The world of turbine technology is a constantly evolving landscape, with each innovation pushing the boundaries of efficiency, reliability, and durability. One such innovation that has significantly transformed turbine performance is the honeycomb seal. Widely recognized for its superior sealing capabilities, the honeycomb seal is becoming the standard in turbine applications, providing remarkable improvements in operational efficiency and lifecycle costs.

Honeycomb seals are named for their unique structure, which resembles the hexagonal patterns found in a natural honeycomb. This design not only optimizes the seal's ability to contain gases but also reduces leakage, a critical factor in turbine performance. The use of honeycomb seals in turbines is based on extensive research and real-world application, underscoring their credibility in enhancing turbine operations.
One of the key indicators of a component's effectiveness in a turbine system is its ability to improve the overall efficiency of the machinery. The honeycomb seal excels in this aspect by minimizing the clearance leakage between rotating and stationary components. By maintaining tighter clearances, honeycomb seals significantly reduce the amount of unplanned air bypassing, thereby increasing the turbine's thermal efficiency.
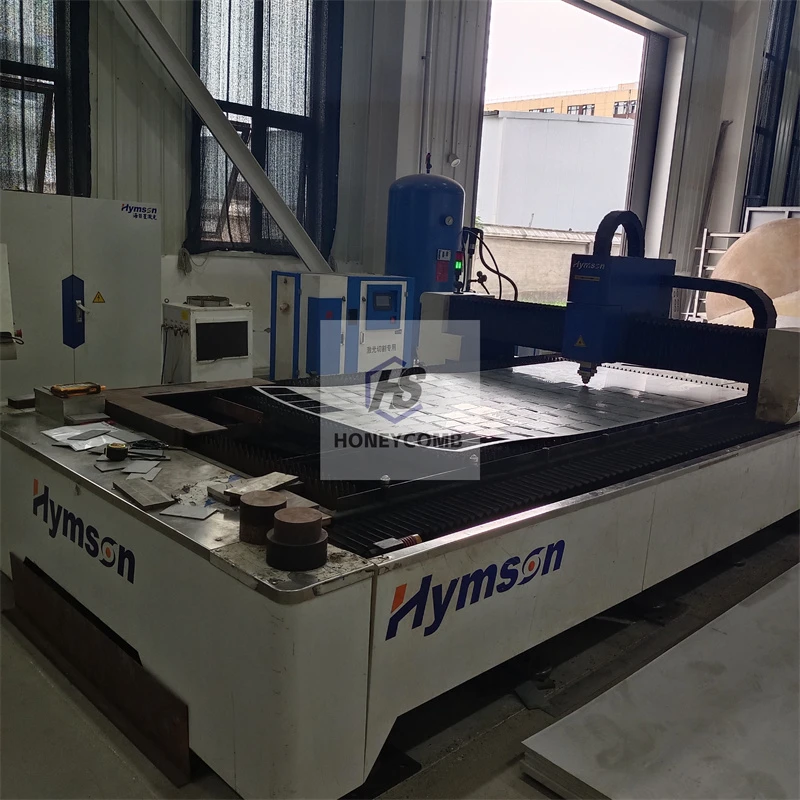
Moreover, the expertise behind honeycomb seals is supported by rigorous scientific and engineering research. Turbine manufacturers and aerospace companies globally have recognized their unparalleled ability to withstand high temperatures and pressures, making them ideal for the demanding conditions present within turbines. The use of materials such as Inconel, a high-performance superalloy, further attests to their durability and functionality under extreme conditions.
The implementation of honeycomb seals also speaks to the authoritative nature within the turbine industry. Leading companies have adopted these seals not just for their initial performance benefits but also for their longevity and reliability. Unlike traditional labyrinth seals, honeycomb seals offer a robust solution, minimizing maintenance requirements and providing long-term cost benefits.
honeycomb seal turbin
Trustworthiness is another vital component when considering turbo machinery components. The use of honeycomb seals is often supported by comprehensive testing and certification from leading industry bodies. This ensures that they meet or exceed rigorous industry standards, giving operators confidence in their equipment's reliability. These evaluations are critical, especially for applications in aviation and power generation where safety and efficiency are paramount.
In real-world applications, the experience and feedback from engineers and turbine operators further validate the effectiveness of honeycomb seals. Users consistently report improved performance metrics, including enhanced power output and reduced operational wear and tear. Such empirical evidence is a testament to their transformative impact on turbine technology.
The expertise required to design and implement honeycomb seals is not just rooted in theoretical knowledge but is also supported by practical application and ongoing innovation. Engineers constantly refine these seals to accommodate the growing demands of modern turbine applications, ensuring they remain at the forefront of technological advancements.
In conclusion, the honeycomb seal represents a fusion of innovative design, expert engineering, and real-world applicability, making it an indispensable component in the realm of turbine technology. As industries continue to seek ways to maximize efficiency and minimize costs, the adoption of honeycomb seals is likely to see a sustained increase. They not only embody the principles of efficiency and reliability but also stand as a testament to human ingenuity in overcoming the challenges of modern engineering.