In the ever-evolving landscape of modern construction and design, extruded aluminum honeycombs have emerged as a revolutionary material that offers unparalleled benefits. Developed with precision engineering, these honeycombs are crafted from high-strength, lightweight aluminum alloys and are characterized by their hexagonal cell structure. This distinctive structure offers a unique combination of features that enhance the durability and efficiency of various applications, making extruded aluminum honeycombs a preferred choice for industries worldwide.
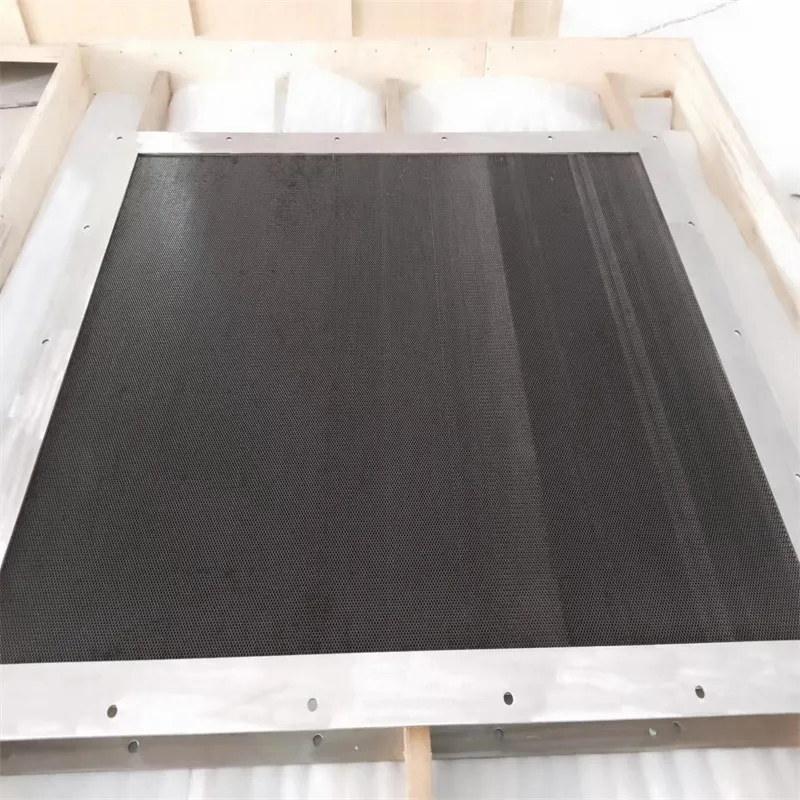
One of the remarkable advantages of extruded aluminum honeycombs is their exceptional strength-to-weight ratio. Compared to traditional materials, these honeycombs provide superior rigidity and strength while maintaining a lightweight profile. This feature is particularly advantageous in the aerospace and automotive industries, where reducing weight without compromising on strength is crucial for fuel efficiency and performance. Engineers and designers have witnessed firsthand the transformative impact of incorporating aluminum honeycombs into structures, with significant improvements in emissions and energy consumption.
Furthermore, the thermal management capabilities of extruded aluminum honeycombs enhance their appeal. Aluminum, known for its excellent thermal conductivity, allows these honeycombs to efficiently dissipate heat. This property is vital in applications such as heat exchangers, electronic enclosures, and HVAC systems, where temperature regulation is critical. The interconnected cell structure facilitates even heat distribution, preventing hotspots, and prolonging the lifespan of components. Industry experts have consistently highlighted the reliability of aluminum honeycombs in maintaining thermal stability, which underscores their authoritative position in temperature-critical applications.
