The plastic honeycomb structure with a carbon core represents an impressive leap forward in materials engineering, bringing the benefits of lightness, strength, and versatility to a wide array of applications. This innovative product is designed with extensive research and development inputs, capitalizing on the intrinsic synergies between plastic and carbon materials.
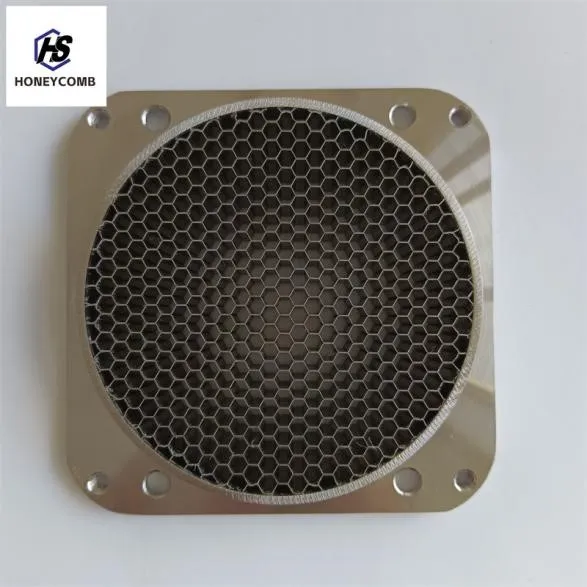
The honeycomb design is inspired by nature, specifically the strength-to-weight ratio seen in beehives. This design is known for its structural efficiency, providing an optimal distribution of weight, which translates to increased durability and a reduction in material usage. The core, made from carbon, amplifies these characteristics by imbuing the structure with increased tensile strength and thermal stability. Carbon's low density and high stiffness lend themselves particularly well to applications where weight reduction without sacrificing performance is critical.
Industries including aerospace, automotive, and construction are rapidly adopting this composite structure. In aerospace, where every gram can translate to significant energy savings, the use of a plastic honeycomb with a carbon core facilitates the production of components that are lighter, without compromising on the integrity needed to withstand extreme conditions. The automotive industry benefits similarly, as the desire for fuel efficiency leads manufacturers to seek ever-lighter components that can reduce overall vehicle weight while maintaining safety and performance standards.
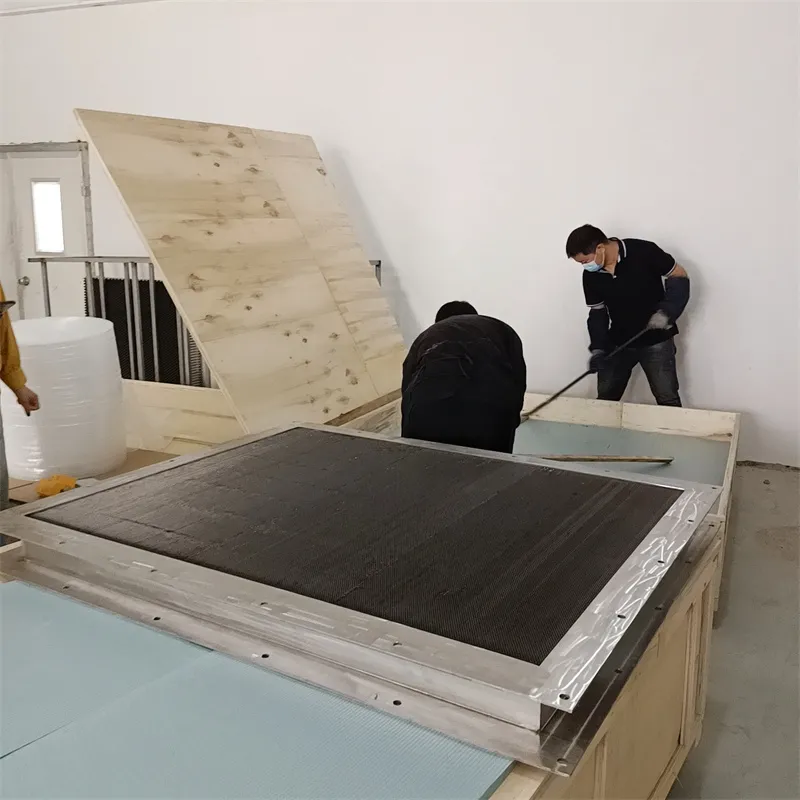
Construction is another field where these materials have a profound impact. Panels made from this honeycomb structure achieve superior thermal insulation properties while remaining highly durable under various environmental conditions.
This makes them ideal for green building practices where energy conservation is paramount. The sustainability aspect is further enhanced by the recyclability of the plastic components, ensuring that the material aligns with eco-friendly building certifications and standards.
nido d'ape in plastica con nucleo in carbonio
The expertise behind these products involves a deep understanding of the physical and chemical interactions between plastic and carbon fibers. Manufacturing such materials requires controlled processes that ensure the carbon core is optimally integrated within the plastic honeycomb, maintaining structural integrity while allowing flexibility for tailored applications. Industry experts point out that the potential for customization is significant, as the production process can adapt the thickness, cell size, and material compositions to meet specific needs.
From a trustworthiness perspective, these products undergo rigorous testing to ensure compliance with international standards for safety and performance. Certifications from recognized authorities provide assurance to consumers and industry users that the products will perform as expected in real-world conditions.
Manufacturers of these honeycomb structures are continually advancing their techniques by investing in cutting-edge technology and research to refine and expand the application possibilities. They are also committed to sustainable practices by minimizing waste in production and endorsing the life cycle analysis of their products to reduce environmental impact.
In summary, plastic honeycomb structures with carbon cores are revolutionizing the way industries approach material usage, embodying the principles of efficient design, sustainability, and versatility. As sectors striving for future innovation embrace these materials, the profound benefits will undoubtedly continue to unfold, establishing this technology as a cornerstone of modern engineering solutions.