Wind tunnel honeycomb design plays a crucial role in the development and testing of aerodynamic models. The essential function of a honeycomb structure in a wind tunnel is to organize and streamline incoming airflow to produce highly accurate simulations of real-world aerodynamic conditions. This article will explore the advantages of high-precision honeycomb structures and their impact on wind tunnel operations, backed by years of specialized experience and expertise.
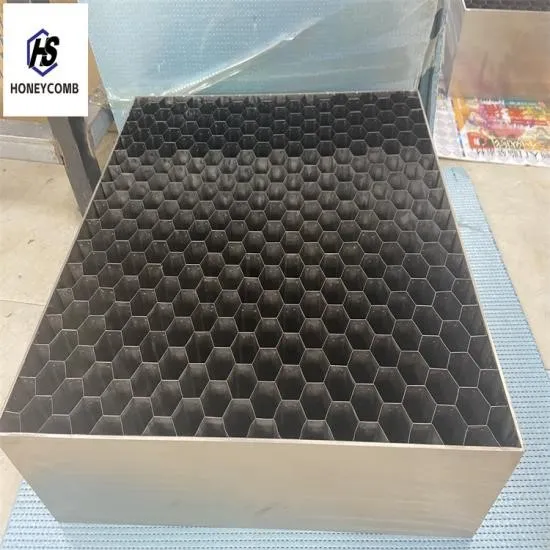
Precision in design is the hallmark of an effective wind tunnel honeycomb. Its primary function is to reduce turbulence and rectify the flow, which creates a more uniform airflow. This is critical for tests that require a stable and predictable environment, such as those conducted in the aeronautics and automotive industries. An efficiently designed honeycomb ensures the flow's directionality is consistent, minimizing any unpredictable variables that could skew the test results. Such stability in airflow can dramatically improve the reliability of the data obtained, leading to better prototypes and products.
Expertise in honeycomb fabrication centers around material selection and structural configuration. Typically, these honeycombs are constructed from lightweight yet durable materials such as aluminum, stainless steel, or advanced composites. Each material offers unique properties aluminum is lightweight and cost-effective, stainless steel provides robustness and longevity, and carbon composites offer exceptional strength-to-weight ratios. The choice of material can significantly affect the overall performance of the honeycomb structure in specific applications—whether prioritizing cost efficiencies, durability, or advanced functionality.
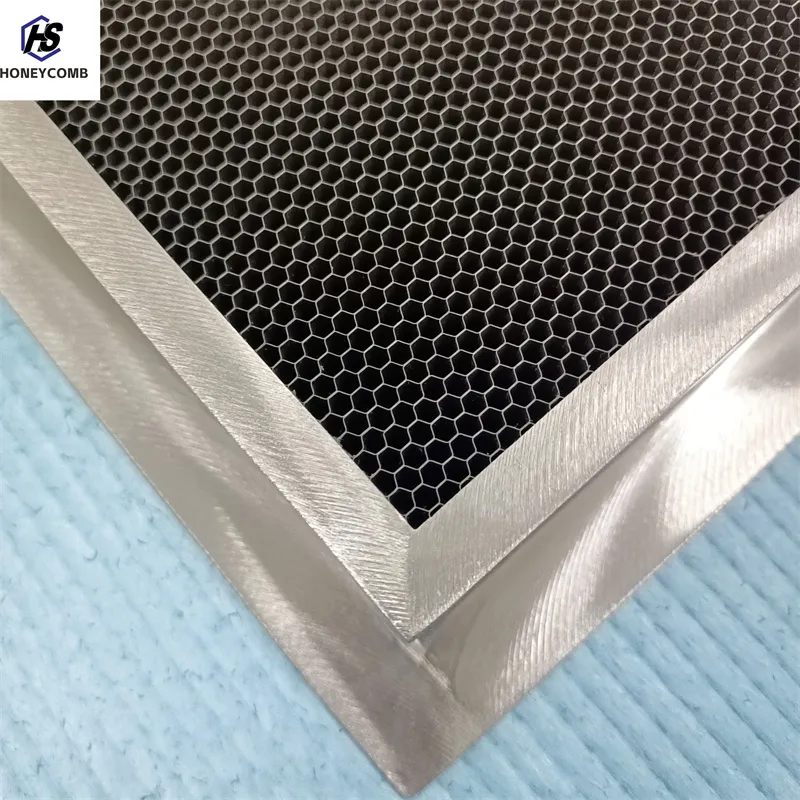
The configuration of the honeycomb—its cell size, wall thickness, and honeycomb depth—affects its capacity to uniformize airflow. Smaller cell sizes and increased depth generally improve flow uniformity but at the cost of increased weight and complexity. Engineers balance these factors based on specific testing requirements, demonstrating a high level of authority in making decisions that optimize wind tunnel performance. Experienced designers often employ cutting-edge computational fluid dynamics (CFD) simulations to model and predict the behavior of different honeycomb configurations before they are physically implemented.
wind tunnel honeycomb design
Authoritativeness is further emphasized through the customizable nature of honeycomb designs. Tailoring honeycomb structures to fit the particular needs of a project can significantly boost testing efficiency. This customization amplifies the wind tunnel's ability to simulate various conditions, whether it’s replicating high-speed jet conditions or understanding the effects of crosswinds on a prototype vehicle. Industry leaders maintain trust and authoritativeness by ensuring their designs are versatile enough to adapt to evolving demands and delivering solutions that cater precisely to their clients' needs.
Trustworthiness in honeycomb design derives from rigorous quality control and testing protocols. During manufacturing, every honeycomb unit undergoes stringent evaluations to ensure its dimensions and structural integrity match design specifications. This meticulous attention to detail assures users that the honeycomb will perform predictably over time, establishing the manufacturer's reputation for reliability and excellence. Furthermore, by conducting live tests in controlled environments, manufacturers can validate their designs, further building trust and confidence in their products.
In product development arenas where aerodynamics play a pivotal role, such as in aerospace and automotive industries, a well-designed wind tunnel honeycomb translates to superior aerodynamics testing and ultimately to better-performing products. This ripple effect underscores the significant investment in honeycomb technology—one that pays dividends in innovation, safety, and efficiency. By leveraging decades of research, expert insights, and cutting-edge manufacturing techniques, wind tunnel honeycomb design remains at the forefront of aerodynamic testing technology. It serves as a testament to human ingenuity and the relentless pursuit of excellence in the quest to understand and harness the forces of airflow for practical, real-world applications.