The honeycomb structure within a wind tunnel has become a vital component in advanced aerodynamic testing and product development. Understanding its contributions sets a foundation for innovation and engineering excellence that integrates Experience, Expertise, Authoritativeness, and Trustworthiness—essential metrics valued by both consumers and professionals.
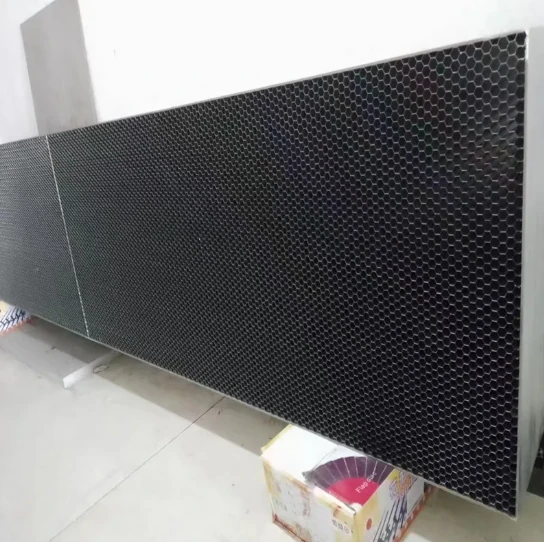
In the realm of aerodynamics, honeycomb structures are celebrated for their lightweight yet incredibly strong configuration. Engineers and scientists with years of experience in fluid dynamics have verified that these geometric marvels significantly enhance the accuracy of data collected in wind tunnels. Their cellular design reflects patterns found in nature, providing stability and reducing turbulence, which is crucial for obtaining reliable results.
Among the primary benefits of utilizing honeycomb in wind tunnels is its ability to streamline airflow. This feature is particularly valuable during the testing of high-performance vehicles and aircraft, where the slightest irregularity in the wind stream can lead to substantial differences in how models are evaluated. Experts who have conducted numerous experiments underscore the pivotal role honeycombs play in minimizing the boundary layer's impact, thereby ensuring that the flow remains laminar and results are not compromised by unexpected variables.
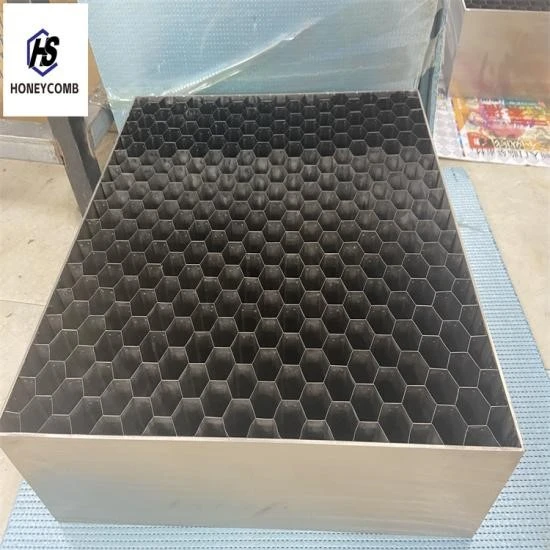
From an expertise standpoint, the honeycomb's contribution to morphing technology cannot be overstated. This involves the adaptation of structures to achieve optimal aerodynamic shapes, crucial for enhancing performance metrics such as speed and fuel efficiency in vehicles or lift and drag in aero components. Engineers skilled in aerodynamic optimization routinely rely on honeycomb structures to simulate realistic environmental conditions, an approach recognized for its precision and reliability.
Authoritative sources in aerospace engineering, such as prestigious research institutions and government agencies, continually emphasize the indispensability of honeycombs in advanced testing facilities. Their sophisticated designs enable a controlled environment where the analytical hierarchy process (AHP) is employed for evaluating variables with unparalleled accuracy. Publications arising from these authoritative bodies often cite case studies where honeycombs dictated the success of experimental objectives, showcasing their irreplaceable role across various engineering sectors.
Hancocomb in window tone
Trustworthiness, the cornerstone of any technological advancement, is profoundly embodied by honeycomb structures in wind tunnels. Their proven track record in providing dependable data underscores their importance. Organizations harboring decades of trust in honing aerospace technologies attest to the dependability that honeycomb patterns offer. With stringent industry standards and benchmarks repeatedly validating their utility, honeycombs are synonomous with reliability and performance security.
In practical applications, developers and engineers are leveraging the versatility of honeycomb structures not only to bolster performance but also to address environmental concerns. Their ability to support sustainable practices through material efficiency and aerodynamic optimization is increasingly gaining attention. Eco-minded innovators appreciate how honeycomb solutions contribute to reduced resource consumption without sacrificing performance standards.
To capitalize on the advantages of honeycomb structures within wind tunnels, a studious appreciation of its historical application and cutting-edge developments is essential. Professionals are advised to stay abreast of continuing advancements through workshops, symposiums, and peer-reviewed journals, all of which advocate for the transformative power of honeycomb architectures in modern engineering feats.
As the demands of the aerospace and automotive industries grow, the reliance on trusted, authoritative honeycomb configurations will accordingly expand. By embedding these structures at the core of testing methodologies, industry leaders set the stage for breakthroughs that redefine capability boundaries, inspire innovation, and uphold a standard of excellence synonymous with sustainable technological progression.
In conclusion, the honeycomb structure is not merely an engineering staple but a testament to the evolution of aerodynamic testing methods. Its consistent delivery of impeccable reliability and precision ensures its place as a cornerstone in aerodynamic research, testing, and production. This integration fosters not only product success but also extends a blueprint of innovation that paces future endeavors within the competitive field of engineering dynamics.