Aluminum honeycomb structures are revolutionizing the world of lightweight, high-strength materials. In the realm of advanced product design and manufacturing, these structures offer unparalleled benefits in terms of strength-to-weight ratios and versatility, making them indispensable in various industries such as aerospace, automotive, and construction.
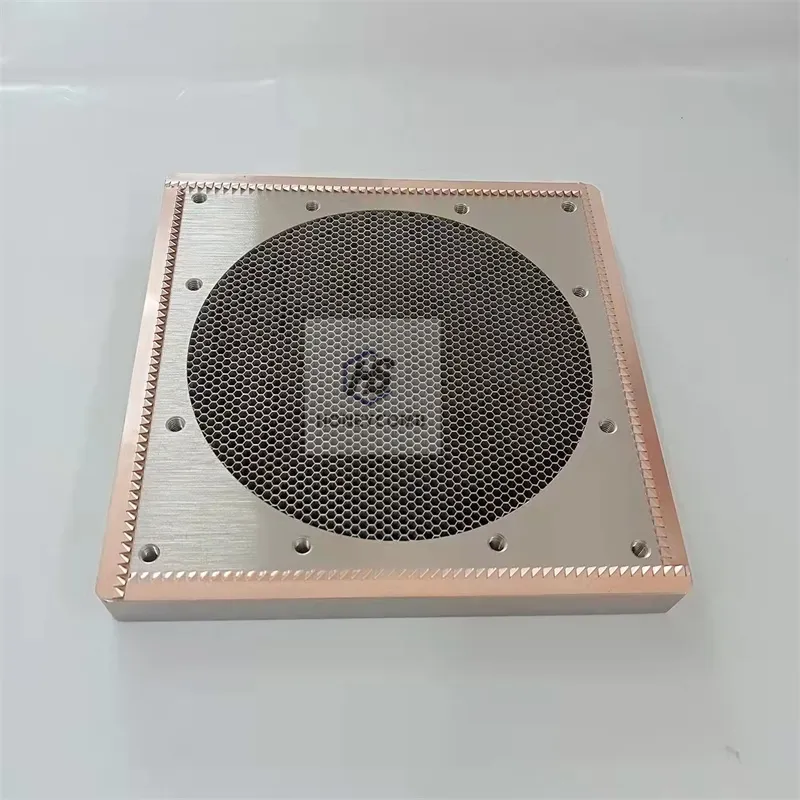
At the heart of aluminum honeycomb structures lies a sophisticated geometric configuration. This configuration is inspired by natural honeycomb, an evolutionary marvel that offers optimal strength while minimizing material use. In engineering terms, honeycomb structures provide excellent rigidity and distribute applied stress uniformly, reducing the risk of material failure. This makes it an attractive choice for engineers and designers aiming to optimize performance while keeping weight in check.
Cost-effectiveness is another compelling feature of aluminum honeycomb structures. Due to their material efficiency, manufacturers can produce strong yet lightweight panels at more affordable costs compared to bulkier alternatives. This affordability doesn't come at the expense of quality; these structures still provide impressive thermal and acoustic insulation, corrosion resistance, and high energy absorption capabilities. Thus, the financial savings extend well beyond production, reflecting in transportation and operational expenses.
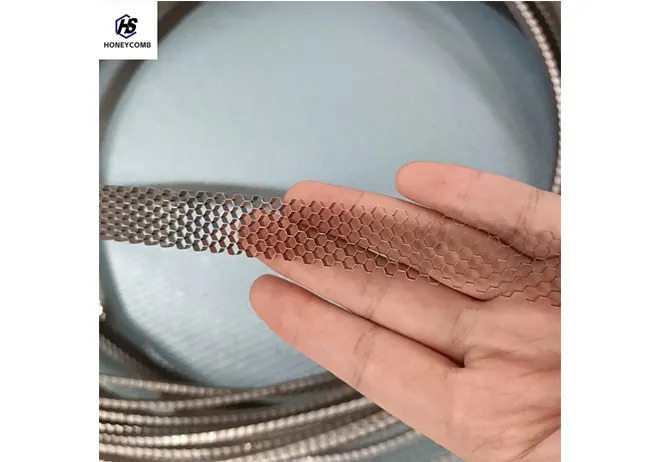
In industries such as aviation, where every gram counts, aluminum honeycomb panels are a favored choice. They form the structural core of aircraft floors, bulkheads, and leading-edge panels, contributing substantially to overall aeronautical efficiency. Their corrosion-resistant properties are particularly valued in this context, ensuring durability and long-term performance even in harsh environmental conditions.
The automotive industry, keen on improving fuel efficiency, sees aluminum honeycomb structures as a game changer. Vehicle components like dashboards, floors, and roof panels can be constructed using this material to drastically reduce weight without sacrificing safety or comfort. This reduction in weight translates directly into improved fuel economy, lower emissions, and enhanced vehicle performance.
bikakestruktur av aluminium
Construction projects, too, are increasingly using aluminum honeycomb paneling to build lightweight structures that don't compromise on safety. The panels can be custom-designed to suit specific architectural needs, providing flexibility and adaptability that traditional materials cannot match. Their resistance to environmental degradation ensures that buildings remain secure and aesthetically pleasing for decades.
As an expert in materials engineering and design, it's crucial to understand the lifecycle of these materials within the context of sustainable development. Aluminum, a highly recyclable metal, makes honeycomb structures an environmentally friendly option. Recycling aluminum requires only a fraction of the energy compared to primary production, thus significantly reducing the environmental footprint.
Trustworthiness and quality assurance are paramount in any application dealing with structural integrity and safety. Reputable manufacturers of aluminum honeycomb structures subject their products to rigorous testing, adhering to international quality standards. Customers can rely on these standards for high performance and safety metrics, ensuring peace of mind whether the material is used in aviation, automotive, or construction.
In conclusion, aluminum honeycomb structures stand out in modern product design for their exceptional strength, versatility, and environmental benefits. As competitive pressures mount across industries to produce lighter, more efficient products, these structures offer an excellent solution. Their evolution from a niche product to a mainstream application speaks volumes about their efficacy and utility. Forward-thinking businesses that integrate aluminum honeycomb structures into their designs are likely to enjoy significant strategic advantages, driving innovation and efficiency in their respective fields.