Understanding the ingenuity of aluminum honeycomb structures is vital not only for professionals within the manufacturing and engineering industries but also for enthusiasts and stakeholders who aim to leverage this innovative technology in various applications. The concept of aluminum honeycomb structure has marked a revolutionary step in material science due to its unmatched combination of strength, flexibility, and lightweight properties. This article explores significant real-world applications, the technical intricacies behind this material, and why it continues to gain traction across multiple sectors, ensuring reliability and performance efficiency.
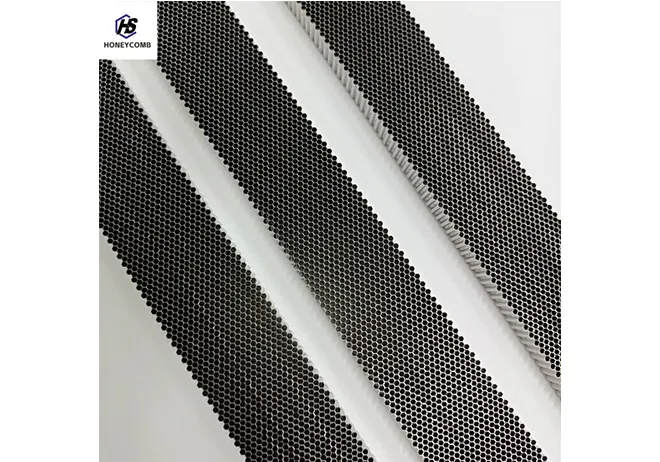
Aluminum honeycomb structures are inspired by nature's efficient ways of creating robust yet lightweight formations, akin to natural honeycombs. These structures consist of an array of hexagonal cells that are meticulously bonded together, offering significant weight reduction without sacrificing strength. This makes aluminum an ideal choice for numerous applications, ranging from aerospace and automotive industries to architectural designs and beyond.
The core benefit of the aluminum honeycomb structure is its incredible strength-to-weight ratio. In aerospace, for example, reducing weight is crucial for fuel efficiency and overall performance. Aircraft components made with aluminum honeycomb panels contribute significantly to the reduced weight of the plane, thus enhancing fuel economy and decreasing operational costs. In automotive sectors, similar principles apply, where aluminum honeycomb structures are increasingly used within car chassis and bodywork to improve safety while maintaining performance.
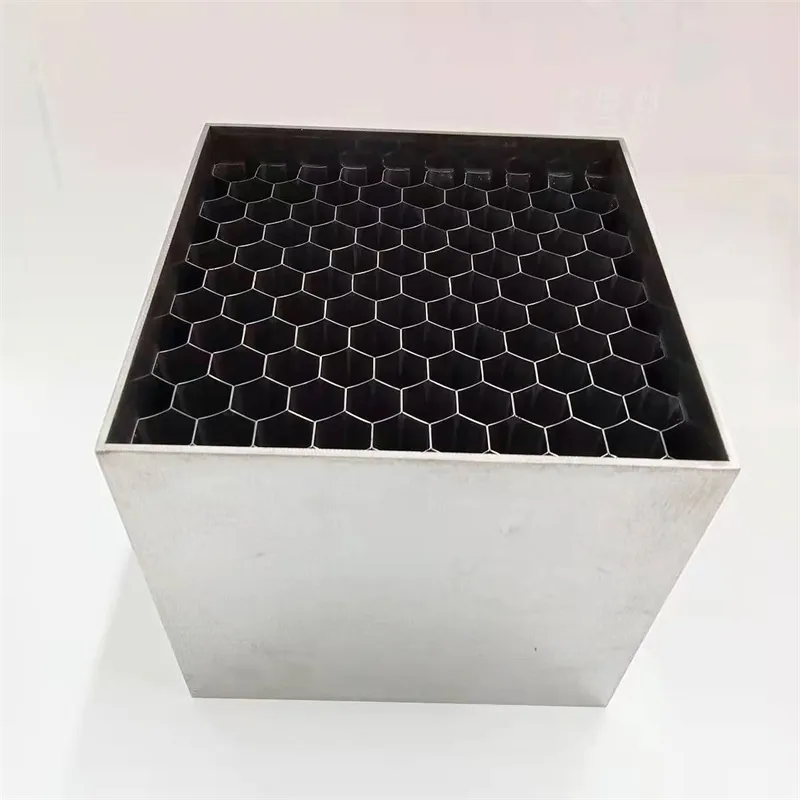
With their exceptional energy absorption capabilities, aluminum honeycomb structures are pivotal in creating safer environments in various modes of transportation. In the event of a collision, honeycomb crash panels within vehicles dissipate energy effectively, thereby reducing the impact force experienced by passengers. This attribute, coupled with the customizable cell size and thickness options, allows manufacturers to tailor specific needs based on energy absorption requirements and safety protocols.
From a technical perspective, producing aluminum honeycomb structures involves a complex manufacturing process that demands expertise and precision. The process begins with the meticulous expansion of aluminum foils into hexagonal cells, followed by the application of high-strength bonding agents that ensure the stability and durability of the honeycomb. Advanced CNC machining tools often enhance precision during fabrication, translating into finished products that meet stringent regulatory standards.
aluminiumwabenstruktur
In architecture, the aesthetic and practical advantages of using aluminum honeycomb structures are compelling. The flexibility of design and ease of installation have led to their increasing use in building facades, ceilings, and floors. Architects appreciate how these structures offer an intriguing balance between contemporary visual appeal and functional resilience. Moreover, the corrosion-resistant properties of aluminum lend themselves well to long-lasting applications in both interior and exterior design elements.
Moreover,
aluminum honeycomb panels are incredibly environmentally friendly. They are recyclable, reducing the carbon footprint associated with the manufacturing and disposal processes. These characteristics align with the growing eco-conscious trends worldwide, driving industries to adopt more sustainable practices and materials.
The expertise involved in fabricating aluminum honeycomb structures extends to precise engineering and thorough knowledge of material properties. Professionals working with these materials must understand the associated technical challenges and design possibilities. Consequently, suppliers and manufacturers who demonstrate high standards of quality and accountability solidify their authoritative position in this realm.
Reliability and trustworthiness in using aluminum honeycomb structures are reinforced through rigorous testing and quality assurance measures. Each product undergoes extensive evaluations, including simulation-based testing for stress and strain distribution, ensuring that it upholds the requisite specifications for its intended application.
In conclusion, aluminum honeycomb structures emerge as an epitome of modern engineering marvels, integrating strength, flexibility, and low weight into one composite material. Their adaptability and efficiency in various industries prove their invaluable contribution to advanced technological developments. As manufacturers continue to explore innovative ways to optimize these materials, aluminum honeycomb structures will undoubtedly maintain their position at the forefront of engineered material solutions, promoting a sustainable, efficient, and safer future for diverse applications.