Dynamic seals, commonly referred to by their German name Wabendichtung, play a crucial role in various industrial applications, providing essential sealing solutions that contribute to the efficiency and reliability of machinery and equipment. A comprehensive understanding of their applications, materials, and technological advancements offers valuable insights into their significant contributions to the industry.
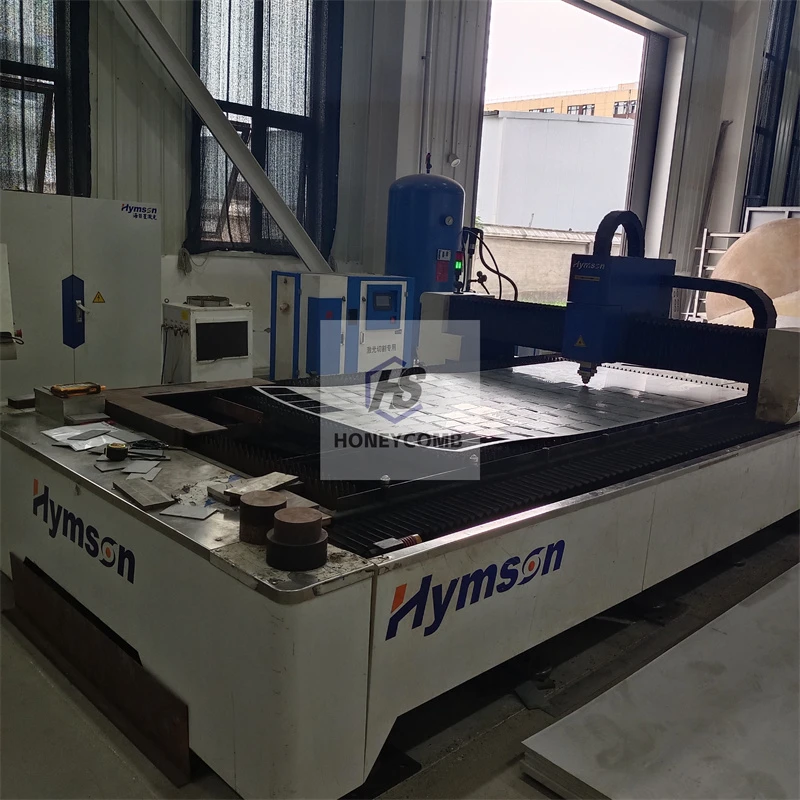
Dynamic seals are primarily used to contain fluids, prevent leakage, and maintain pressure in rotating and reciprocating equipment. Their versatile applicability spans industries such as automotive, aerospace, manufacturing, and energy, where they ensure the seamless operation of engines, pumps, compressors, and other critical machinery. The effectiveness of a dynamic seal lies in its ability to handle friction, pressure fluctuations, temperature variations, and other operational stresses, ensuring that mechanical components function smoothly and without interruption.
Material selection for dynamic seals is a pivotal aspect of their design and function. Different applications necessitate specific material properties to withstand environmental and operational conditions. Common materials used include rubber, polymers, and advanced composites, each offering distinct advantages. Rubber seals, often used for their elasticity and resilience, provide excellent sealing performance in low to moderate temperatures. In contrast, high-performance polymers and composites offer superior thermal stability, chemical resistance, and reduced wear, making them ideal for more demanding environments.
