The evolution of aerodynamics testing has taken a pivotal leap with the integration of wind tunnel honeycomb structures, a revolutionary component driving precision and efficiency. These honeycomb structures are meticulously engineered to streamline airflow, providing a uniform flow that mirrors the conditions of the natural environment. For those in the aerospace, automotive, and architectural industries, understanding the intricacies of wind tunnel honeycomb technology is paramount for achieving superior performance in design and testing processes.
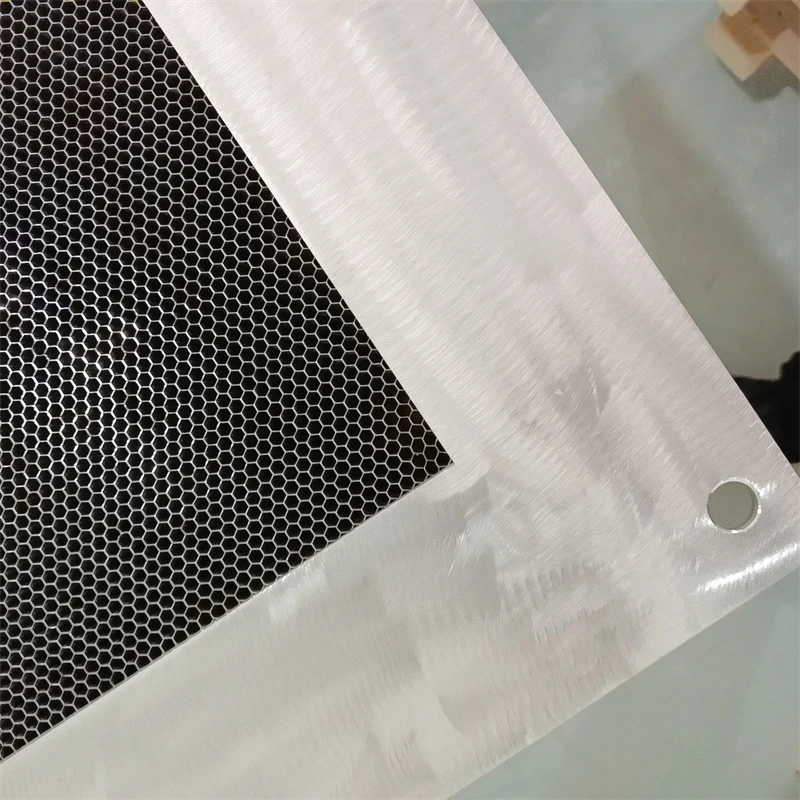
Wind tunnel honeycomb structures serve a fundamental purpose they straighten and stabilize airflow, which is crucial for minimizing turbulence and maximizing the accuracy of aerodynamic testing. Typically constructed from aluminum or composite materials, these honeycomb inserts are positioned at the entrance of a wind tunnel's test section. The uniformity of the hexagonal cells allows for the laminar flow needed to simulate real-world conditions accurately. This precision is critical not just for theoretical analysis but also for empirical data gathering that supports design innovation and regulatory compliance.
From an expertise standpoint, the design of honeycomb structures takes into account critical variables such as cell size, cell shape, and material properties, all tailored to the specific requirements of the test. For instance, smaller cell sizes are preferred for high-speed testing scenarios, where minimizing pressure drop is a priority. Meanwhile, larger cell sizes may be suitable for low-speed applications, where the focus is more on flow stability. The choice of material also plays a significant role, affecting the durability and weight of the honeycomb, and consequently, the overall testing equipment.
