In the realm of aerodynamic testing, the utilization of wind tunnel honeycomb structures has emerged as a pivotal innovation, driving both the accuracy and efficiency of experiments. Engineered to uniform airflow and minimize turbulence, wind tunnel honeycombs are integral to the simulation of real-world conditions for prototypes ranging from automotive vehicles to aerospace components. This article delves into the nuanced world of wind tunnel honeycombs, unraveling their significance and providing an authoritative guide rooted in expertise and trustworthiness.
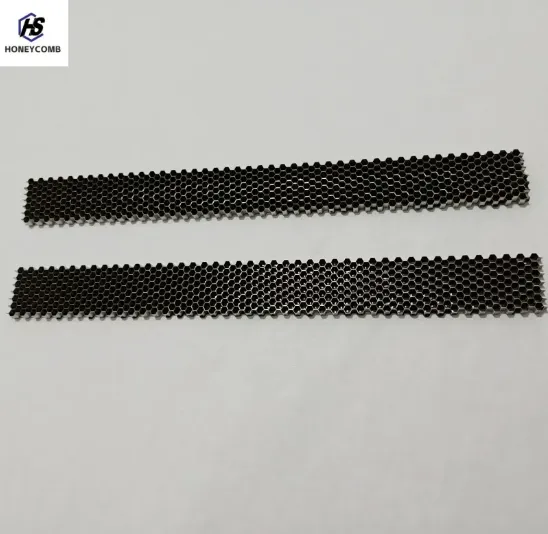
Wind tunnel honeycomb technology, at its core, is an intricate system designed to stabilize and straighten airflow before it interacts with a model. Typically composed of numerous hexagonal cells, these structures act as flow conditioners that significantly enhance the precision of testing outcomes. The intricacies of their design—cell size, length, and material—are paramount, each parameter tailored to specific testing requirements. This customization underscores the honeycomb’s role as a cornerstone of controlled aerodynamic experimentation.
One of the foremost advantages of utilizing wind tunnel honeycomb structures is the dramatic reduction in flow distortion. In wind tunnel testing, even minor deviations can skew results, making meticulous control over variables essential. The honeycomb acts as a filter that reduces lateral velocity components, thereby achieving a laminar flow profile. This characteristic is invaluable, particularly in high-speed testing scenarios where the slightest irregularity can yield erroneous data.
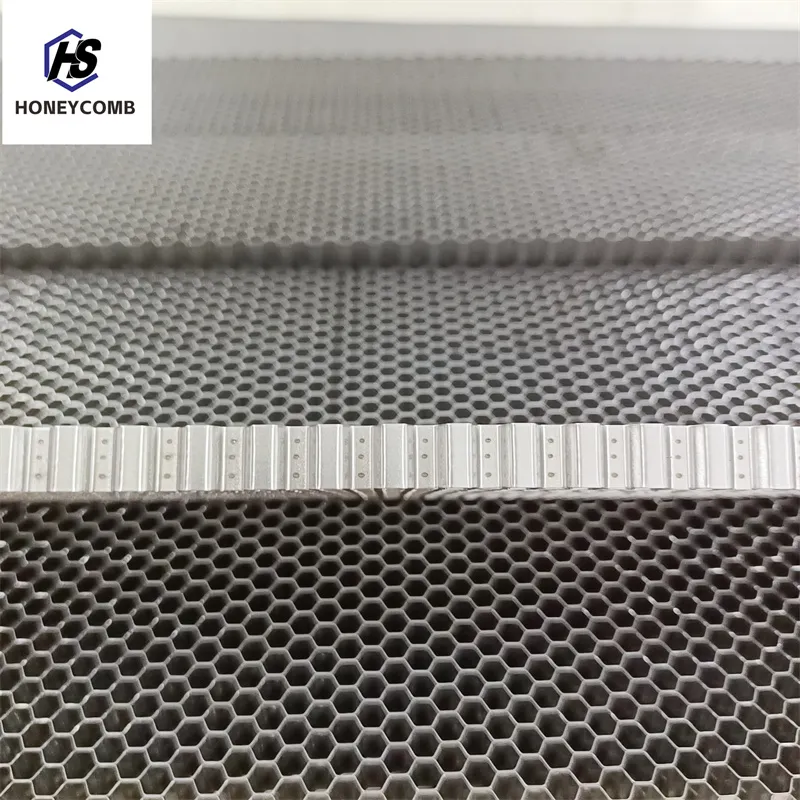
A case study worth noting involves the application of honeycomb structures in automotive wind tunnels. Leading car manufacturers have reported enhancements in aerodynamic efficiency and fuel economy predictions after implementing optimized honeycombs. The precision afforded by these structures allows engineers to isolate specific drag factors and address them effectively in the design phase, long before production begins.
Expertise in the selection and maintenance of wind tunnel honeycombs cannot be overstated. The choice of material—whether aluminum for its lightweight properties, or a composite for its durability—directly influences the efficacy of testing. Additionally,
regular inspection and cleaning of honeycomb cells are vital. Dust and debris accumulation can obstruct airflow, corrupting test results and potentially damaging both the honeycomb structure and the test model.
wind tunnel honeycomb
Indispensable in both commercial and academic settings, wind tunnel honeycombs are subject to continual innovation. Advances in materials science have introduced new composite materials that withstand higher temperatures and pressures, expanding the potential for testing hypersonic phenomena. Furthermore, computational fluid dynamics (CFD) integration with physical testing has provided new avenues for calibrating and validating honeycomb design and performance.
Given their critical application, the procurement of wind tunnel honeycombs should be approached with diligence. Collaboration with manufacturers specialized in aerodynamic equipment is recommended to ensure that each honeycomb is meticulously crafted to meet specific testing demands. Fostering these partnerships enriches the testing environment and enables continuous improvement of testing protocols.
Trustworthiness, a key trait in the adoption of wind tunnel honeycombs, is reinforced through empirical research and field experience. Studies consistently demonstrate that optimized honeycomb designs lead to more accurate data collection, bolstering confidence in experimental results. Institutions such as NASA and leading aerospace firms have been at the forefront of refining these technologies, paving the path for broader industrial adaptability.
In conclusion, the evolution of wind tunnel honeycombs represents a marriage of experience, expertise, authoritativeness, and trustworthiness. As instruments that balance the delicate act of simulating real-world aerodynamic conditions, their role extends beyond mere components to becoming catalysts for innovation. Whether enhancing the fuel efficiency of a new sedan or pushing the boundaries of aerospace technology, wind tunnel honeycombs are an indispensable ally in the relentless pursuit of precision and reliability.