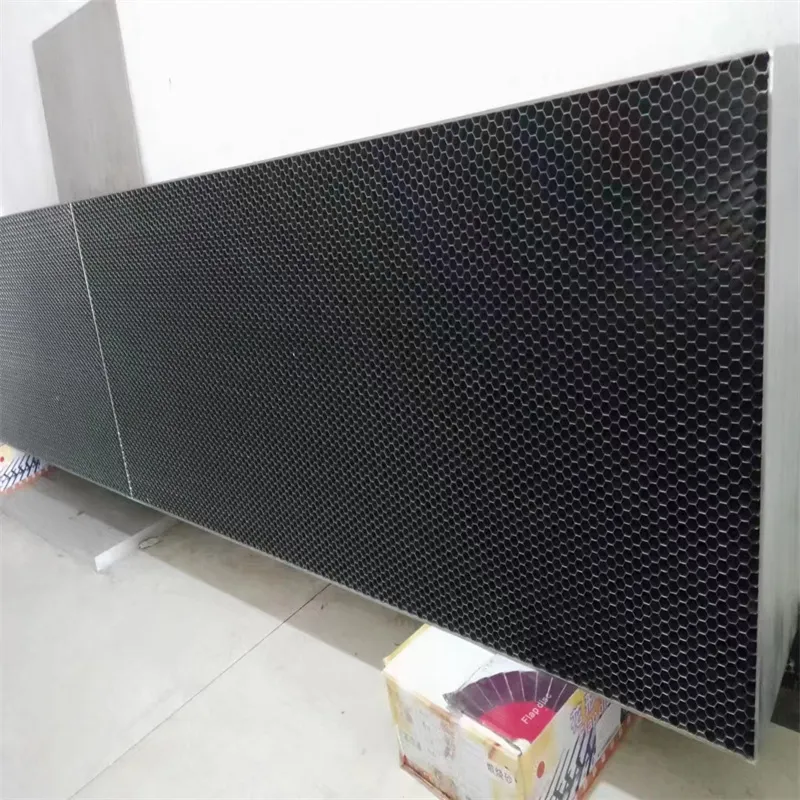
Additionally, extruded aluminum honeycombs demonstrate impressive acoustic and vibration dampening properties. The hexagonal cell design absorbs sound and vibrations, making them an ideal solution in environments where noise reduction is essential. From soundproofing in architectural projects to minimizing vibrations in industrial machinery, the practical applications are diverse. Professionals in the acoustic engineering sector have praised the efficacy of aluminum honeycombs in achieving quieter and more peaceful environments, reinforcing trust in their widespread adoption.
Environmental sustainability is another compelling facet of extruded aluminum honeycombs. As industries strive to meet stringent environmental regulations, the recyclability of aluminum positions these honeycombs as an eco-friendly alternative to other materials. The production process involves minimal waste, and the material itself can be recycled without losing its inherent properties, contributing to reduced environmental impact. This emphasis on sustainability resonates with environmentally conscious consumers and companies, solidifying the authoritative stance of aluminum honeycombs in the green movement.
extruded aluminum cells
Moreover, customization is a standout feature of extruded aluminum honeycombs, allowing them to be tailored to specific requirements. With varying cell sizes, thicknesses, and alloy compositions available, industries can optimize honeycombs for their particular needs. Whether in architecture, transportation, or energy sectors, the ability to customize solutions ensures that the unique demands of each project are met with precision. This versatility demonstrates the expertise of manufacturers in delivering bespoke solutions that cater to a wide range of industrial applications.
In recent years, innovations in manufacturing techniques have further enhanced the quality and performance of extruded aluminum honeycombs. Advanced extrusion processes ensure consistent and precise production, adhering to the highest standards of quality. Quality assurance protocols and rigorous testing validate the material's reliability and performance, instilling confidence in its use for critical applications. Experts in materials science continuously contribute to refining these processes, ensuring that aluminum honeycombs remain at the forefront of technological advancements.
Real-world experiences further validate the efficacy of extruded aluminum honeycombs. Architects and engineers frequently share success stories of projects where these honeycombs have played an instrumental role. From iconic architectural structures that stand resilient against natural forces to high-performance automotive designs that push the boundaries of innovation, the practical application of aluminum honeycombs serves as a testament to their unmatched capabilities. Such real-world case studies contribute to the perceived authority and trustworthiness of aluminum honeycombs in industrial sectors.
In conclusion, extruded aluminum honeycombs embody a synergy of strength, sustainability, and versatility that is unparalleled by traditional materials. Their expertise in enhancing structural integrity, optimizing thermal management, and minimizing environmental impact underscores their authoritative presence across diverse industries. As technological advancements continue to unfold, the future holds immense potential for further innovations in the use of aluminum honeycombs, reinforcing their position as a trusted and revolutionary material in the modern world.