Honeycomb panels made from alloys offer a remarkable innovation in material technology, widely acclaimed for their strength, lightweight nature, and versatility. These advanced materials are swiftly gaining traction in a variety of industries, thanks to their unique properties that provide solutions to numerous engineering challenges.
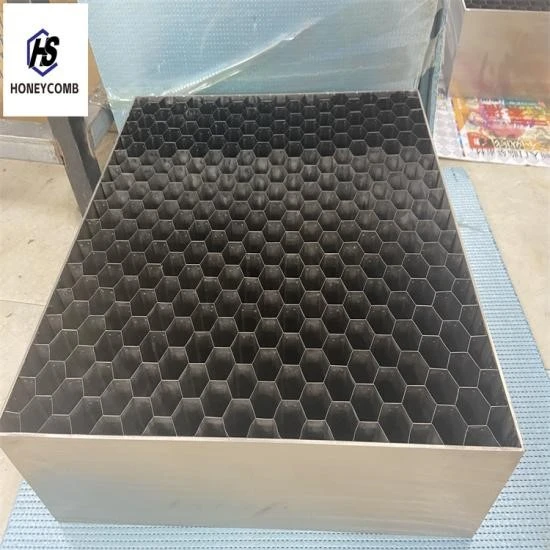
The primary advantage of honeycomb alloy panels lies in their distinctive structure. The honeycomb geometry, characterized by its hexagonal pattern, optimally distributes force, offering exceptional strength while maintaining a lightweight profile. This balance is crucial in sectors such as aerospace, automotive, and construction where reducing weight without compromising durability is essential. The materials used in these panels, such as aluminum or titanium alloys, are chosen for their superior strength-to-weight ratios and corrosion resistance.
In aerospace, for instance, the adoption of alloy-based honeycomb panels has revolutionized aircraft design. They contribute to fuel efficiency by reducing overall aircraft weight, leading to a significant reduction in operating costs and environmental impact. Structural components like wings, fuselages, and flooring systems benefit from the increased stiffness and resistance to deformation provided by these panels. The aerospace industry's trust in these materials is a testament to their reliability and advanced performance.
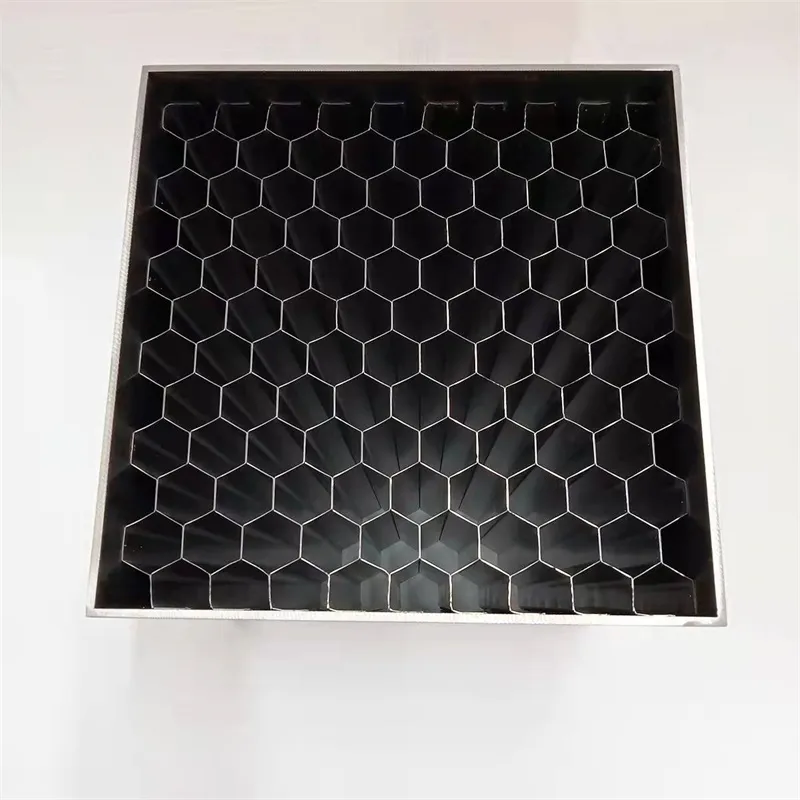
The automotive industry also sees substantial benefits. As the demand for high-performing, energy-efficient vehicles accelerates, manufacturers are turning to honeycomb panels to optimize vehicle dynamics. These panels enhance crash resistance and noise reduction, improving passenger safety and comfort. Moreover, the ability to customize the alloy composition makes it possible to tailor panels to specific vehicle requirements, exemplifying the material's versatility and expertise-driven application.
صفائح قرص العسل المصنوعة من السبائك
Construction is yet another field where honeycomb alloy panels demonstrate significant potential. Their use in facades, flooring, and roofing transforms buildings into resilient structures capable of withstanding harsh environmental conditions. The panels' thermal insulation properties contribute to building energy efficiency, aligning with global movements towards sustainable and eco-friendly construction practices.
From a production standpoint, manufacturers benefit from the streamlined fabrication processes associated with honeycomb panels. Techniques such as adhesive bonding, welding, and riveting facilitate the integration of these components into larger assemblies, enhancing production efficiency and reducing costs. The panels' ease of installation and low maintenance requirements further amplify their appeal across different application domains.
Trust in alloy honeycomb panels is reinforced by rigorous testing and certifications, which validate their structural integrity and performance standards. Organizations implementing these solutions can rely on well-documented research and development efforts, ensuring these products meet the highest industry standards for safety and performance.
In conclusion, honeycomb panels made from alloys embody a fusion of innovative engineering and practical application. Their enduring presence across diverse industries highlights their role as a cornerstone in the evolution of material science. By continually refining these technologies, manufacturers not only enhance their authoritative stance in the field but also contribute to the broader goals of operational efficiency and sustainability.