Honeycomb seals, renowned for their sophisticated design and functional superiority, are transforming the landscape of industrial machinery. These seals, often employed in turbomachinery, serve as pivotal components that enhance efficiency and reliability by limiting leakage flow in critical applications. The enticing aspect of honeycomb seals lies in their unique structure and material composition, which not only enhances their performance but also endows them with remarkable durability.
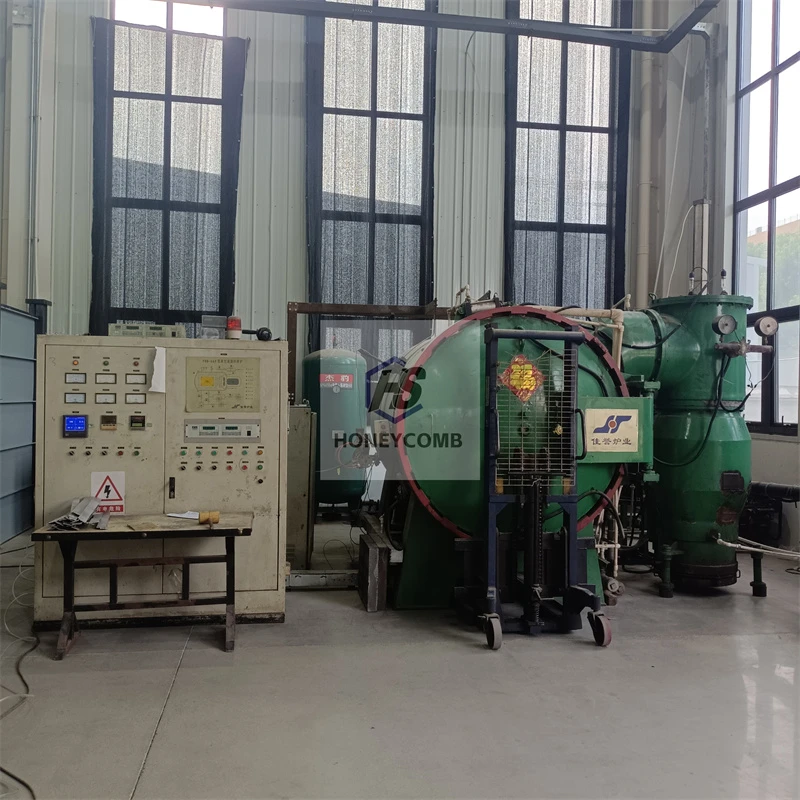
In industrial settings, efficiency is king, and honeycomb seals consistently prove to be vital tools in achieving superior performance. They exhibit a distinct ability to manage pressure differences, effectively reducing leakage in areas such as gas turbines and compressors. This attribute is primarily due to their honeycomb structure, which creates a tortuous path for any fluid attempting to escape, thereby significantly mitigating leakage compared to conventional seal designs. The structure of these seals boosts their stiffness-to-weight ratio, an essential feature for high-speed rotating equipment.
From an engineering perspective, the honeycomb seal is a masterpiece of precision and adaptability. It stands out due to its cellular design, which not only promotes thermal strain relief but also adjusts to varying thermal loads often experienced in high-speed machinery. This flexibility ensures that the integrity of the seal remains uncompromised even in the face of fluctuating operational conditions. Due to these capabilities, industries where reliability is non-negotiable, such as aerospace and power generation, heavily rely on honeycomb seals.
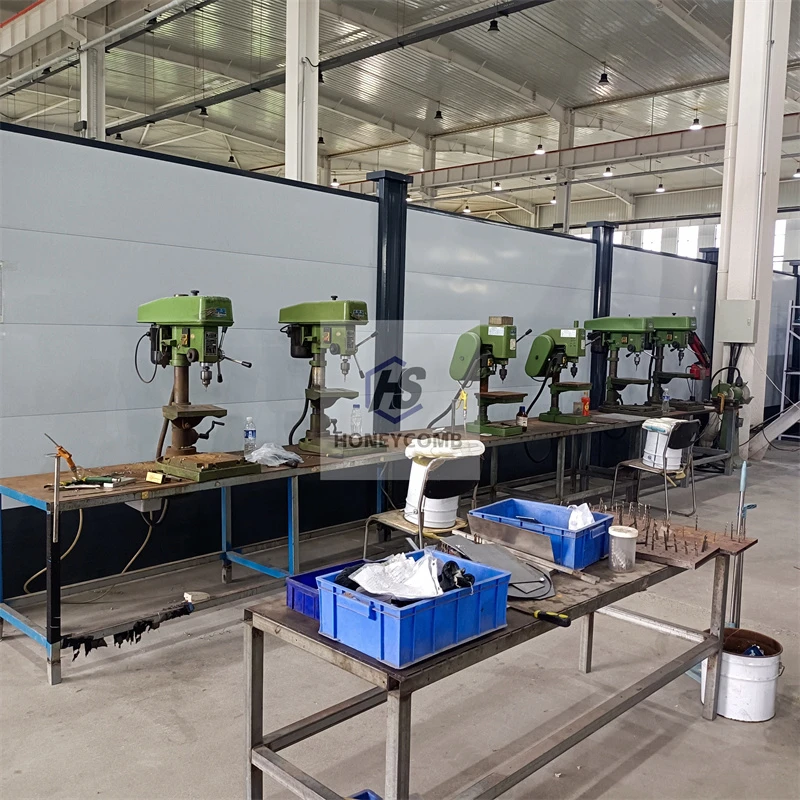
Manufacturers of honeycomb seals have taken significant strides in customizing these products to meet specific needs, further enhancing their desirability in the market. The ability to tailor the honeycomb structure, whether through variable cell sizes or materials, allows end-users to optimize their seals for particular applications. This level of customization not only enhances performance but also extends the lifespan of the machinery in which they are integrated.
honeycomb seal
Expert assessments indicate that honeycomb seals outperform many traditional sealing methods, providing a cost-effective solution to potential inefficiencies and mechanical failure. Their capability to handle high differential pressures and temperatures makes them a preferred choice for engineers aiming to extend the operational life of industrial equipment, minimize maintenance needs, and reduce downtime. This expert validation underscores the trustworthiness and authority honeycomb seals have earned over the years.
Trust in honeycomb seal products also stems from their track record in safety and reliability. In sectors where safety is paramount, any potential failure can lead to catastrophic outcomes. Honeycomb seals not only prevent such failures but do so while minimizing environmental impact by reducing leakage of potentially harmful substances. This role in promoting safe operational standards further solidifies their position as a reliable solution in advanced engineering systems.
In conclusion, honeycomb seals represent an expertly crafted balance of innovation, expertise, and practical application. Their ability to significantly enhance the efficiency of industrial machinery while ensuring safety and reliability marks them as indispensable elements in the modern engineering landscape. As industries continue to push the boundaries of what is possible, the demand for such specialized and dependable components is set to only grow.