Unlocking the potential of cutting-edge aerodynamics testing requires state-of-the-art facilities that cater to the evolving needs of modern engineering. Central to these facilities is the wind tunnel honeycomb, also known as windkanal-wabenwabe in German. This seemingly simple yet ingeniously complex component holds the key to more accurate data, enhanced testing capabilities, and more efficient designs in the aviation, automotive, and renewable energy sectors.
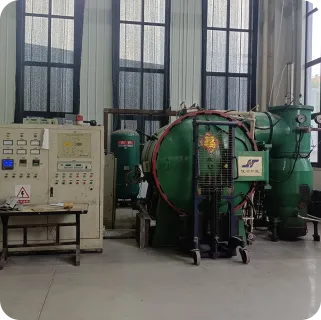
The role of the wind tunnel honeycomb is to ensure the controlled and consistent flow of air before it meets the test section of a wind tunnel. It achieves this by straightening turbulent airflow, reducing turbulence intensity, and distributing the flow evenly. These factors are crucial in replicating real-world conditions within the controlled environment of a wind tunnel.
From an engineering perspective, the design of the honeycomb is no small feat. It requires a precise balance between cell size, length, and materials to meet the specific needs of different tests. Engineers prefer materials like aluminum or composite materials because they provide a good balance between strength and weight. The cells of the honeycomb typically range from 0.125 inches to 1 inch in diameter, with lengths between 3 to 10 inches. This design variability allows engineers to tailor the honeycomb to the specific Reynolds number and Mach number of the test, ensuring high correlation between experimental and real-world conditions.
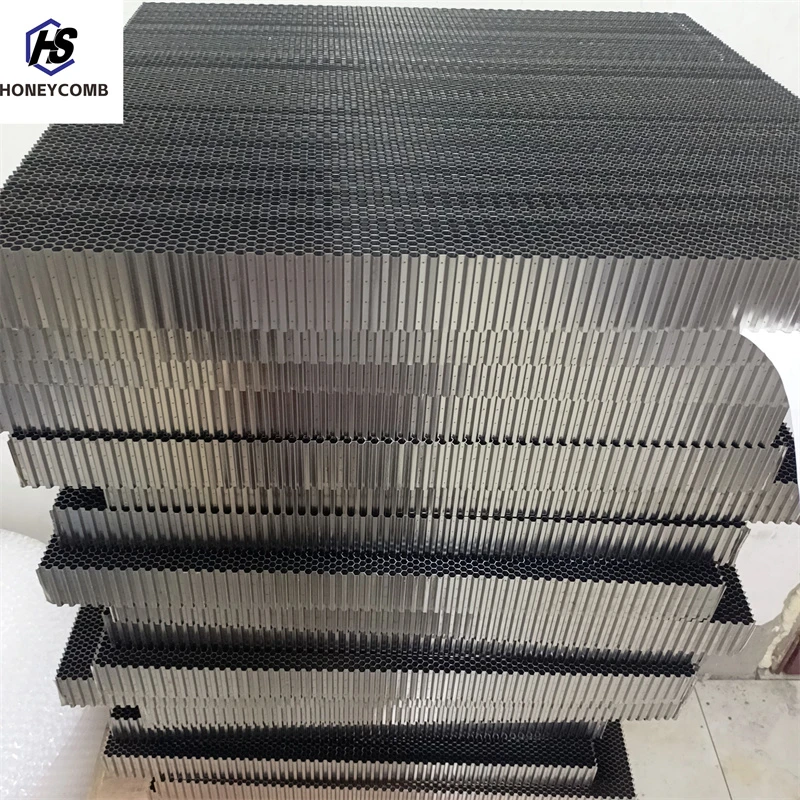
One area where windkanal-wabenwabe plays a pivotal role is in the automotive industry. As manufacturers strive for more fuel-efficient and aerodynamic vehicles, wind tunnels equipped with efficient honeycombs become indispensable. They facilitate the testing of vehicle aerodynamics, leading to designs that minimize drag and maximize performance. The precision that honeycombs offer in airflow regulation directly translates into more reliable data and, ultimately, more aerodynamic vehicle shapes.
In the realm of aviation, where safety and efficiency are paramount, the wind tunnel honeycomb is integral to testing new wing and fuselage designs. With the global push towards more sustainable aviation, particularly the development of electric aircraft, accurate wind tunnel testing using advanced honeycomb systems ensures that these future-forward designs are as efficient and safe as possible. The meticulous control of airflow allows for more refined adjustments to wing profiles and structural layouts, without resorting to costly flight trials.
windkanal-wabenwabe
The renewable energy sector, especially wind energy, also benefits significantly from advanced wind tunnel honeycombs. With the world leaning towards sustainable power sources, optimizing the design and efficiency of wind turbines has never been more critical. Testing in wind tunnels fitted with sophisticated honeycomb structures allows engineers to fine-tune turbine blade design to ensure they capture maximum energy with minimal mechanical stress, directly impacting the energy return on investment and longevity of turbine installations.
Trust in these systems is built on years of empirical research and practical application.
Engineers and scientists like Dr. Hans Müller, a pioneer in wind tunnel technology, highlight the importance of precision in their research. Dr. Müller’s work, widely published and respected, underscores the role of honeycomb technology in reducing airflow distortion and improving data fidelity. This expert endorsement strengthens the credibility of windkanal-wabenwabe systems and assures industries of its reliability.
Moreover, industry experience demonstrates the trustworthiness of windkanal-wabenwabe systems. Companies like Airbus and Ford have long relied on wind tunnel honeycombs to refine their products. Their consistent use of these systems, supported by comprehensive data analyses, demonstrates the invaluable contribution of honeycombs to product development and optimization.
In conclusion, the wind tunnel honeycomb, or windkanal-wabenwabe, stands as a testament to the power of precision engineering. Its impact on various sectors underscores its importance in more sustainable, efficient, and innovative design and testing environments. By ensuring accurate, reliable, and trustworthy data, it paves the way for groundbreaking advancements across industries, marking its place as an indispensable tool in modern engineering.