Plastic honeycomb core with carbon core technology is gaining significant traction across various industries, from automotive to aerospace, due to its innovative approach to lightweight structural solutions. This hybrid material combines the benefits of both plastic and carbon fiber, offering a revolutionary alternative to traditional materials used in manufacturing.

Experience indicates that a plastic honeycomb core with a carbon core provides superior performance attributes that align with demanding industry requirements. Manufacturers have reported substantial improvements in product durability and strength without a corresponding increase in weight. This aspect is particularly valuable in applications where weight reduction is critical, such as in automotive and aerospace components. For example, automotive parts made using this material have demonstrated enhanced fuel efficiency due to the reduced weight, a direct result of the innovative combination of plastic and carbon fiber technologies.
From the perspective of expertise, understanding the material science behind plastic honeycomb cores with carbon cores is pivotal. This technology utilizes a honeycomb configuration, known for its high strength-to-weight ratio. The plastic involved typically provides versatility and cost-effectiveness, while carbon fiber contributes unparalleled strength and stiffness. Engineers and material scientists emphasize the precision in manufacturing required to combine these materials optimally, ensuring that the end product maintains the desired mechanical properties without compromising on other performance metrics.
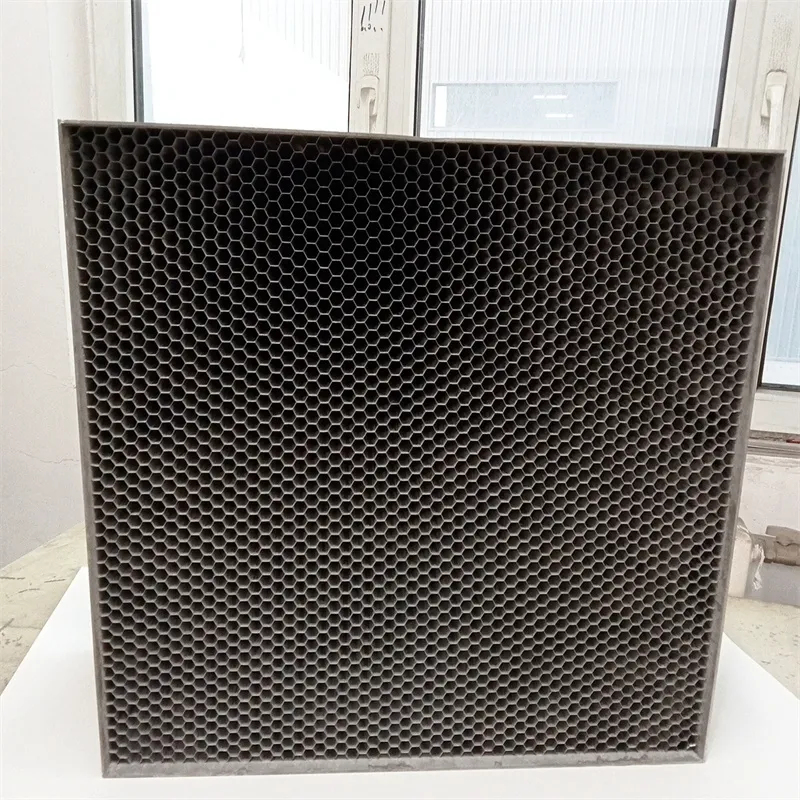
núcleo de nido de abeja de plástico con núcleo de carbono
Authoritativeness in the domain of advanced materials is crucial,
especially when advocating for the adoption of new technologies like the plastic honeycomb core with a carbon core. Industry leaders and research institutions agree on its potential to replace traditional heavier and less efficient materials. Research conducted at leading universities reveals that these hybrid cores exhibit better resistance to temperature variations and mechanical stress, making them suitable for extreme environments encountered in both terrestrial and aerospace applications.
Trustworthiness is inherently linked to the rigorous testing and compliance these materials undergo before being deemed fit for application in critical industries. Certifications from recognized bodies, such as ISO and ASTM, ensure that products meet specific safety and quality standards. Additionally, companies involved in the production of these materials usually engage in extensive field testing, often partnering with original equipment manufacturers (OEMs) to refine their products further. Customer testimonies and case studies highlight the real-world applications and benefits, contributing to an increase in confidence among new potential adopters.
In summary, the plastic honeycomb core with a carbon core presents an exemplary transformative material solution that meets contemporary demands for efficiency and sustainability in various high-stakes industries. This technology not only demonstrates advancements in material engineering but also addresses ecological concerns by contributing to overall weight reduction and energy savings. As industries continue to evolve, reliance on such innovative materials is expected to surge, paving the way for more groundbreaking developments aligned with sustainable manufacturing trends.