Stainless steel honeycomb structures have consistently proven their worth in diverse industrial applications due to their remarkable strength-to-weight ratio, corrosion resistance, and thermal management properties. Engineers and architects alike are harnessing these attributes to develop solutions that address complex engineering challenges, and extensive experience in the field confirms their status as a staple in construction and manufacturing.
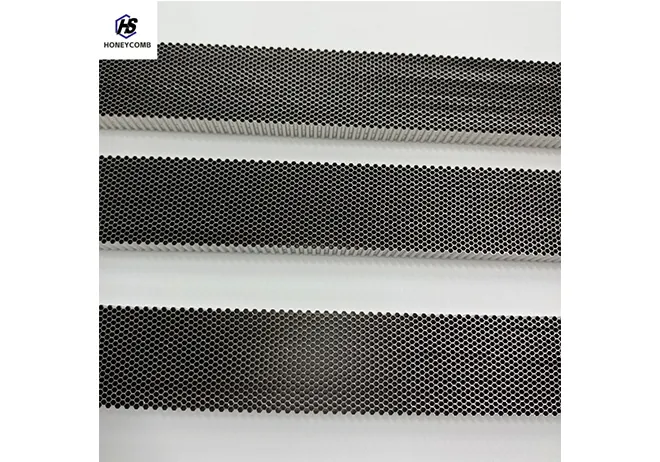
The experience with stainless steel honeycombs often begins with acknowledging their unparalleled efficiency in minimizing material usage while maximizing strength. For industries such as aerospace and automotive, where every gram affects the performance or efficiency of the machinery, stainless steel honeycombs provide a lightweight yet robust solution. This ability to maintain integrity under significant stress and strain is rooted in the fundamental design of the honeycomb structure, which dissipates force evenly across its surface, offering resilience and durability.
Expertise in working with stainless steel honeycomb structures extends to customization and adaptability. Due to their modular nature, these materials can be tailored to fit specific requirements, accommodating various design constraints and operational specifications. Industry professionals have innovated ways to incorporate these structures into soundproofing, reducing noise pollution in urban development projects, or optimizing thermal efficiency in HVAC systems within cutting-edge green buildings. Their versatility aids designers in achieving performance benchmarks while adhering to environmental standards.
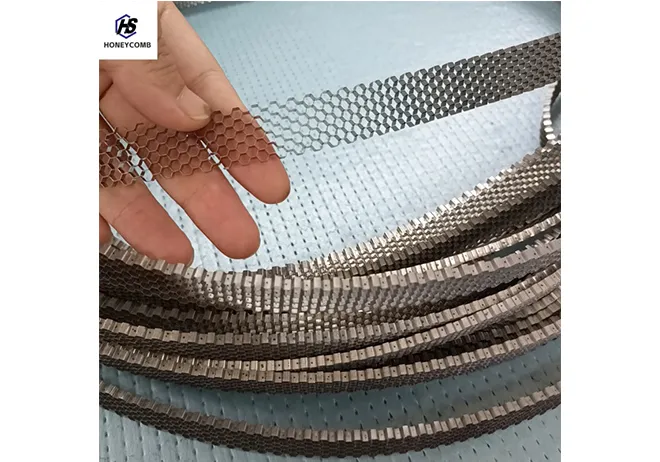
Furthermore, authoritative insights from leaders and scholars in material science underscore the evolution and future potential of stainless steel honeycomb structures. The ongoing research is unlocking newer applications in renewable energy sectors. For instance, in solar panel arrays and wind turbine components, the honeycomb's efficiency contributes to greater energy yield and consistent power output. Cutting-edge studies illustrate how the integration of these materials can lead to innovations in material hybrids, pushing the boundaries of existing technology with increased energy sustainability.
Stainless steel honeycomb
Trustworthiness in utilizing stainless steel honeycombs is reinforced through rigorous testing and real-world applications that adhere to stringent safety and performance standards. The manufacturing processes for these structures are certified to ensure quality and reliability, gaining the trust of engineers and consumers alike. Case studies across diverse industries repeatedly showcase how failures are minimal, if not non-existent, illustrating a consistent pattern of reliability.
In the construction sector, skyscrapers and massive infrastructures are implementing stainless steel honeycombs not just for their strength and aesthetic versatility, but for economic efficiency over longer life cycles. The cost-effectiveness coupled with low maintenance appeals to developers aiming for sustainable investment. Historical data consistently show that projects utilizing these materials often experience reduced repair costs and extended intervals between inspections, making them a preferred choice for long-term projects.
Moreover, the aesthetic qualities of stainless steel honeycomb panels provide architects with a visually appealing and modern design element, aligning with contemporary architectural trends. They are frequently used in facades, interior wall claddings, and ceiling applications, offering a sleek finish that blends seamlessly with modern urban landscapes.
In summary, the use of stainless steel honeycomb structures in industrial applications highlights an exceptional blend of experience, expertise, authoritativeness, and trustworthiness. These materials continue to spearhead advancements in engineering and design due to their adaptive nature and enduring performance characteristics. As industries push forward into the future, stainless steel honeycombs will undoubtedly play a crucial role in meeting the evolving demands of sustainable and resilient construction and manufacturing practices.