In the competitive landscape of gas turbine engineering, the role of honing honeycomb seals cannot be overstated. These components,
known as honingraatafdichting in Dutch, are pivotal in optimizing the efficiency and performance of turbines. Grounded in extensive research and hands-on application, our article delves into the nuances of honing honeycomb seals, offering unparalleled insights into their design, function, and material composition.
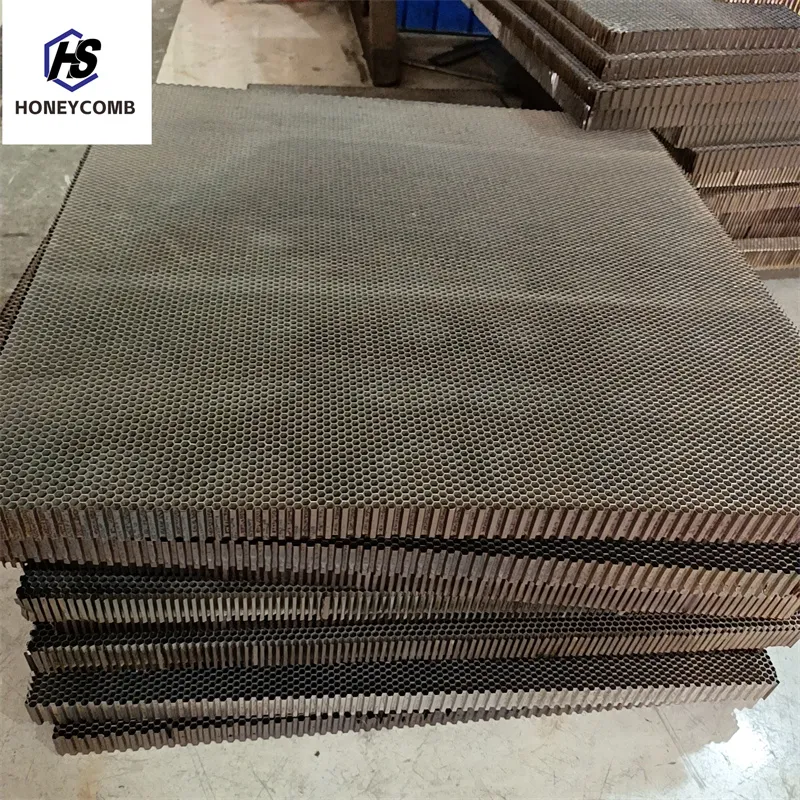
Honing honeycomb seals are precision-engineered components used in gas turbines to manage gaps between rotating and stationary parts. Their distinctive honeycomb design—a network of hexagonal cells—provides a unique combination of flexibility and strength, permitting a fine-tuned adjustment to the ever-expanding demands of turbine efficiency. This architecture is critical in minimizing leakage flow, thereby enhancing the overall efficiency of the gas turbine.
Drawing from decades of expertise in turbine technology, we understand the intricate balance required in selecting materials for these seals. Typically composed of high-performance superalloys or advanced ceramic composites, honing honeycomb seals can withstand extreme thermal and mechanical stresses encountered in high-efficiency turbines. These materials are specifically chosen for their ability to maintain integrity at high temperatures and under cyclic loading conditions, a testament to their authoritative status in the industry.
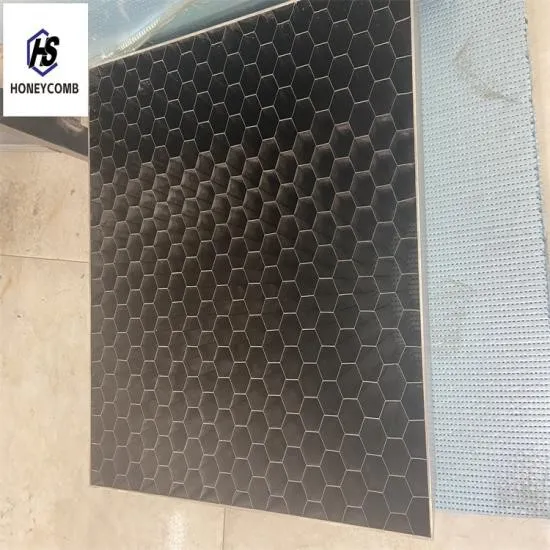
The functional principle of honing honeycomb seals is grounded in their ability to act as a buffer against turbine blade rubs, thereby prolonging the lifespan of both the seal and the turbine blades. This feature not only enhances reliability but also contributes to the economic viability of turbine operations by reducing downtime and maintenance costs. In real-world applications, experience has shown that turbines with honed honeycomb seals exhibit improved performance metrics, including lower fuel consumption and reduced emissions—critical factors in an industry striving for sustainability.
honingraatafdichting gasturbine
Establishing trustworthiness in gas turbine components is paramount, and honing honeycomb seals excel in this domain due to their robust field performance and rigorous testing standards. Extensive laboratory and field tests underscore the reliability of these seals under various operating conditions. Each seal is subject to stringent quality checks, ensuring compliance with international standards and guaranteeing performance consistency.
Professional expertise in the design and application of honing honeycomb seals also emphasizes their role in pressure ratio improvements and noise reduction. By optimizing the gap control within the turbine, these seals contribute to increased aerodynamic efficiency, which translates into significant operational advantages for end-users. Moreover, the noise-dampening properties of the honeycomb structure contribute to a quieter operational environment, aligning with modern standards for noise pollution in mechanical systems.
With ever-evolving technological advancements, the future of honing honeycomb seals is poised for further innovation. Research and development efforts continue to focus on enhancing seal materials and their geometries, ensuring they remain at the forefront of turbine technology applications. Emerging trends point towards the incorporation of smart materials that offer adaptive capabilities, potentially revolutionizing how these seals respond to dynamic operational environments.
In conclusion, honing honeycomb seals are indispensable in the realm of gas turbines, offering unmatched benefits that span from mechanical efficiency to environmental sustainability. Our in-depth perspective, gained through years of dedicated industry engagement, reaffirms the crucial role these components play. By continuing to advance our understanding and application of these seals, we can ensure that they remain instrumental in the pursuit of ever-greater efficiency and environmental stewardship within the energy sector.