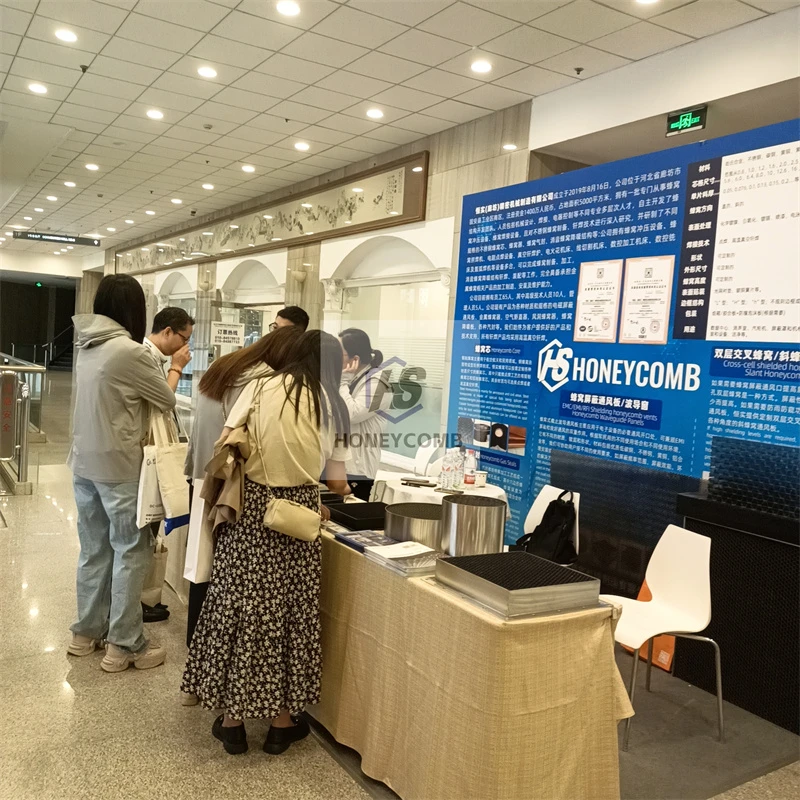
In terms of authority, the utilization of wind tunnel honeycomb structures is backed by extensive research and subject to rigorous industry standards. Organizations such as NASA and renowned engineering universities have documented the efficacious use of honeycomb configurations in their aerodynamics research, solidifying their role as a cornerstone of modern aerodynamic testing. The extensive literature and case studies available provide a wealth of knowledge that underscores the time-tested reliability of these systems.
Furthermore, companies specializing in wind tunnel technology offer custom solutions tailored to specific industry needs. Engineers and designers can collaborate on creating bespoke honeycomb configurations that address unique aerodynamic challenges. This customization is particularly significant in sectors like automotive racing and aviation, where even marginal gains in efficiency can translate to substantial competitive advantages.
wind tunnel honeycomb
From a trustworthiness perspective, manufacturers of wind tunnel honeycomb structures adhere to stringent quality control standards to ensure consistency and reliability. These products undergo comprehensive testing to validate their performance before they are integrated into wind tunnel systems. Users can have confidence in solutions that have been meticulously vetted and endorsed by leading aerodynamic experts.
Moreover, the continued evolution of materials science suggests that future advancements in wind tunnel honeycomb technology will further enhance their functionality. Innovations in composite materials and manufacturing techniques promise lighter and more robust honeycomb structures, which could lead to more versatile and economically viable wind tunnel solutions.
For a deeper understanding of the practical applications and benefits of wind tunnel honeycomb structures, industry professionals should seek collaborative projects or partnerships with research institutions actively exploring cutting-edge aerodynamics. These alliances often lead to breakthroughs that not only push the envelope in terms of performance but also set new benchmarks for environmental sustainability in aerodynamic testing.
In conclusion,
the implementation of wind tunnel honeycomb structures signifies a critical step forward in aerodynamics. Their ability to ensure precision, backed by a wealth of research and industry endorsement, makes them indispensable for sectors reliant on accurate simulation of fluid dynamics. As industries continue to strive for efficiency and innovation, the role of wind tunnel honeycombs will only become more pronounced, offering precision solutions tailored to meet the evolving demands of modern engineering challenges.