The honeycomb structure, long revered in nature for its strength and efficiency, finds its industrial counterpart in the stainless steel honeycomb core, known in Italian as nucleo a nido d'ape in acciaio inossidabile. This revolutionary material remains essential across a variety of industries due to its unique combination of durability, light weight, and corrosion resistance.
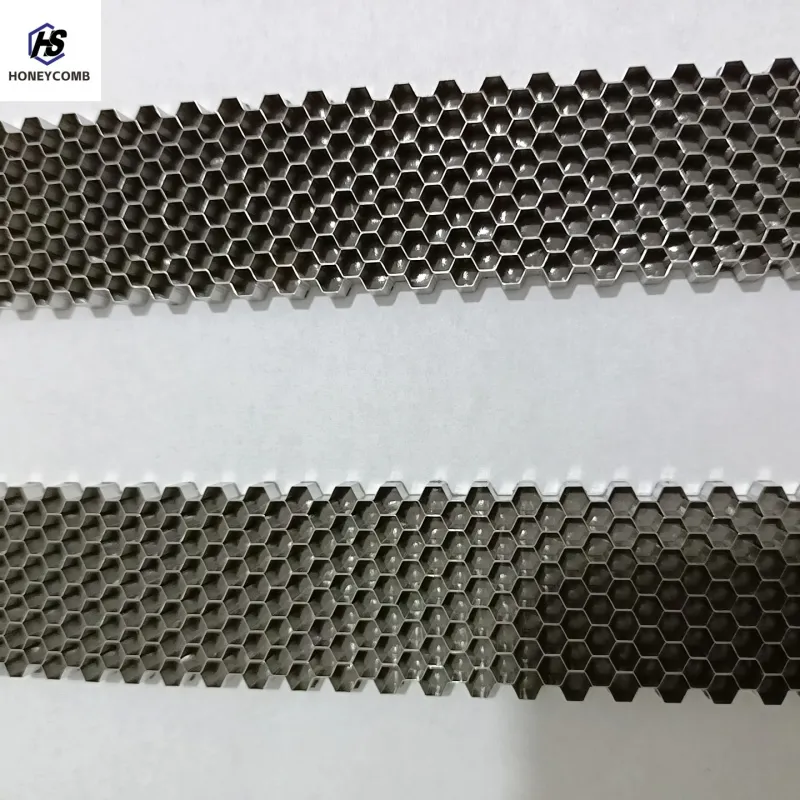
Fabricators and engineers worldwide are increasingly favoring stainless steel honeycomb cores for the myriad of applications that demand reliability and longevity. With decades of experience in manufacturing and engineering, I can attest to the transformative impact of this material in product development and structural integrity.
The expertise required in crafting these honeycomb cores is paramount. Industry specialists recognize the meticulous engineering process that involves precision cutting, forming, and bonding to create the intricate web of hexagonal cells. Each core is manufactured to meet exacting specifications that ensure optimal performance under pressure, vibration, and diverse environmental conditions. With exact engineering principles guiding production, these cores become formidable components in aerospace, architecture, and automotive sectors.
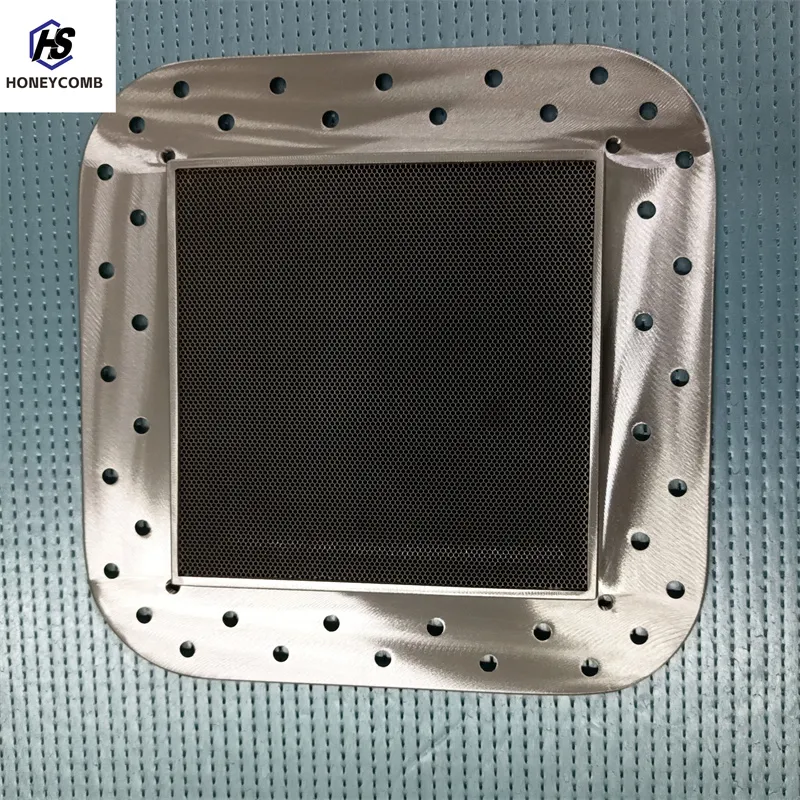
In the aerospace industry, for instance, the strength-to-weight ratio of stainless steel honeycomb cores is unparalleled. Aircraft manufacturers integrate these cores into wing panels, fuselages, and interior structures, achieving lightweight designs without compromising safety or performance. Engineers value the material's ability to withstand extreme temperatures and resist corrosion, critical factors when flying through varied climatic zones. Trusted experts at leading aerospace conglomerates consistently choose stainless steel honeycomb cores to enhance fuel efficiency and flight dynamics, underscoring their authority in aviation innovation.
stainless steel honeycomb core
Architectural applications equally benefit from the use of stainless steel honeycomb cores. Skyscrapers and large structural projects incorporate these materials for curtain walls and facades due to their aesthetic appeal and structural benefits. The reflective quality of stainless steel, combined with the geometric pattern of the honeycomb, offers architects a contemporary design element that also conforms to rigorous safety standards. Not only does the material provide superior insulation properties, making buildings more energy efficient, but it also enhances acoustics by reducing noise penetration – a testament to the broad expertise required in urban planning and construction.
The automotive industry also harnesses the power of stainless steel honeycomb cores in manufacturing high-performance vehicles. The cores' lightweight, yet robust characteristics translate to improved acceleration and handling. Vehicle manufacturers trust these cores for crash protection components, where maintaining structural integrity during impacts is crucial. The use of stainless steel enhances the recyclability of automotive components, aligning with global sustainability initiatives and proving the material's trustworthiness.
Stainless steel honeycomb cores offer an undeniable value proposition across numerous sectors. The trust bestowed upon this technology is backed by its authoritative performance credentials—tested, validated, and relied upon by engineers dedicated to pushing the boundaries of what modern materials can achieve. Seamlessly integrating strength with design flexibility, stainless steel honeycomb cores stand out as a testament to human innovation inspired by natural ingenuity.
From aerospace advancements to groundbreaking architectural feats and groundbreaking automotive designs, the stainless steel honeycomb core is not just a material; it’s a catalyst for change that professionals in varied fields depend on to deliver superior products and projects.