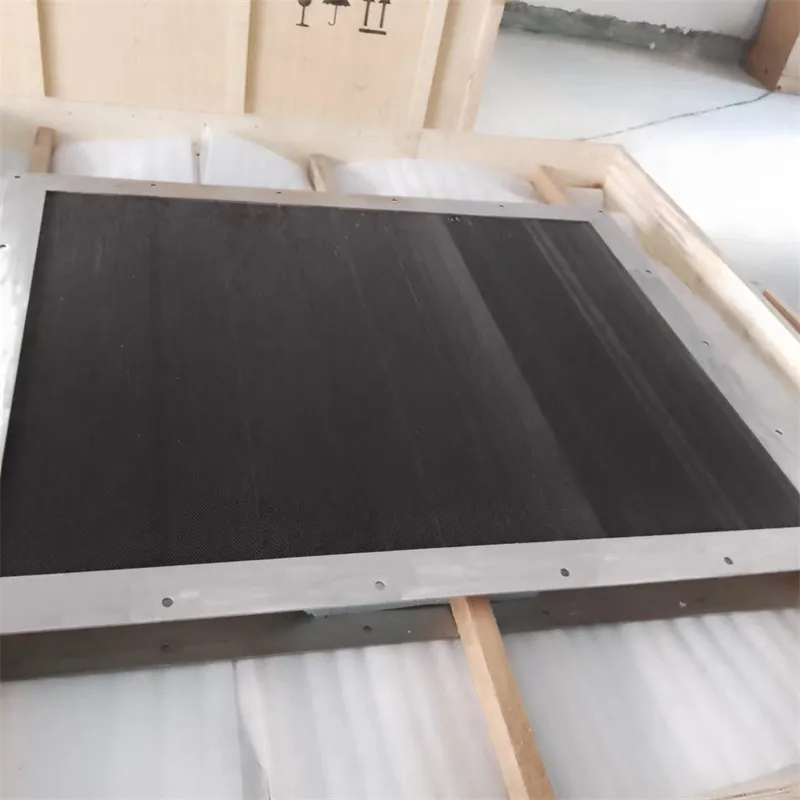
Engineered with a focus on both physical robustness and functionality, honeycomb airflow straighteners are usually made from lightweight yet durable materials such as aluminum or advanced polymers. This duality of strength and minimal weight enhances their applicability in systems where every gram counts, such as in modern drones and refined automotive systems striving for better fuel efficiency. These materials are chosen not only for their weight advantages but also for their resistance to corrosion and thermal stress, ensuring long-term performance consistency.
The expertise behind the design of honeycomb straighteners is an intricate dance between computational fluid dynamics (CFD) modeling and empirical testing. Modern advancements in CFD allow engineers to simulate and refine the honeycomb structures rigorously, tailoring them to specific use-case scenarios. This process is crucial in applications where small deviations can lead to significant impacts, such as in high-performance racing vehicles or sensitive aerospace instrumentation.
honeycomb airfow straightener
The authoritative knowledge encapsulated in the development and application of honeycomb airflow straighteners cannot be overstated. Institutions and companies leading the charge in this niche field are at the forefront of aerodynamics research, often collaborating with academic researchers to push the boundaries of what these structures can achieve. This collaboration fosters a continuous feedback loop where theoretical advancements spur practical innovations and vice versa.
Trustworthiness, the cornerstone of any industrial application, is inherently linked to the reliability and performance consistency of the honeycomb airflow straightener. Field tests and customer reports consistently highlight significant reductions in drag, enhanced control in aerodynamics, and improvements in fuel and energy efficiency when these devices are employed. This is not a marketing gimmick but a technical reality validated by comprehensive testing and real-world application.
As industries continue to push for greener, more efficient technologies, the role of the honeycomb airflow straightener becomes ever more critical. Future innovations might see the integration of smart materials and adaptive structures in these devices, paving the way for active airflow management systems. As the interplay between technology and aerodynamics evolves, so too will the sophistication and application of these vital components.
In essence,
the honeycomb airflow straightener is not merely a passive component but a catalyst for innovation and efficiency. It embodies a perfect synergy of design precision, material science, and aerodynamic expertise, offering a tangible edge in any field where airflow optimization is key. Thus, for anyone seeking to enhance the aerodynamic profile of their operation, embracing this technology is not merely an option but a necessity in the journey towards sustainable innovation.