The expansion of using extruded aluminum honeycomb panels in contemporary construction and design embodies the intersection of innovation, efficiency, and sustainability. As a material with unparalleled structural integrity and lightweight properties, these panels have become indispensable across various domains, offering a blend of aesthetic and functional benefits that are hard to surpass. For those immersed in fields ranging from aerospace to architectural design, understanding the nuances of extruded aluminum honeycomb is vital.
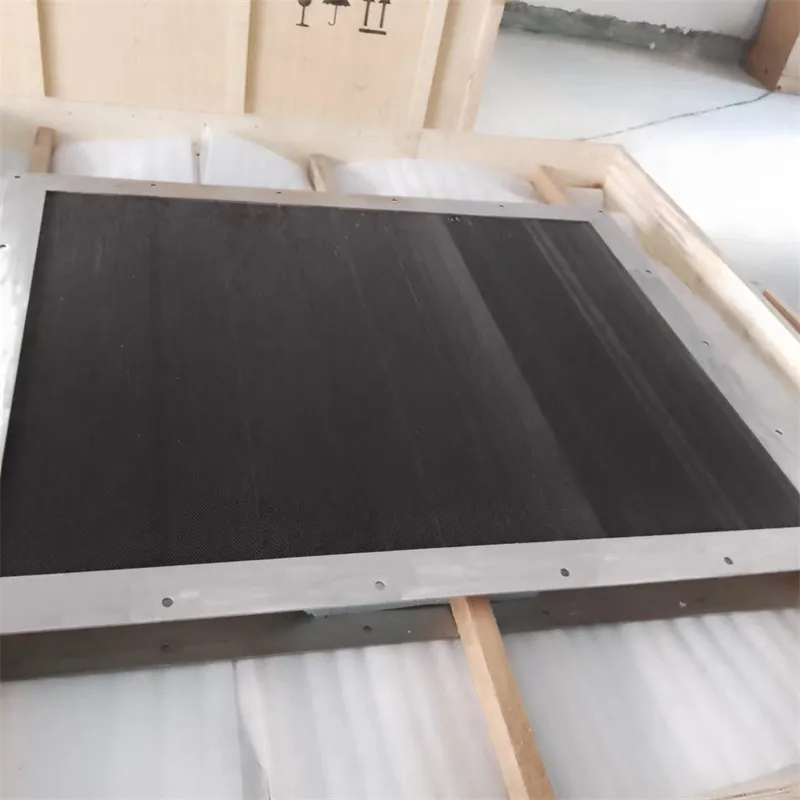
Extruded aluminum honeycomb panels stand out due to their exceptional strength-to-weight ratio, a feature achieved through their unique hexagonal structure. This cellular configuration not only minimizes the material usage without compromising strength but also enhances the load-bearing capabilities of large surface areas. For instance, in aviation, these panels contribute significantly to reducing the overall weight of aircraft, resulting in lower fuel consumption and reduced greenhouse gas emissions, aligning with global sustainability objectives.
In terms of experience, professionals utilizing extruded aluminum honeycomb appreciate its ease of fabrication and versatility. Its adaptability in various climatic conditions makes it an ideal candidate for external façade panels in buildings, where it offers longevity and minimal maintenance due to its resistance to environmental degradation like corrosion. The anodizing process further enhances its durability, extending the lifecycle of constructions in coastal or industrial environments.

From an expertise standpoint, the application of extruded aluminum honeycomb demands an understanding of material science and structural engineering. Manufacturers have perfected the art of extrusion and bonding techniques to ensure panels meet rigorous industry standards. As engineers and architects continue to push the boundaries in design, early-stage collaboration with material scientists specializing in aluminum honeycomb can lead to bespoke solutions that are both innovative and practical.
extruded aluminum honeycomb
Expertise in this field also involves knowing how to customize these panels according to specific project needs, whether that entails adjusting cell size and thickness or selecting particular alloys for improved thermal conductivity or fire resistance. These customizations are critical in sectors like automotive manufacturing, where the balance between performance and safety is paramount.
The authoritativeness of extruded aluminum honeycomb as a material is undisputed within scientific and engineering communities. Numerous studies and technical papers have highlighted its efficacy, especially in applications requiring energy absorption and impact resistance. The sandwich structure, a hallmark of this material, dissipates energy efficiently, making it a key component in protective gear and impact-resistant enclosures. Regulatory bodies and certification entities often rely on empirical data derived from testing these panels to establish industry benchmarks and safety guidelines.
Building trust with extruded aluminum honeycomb involves adhering to strict quality control protocols. Reputable manufacturers follow ISO quality management practices, ensuring consistency in panel production and performance. For end users, specifying certified products and working with established suppliers mitigates risks and guarantees that the panels will perform as expected throughout their intended lifespan.
In conclusion, the strategic integration of extruded aluminum honeycomb panels can significantly elevate projects across various industries. Their unmatched combination of strength, lightness, and adaptability not only supports ambitious design aspirations but also aligns with a broader commitment to efficiency and sustainability. Embracing this material can propel innovative solutions, establishing benchmarks for future developments in an increasingly complex and demanding world.