Metal honeycombs are revolutionizing the market with their superior strength-to-weight ratio, thermal and acoustic insulation properties, and versatile applications. The innovation lies in their unique geometric structure, inspired by natural honeycombs, which provides exceptional support and efficiency in various industries, including aerospace, automotive, and architecture.
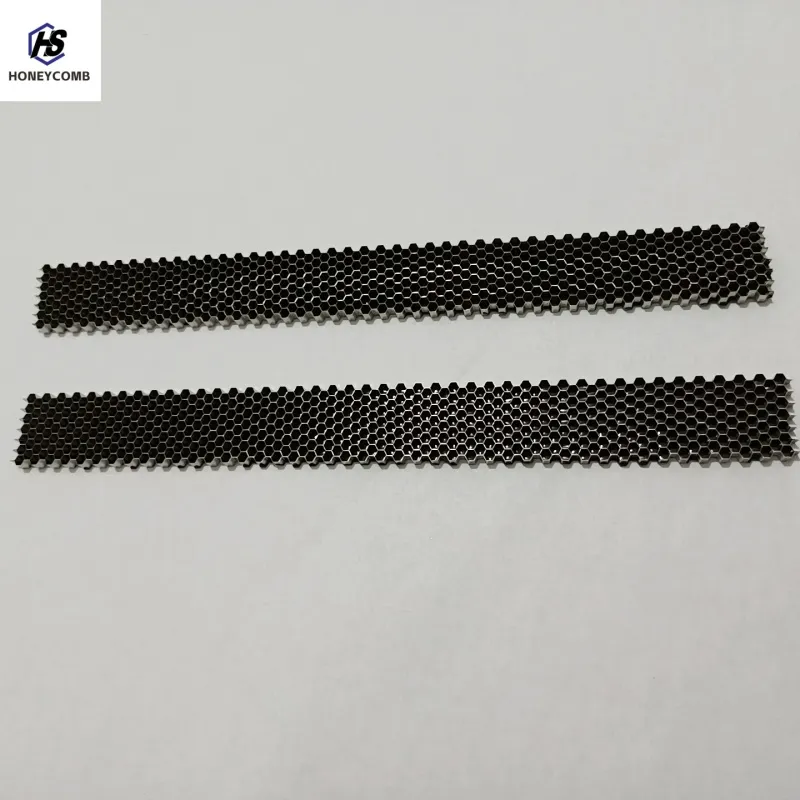
Imagine a material that embodies the robustness required for structural applications while maintaining a lightweight profile. This is precisely what metal honeycombs offer. Their cellular structure allows for custom design options tailored to specific project needs, making them invaluable for engineers seeking both strength and flexibility. The open cell design is pivotal, providing efficient load distribution and resistance to physical shocks, reducing the risk of structural damage.
In aerospace engineering, metal honeycombs are indispensable. The need for materials that can withstand extreme conditions in flight without adding significant weight is critical. Metal honeycombs excel here by providing insulation from the vast temperature fluctuations and vibrations encountered within the aerospace sector. Their application can result in more fuel-efficient aircraft thanks to the reduced weight, blending economic advantages with engineering foresight.

The automotive industry similarly benefits from this material.
Metal honeycombs infuse vehicle components with the strength to endure high-impact collisions while ensuring passenger safety. Their integration into crash absorption zones is a focus area for manufacturers aiming to enhance car safety ratings without compromising on design or cost-effectiveness. Moreover, the reduction in vehicle weight contributes directly to fuel efficiency and lower emissions, aligning with global sustainability goals.
Beyond aerospace and automotive, metal honeycombs are making strides in architecture. Architects and builders are increasingly incorporating these structures for their aesthetic appeal and functional integrity. Facades designed with metal honeycombs are not only visually striking but also offer significant energy savings by regulating indoor temperatures. The material's capacity to diffuse sound enhances its suitability for use in public and commercial buildings where acoustic control is essential.
metal honeycomb
Quality assurance in metal honeycomb manufacturing is paramount. Each honeycomb structure is tested rigorously to meet industry standards, ensuring reliability and performance. Manufacturers utilize advanced technologies like laser cutting and 3D printing to achieve precise formations and designs, ensuring each product meets the specific demands of its intended application.
Trust in the application of metal honeycombs is backed by extensive research and development. The materials used typically include aluminum, stainless steel, and titanium, chosen for their durability and performance. Reputable suppliers provide thorough documentation on product specifications, performance metrics, and environmental impact assessments, supporting informed decision-making for end-users and stakeholders.
Explorations into new alloys and composites continue to expand the potential of metal honeycombs, integrating cutting-edge research with practical applications. The industry is witnessing innovations that promise even greater efficiency and application versatility, paving the way for the next generation of engineering possibilities.
In summary, metal honeycombs represent a leap in engineering potential with their remarkable combination of strength, versatility, and efficiency. Their ability to transform industry practices across sectors makes them a cornerstone of modern material science, providing reliable, eco-friendly solutions tailored to the demands of our evolving world.