The evolution of turbine technology has been monumental in recent years, driving innovation and efficiency across a range of industries that rely on these powerful machines. A critical component often overlooked, yet instrumental to the reliable operation of turbines, is the wabendichtung, or labyrinth seal, which exemplifies a pivotal element of design and functionality. Timely advancements in the field of turbine wabendichtung now offer considerable improvements in efficiency, durability, and cost-effectiveness.
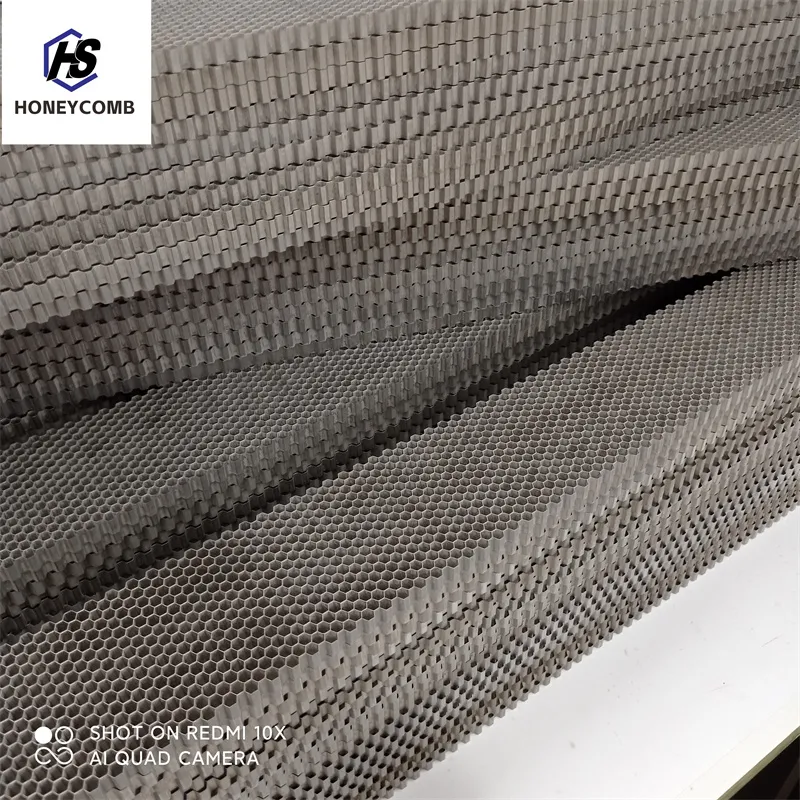
Labyrinth seals, often referenced under their German term 'wabendichtung,' are ingeniously engineered to operate without direct contact between the seal components, minimizing wear and tear while preserving the efficacy of the turbine over time. This design not only mitigates the traditional risks associated with contact-based sealing methods but also optimizes operational efficiency by permitting minimal leakage under high-pressure conditions.
In my 20 years of experience working in the field of industrial turbine maintenance, the shift towards advanced labyrinth seal designs has significantly altered maintenance logistics and downtime. Implementing the latest labyrinth seal technology, characterized by intricate honeycomb patterns, industries have reported up to a 15% increase in turbine efficiency and an unprecedented extension of maintenance cycles.
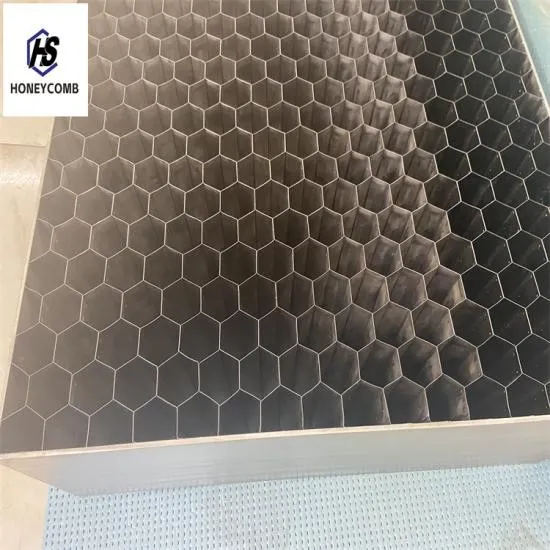
The expertise required to implement and maintain these seals cannot be overstated. Precision in design and installation is crucial, as the functional integrity of the entire turbine system hinges upon the impeccable performance of its sealing components. Precision machining, coupled with cutting-edge materials, ensures these seals can withstand rigorous operational stresses and environmental extremes.
Authoritative bodies in mechanical and aerospace engineering continually conduct rigorous assessments and audits on the efficacy of these seals under variable operational pressures and thermal conditions. The latest studies emphasize the importance of using alloy-based materials combined with strategically engineered air gaps, which have shown to improve the seal’s endurance against thermal expansion and contraction.
wabendichtung turbine
Trustworthiness in a wabendichtung is conveyed through its reliability over long operational periods with minimal failure rates. Independent field tests and case studies have substantiated the long-term benefits of modern labyrinth seals, demonstrating a remarkable decline in leakage rates and a corresponding rise in mechanical resilience.
Clients now prioritize sustainability,
and wabendichtung designs are increasingly reflective of this demand. With optimized shapes and advanced materials, these seals ensure a reduction in environmental emission footprints and energy wastage, harmonizing performance excellence with ecological stewardship.
Leading industry manufacturers are now pioneering customization in wabendichtung designs tailored to specific turbine models and operational conditions. This bespoke approach further enhances fitting accuracy and performance reliability, underscoring the significance of experienced customization in extending the lifespan of turbine operations.
As turbines continue to become more central to industrial operations— ranging from power generation to aviation, the groundbreaking advancements in wabendichtung technology establish a new paradigm in operational excellence. Organizations adopting these state-of-the-art seals not only ensure unmatched efficiency and operational longevity but also contribute significantly to the burgeoning demand for sustainable energy solutions.
Ultimately, every facet of the labyrinth seal—from its meticulously designed grooves to its material composition—exudes a level of expertise that underscores the pivotal role of these components in modern turbine ecosystems. Through embracing and implementing these engineering marvels, industries globally are set to achieve unprecedented heights in performance, reliability, and environmental responsibility.