In the world of advanced engineering and industrial applications, honeycomb vents have emerged as an indispensable component. These structures, characterized by their unique hexagonal lattice, are not simply a marvel of geometric elegance but serve numerous practical purposes across various domains. Here we delve into the fascinating realm of honeycomb vents, exploring their use, benefits, and the scientific principles that make them irreplaceable.
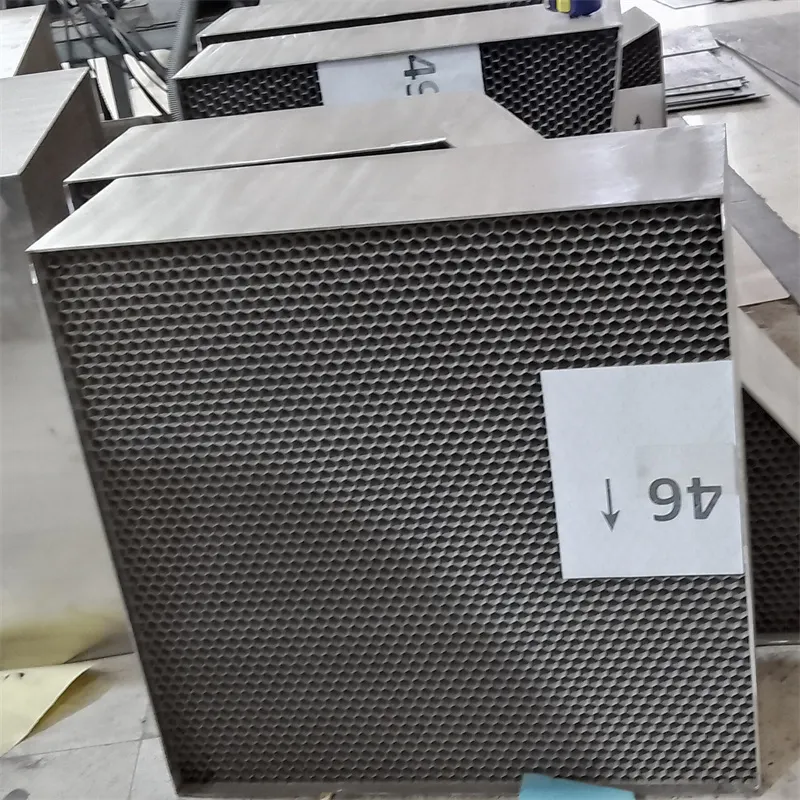
Honeycomb vents are primarily known for their ability to regulate airflow and maintain optimal ventilation in technology-intensive environments. From aeronautics to automotive sectors, and even in household appliances, these vents play a critical role in ensuring the efficient passage of air without compromising structural integrity. Their unique design maximizes open area while minimizing resistance, resulting in improved performance and fuel efficiency, an aspect highly valued in aerospace engineering.
The structural integrity provided by the honeycomb design is not just beneficial for airflow. Engineers and designers value these vents for their superior strength-to-weight ratio. The honeycomb pattern can bear significant stress while remaining extremely lightweight, making it an ideal choice for applications requiring durable, yet lightweight materials. This explains the widespread usage of honeycomb vents in designing fuselages, vehicle bodies, and even in the construction industry where lighter materials reduce the overall weight burden without sacrificing strength.
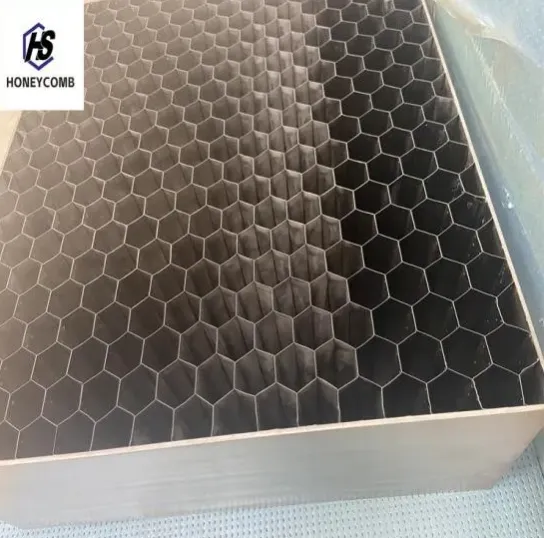
Another essential feature of honeycomb vents is their thermal management capability. By facilitating enhanced airflow, they support superior heat dissipation. This trait is especially crucial in electronic devices—such as computers and servers—where overheating can lead to decreased performance or potential failures. Companies continuously seek materials that can effectively manage thermal loads, and honeycomb vents have proven indispensable in these scenarios. With rapid developments in electronics requiring ever more efficient cooling systems, honeycomb vents are frequently incorporated into designs to enhance reliability and longevity.
honeycomb vent
Precision is key when manufacturing honeycomb vents, as even slight deviations can affect their performance. Advanced manufacturing techniques, such as 3D printing and material science innovations, have enabled the production of perfectly uniform honeycomb structures. These technological advancements ensure that each vent fulfills its intended function with maximum efficiency, whether it's filtering air or supporting a lightweight structure.
In environments exposed to electromagnetic interference (EMI), honeycomb vents offer a unique solution. By integrating conductive materials within the lattice structure, these vents can effectively shield sensitive electronic equipment from unwanted electromagnetic noise. This capability is becoming increasingly important as the proliferation of electronic devices necessitates robust protection against interference, ensuring reliable operation in various settings, from industrial floors to military applications.
The versatility of honeycomb vents is matched by their environmental benefits. Modern production processes focus on sustainability, using recyclable materials and energy-efficient methods to craft these components. By choosing honeycomb vents, industries can contribute to a lower environmental footprint while reaping the benefits of efficient, high-performance products.
In conclusion, honeycomb vents exemplify the intersection of nature-inspired design and cutting-edge technology. Their widespread application across multiple industries highlights their indispensable role in modern engineering solutions. As technology advances, the demand for efficient, reliable, and sustainable components will continue to grow, solidifying honeycomb vents' status as a foundational element in innovative design and engineering.