Stainless steel honeycomb core products have revolutionized the way various industries approach structural design and material efficiency. This innovative material captivates those seeking unparalleled strength-to-weight ratios, durability, and corrosion resistance. In aerospace, architecture, and other advanced engineering sectors, the use of stainless steel honeycomb core structures marks a significant leap in design possibilities.
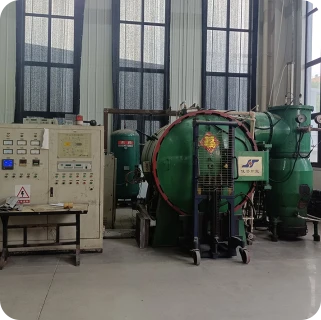
From a product perspective, stainless steel honeycomb panels are the blend of engineering expertise and practical design. These panels consist of a central core constructed in a honeycomb lattice, which is fused between two stainless steel sheets through a process known as brazing or adhesive bonding. This configuration provides exceptional mechanical performance, effectively distributing weight and pressure across the entire surface area. The resulting material is incredibly stiff and stable, allowing for a variety of applications where high load-bearing capacity and minimal weight are crucial.
In the aerospace industry, for example, stainless steel honeycomb cores serve as critical components in aircraft interiors and structures. Their lightweight nature helps in reducing the overall aircraft weight, which in turn enhances fuel efficiency and reduces emissions—a top priority in environmentally-conscious engineering practices. Moreover, these cores possess excellent damping properties, allowing for vibration reduction, which enhances passenger comfort and aircraft longevity.
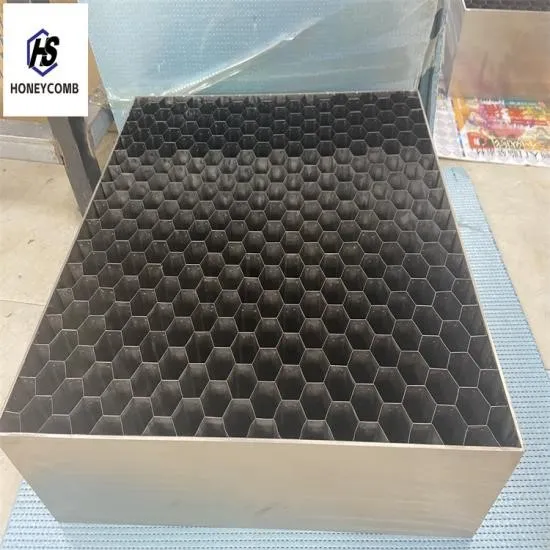
Architects increasingly favor stainless steel honeycomb panels for facade applications. Besides their aesthetic appeal, these panels offer practical solutions to design challenges faced by modern architects. They provide not only the structural integrity needed to withstand various environmental factors like wind loads and temperature variations but also maintain visual elegance with their sleek, polished surfaces. Additionally, the inherent corrosion resistance of stainless steel ensures longevity, reducing the need for ongoing maintenance and replacement, which ultimately leads to cost savings.
stainless steel honeycomb core
In addition to their practical benefits, these materials are essential from a sustainability standpoint. Manufacturers typically use recycled materials to produce stainless steel honeycomb cores, and their long-lasting nature minimizes environmental impact. Furthermore, at the end of their lifecycle, these materials can be fully recycled, presenting a closed-loop solution that aligns with global sustainability goals.
Professionals in marine engineering stand among those who benefit most from stainless steel honeycomb cores, where the harsh marine environment demands materials that stand the test of time. From shipbuilding to offshore structures, the resistance to saltwater corrosion and the material's impressive buoyancy properties make it the first choice for numerous marine applications. Additionally, the material's enhanced thermal properties are utilized in heat exchangers and other energy-efficient systems, demonstrating its versatility.
The trustworthiness and credibility of stainless steel honeycomb cores are further reinforced by extensive testing and certifications that meet international standards. Engineers and designers can rely on documented performance metrics, which help in making informed decisions when integrating these materials into their projects. Research and development in this field are ongoing, with scientists consistently testing limits and uncovering new applications.
Ultimately, stainless steel honeycomb core products represent the epitome of modern engineering prowess. They address critical challenges and meet the demands of an evolving technological landscape, providing innovative solutions across diverse sectors. Their benefits surpass traditional materials, offering superior performance and sustainability that aligns with contemporary engineering and architectural ideals. As industries continue to evolve, stainless steel honeycomb cores will undoubtedly play a pivotal role in advancing material science and construction methodologies.