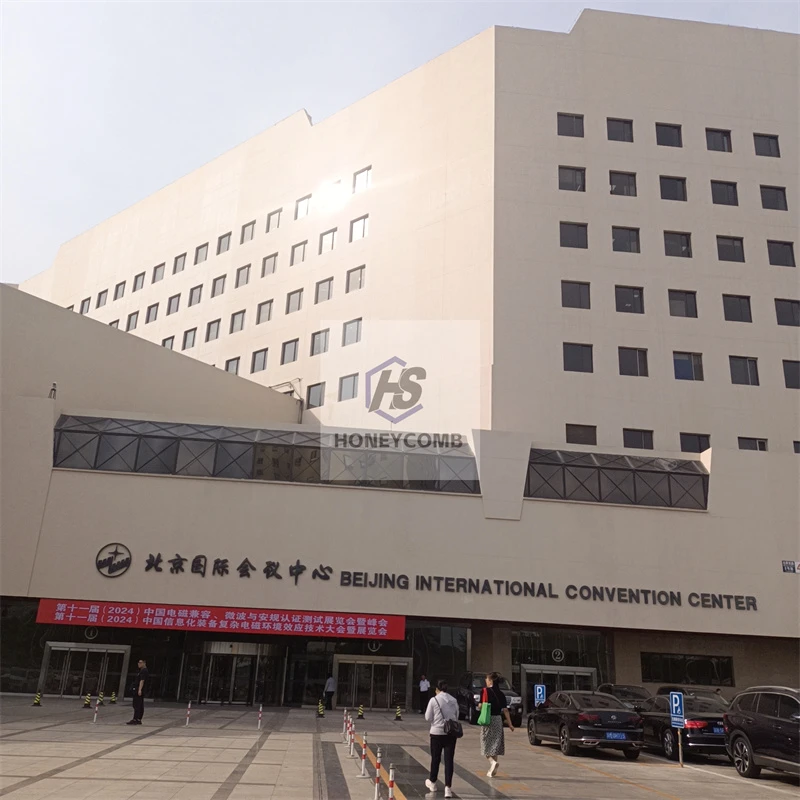
The advancement in dynamic seal technology is noteworthy, particularly in the context of efficiency and sustainable practices. Recent innovations in material science have led to the development of seals capable of operating under extreme conditions, such as high-speed rotations and high-temperature environments. These advancements are crucial in industries striving for greater energy efficiency and reduced environmental impact. In the automotive industry, for example, dynamic seals contribute to improved engine efficiency and reduced emissions by minimizing leakage and energy loss, aligning with global trends towards sustainability and environmental responsibility.
A critical factor contributing to the effectiveness of dynamic seals is the precision in their design and manufacturing. Advanced computer-aided design (CAD) technologies enable engineers to simulate various conditions, allowing for the optimization of seal geometry and material properties. These simulations help predict the seal's behavior under different loads, speeds, and temperatures, ensuring that the final product meets the stringent requirements of modern industrial applications. Furthermore, precision manufacturing techniques, such as injection molding and CNC machining, ensure that each seal meets exact specifications, enhancing its reliability and lifespan.
wabendichtung
The expertise required to develop and implement dynamic sealing solutions underscores the importance of specialized knowledge and technical proficiency. Engineers and designers must possess a deep understanding of material science, mechanical engineering, and fluid dynamics to create seals that not only meet functional requirements but also contribute to the overall efficiency of machinery. Collaboration between material scientists, mechanical engineers, and manufacturers ensures that dynamic seals adhere to the highest standards of quality and performance.
Authoritativeness in the field of dynamic sealing technologies is maintained through adherence to international standards and rigorous testing protocols. Organizations such as the American Society for Testing and Materials (ASTM) and the International Organization for Standardization (ISO) provide guidelines to ensure that products meet global safety and quality benchmarks. Compliance with these standards is essential for manufacturers aiming to compete in a global marketplace, where reliability and quality are non-negotiable.
Trustworthiness in the performance of dynamic seals is established through a combination of extensive field testing, customer feedback, and continuous improvement in design and materials. Manufacturers often conduct field trials and long-term durability tests to validate the performance of their sealing solutions under real-world conditions, addressing potential challenges that may arise during operation. The feedback loop from end-users is invaluable, providing insights into potential areas for enhancement and innovation.
In conclusion, the realm of dynamic seals or Wabendichtung exemplifies the intersection of engineering expertise, material science innovation, and sustainable industrial practices. As industries continue to evolve, the demand for high-performance, reliable, and efficient sealing solutions will only intensify, driving ongoing research and development in this critical field. By focusing on experience, expertise, authoritativeness, and trustworthiness, manufacturers of dynamic seals can ensure that their products meet the current and future needs of a broad range of industrial applications, contributing to the advancement of modern technology and engineering.