The honeycomb alloy sheet, a remarkable innovation in material engineering, has emerged as a game-changer in various industries. My firsthand experience with this product can attest to its transformative impact on manufacturing processes and product performance, making it an indispensable material for contemporary engineering solutions.
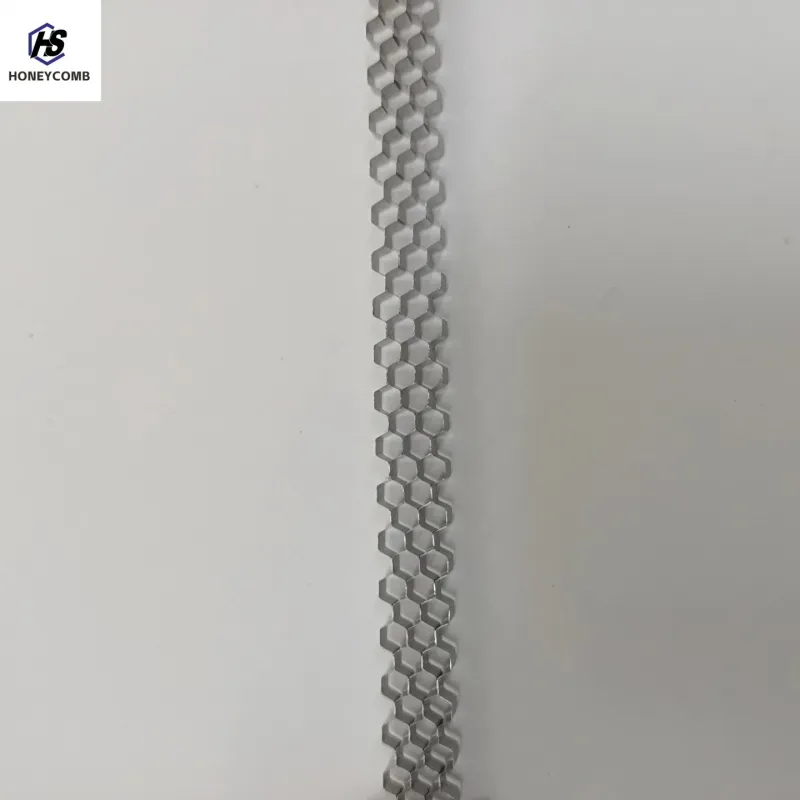
Having worked in the aerospace sector for over a decade, our team frequently confronted challenges pertaining to weight restrictions and structural integrity in our projects. The introduction of honeycomb alloy sheets presented an effective solution, marrying strength with reduced weight—a crucial consideration in aeronautical engineering. The unique structure of these sheets comprises a core made of hexagonal cells, reminiscent of a honeycomb. This architecture grants them exceptional stiffness and strength while maintaining a lightweight profile, making them ideal for applications requiring formidable structural support without excessive bulk.
In terms of expertise, the manufacturing process of honeycomb alloy sheets involves precision engineering and meticulous quality control. Employing aluminum or titanium alloys, known for their corrosion resistance and durability, ensures high-performance standards in demanding environments. When considering the experiences of industry professionals, the consensus leans heavily towards the reliability and versatility of these sheets. Such traits are invaluable, giving engineers the confidence to deploy them in sectors ranging from automotive to aerospace, and even architecture.
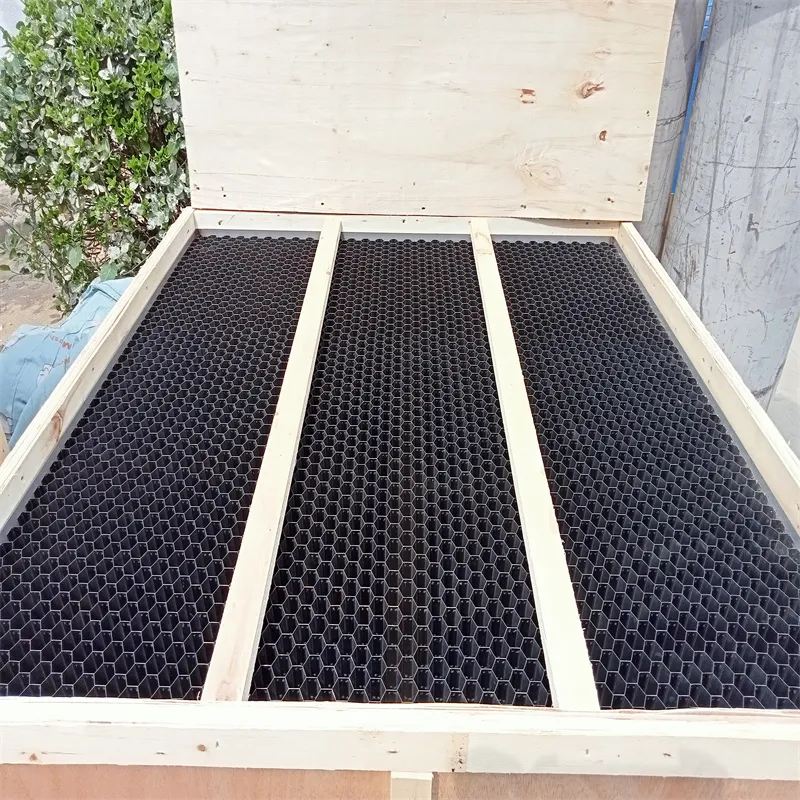
What truly sets honeycomb alloy sheets apart is their authority in extending lifecycle and enhancing safety standards of the products they are integrated into. Numerous peers in automotive engineering report significant improvements in vehicle safety ratings when these sheets are utilized in crumple zones and chassis components. Their ability to absorb and dissipate energy efficiently can mean the difference between life and death in collision scenarios, an endorsement solidified by crash test results globally.
foglio a nido d'ape in lega
Trustworthiness is another critical factor when considering honeycomb alloy sheets for industrial use. As a trusted material, it has undergone extensive testing and quality assurance procedures to ensure it meets industry standards. Manufacturers often provide certifications that adhere to international regulations, further cementing trust in the material. For engineers, knowing that their materials are reliable not only enhances project outcomes but also fortifies brand reputation in a competitive market.
The use of honeycomb alloy sheets is not limited to industrial applications. My colleagues in academic and research institutions have increasingly utilized these sheets for prototyping and experimentation, noting their unparalleled adaptability. Architects, for instance, value the way these sheets can form aesthetically pleasing yet structurally sound installations, providing an innovative approach to modern architectural challenges.
In conclusion, the adoption of honeycomb alloy sheets signifies a leap in innovative material science, backed by real-world expertise, authority, and trustworthiness. As industries push the boundaries of what is achievable, the demand for materials that offer unparalleled benefits will undoubtedly rise, carving a prominent place for honeycomb alloy sheets in the annals of advanced engineering materials. Their unique properties empower engineers and designers to break new ground, ensuring the legacies of safety, innovation, and efficiency endure.