Industrial honeycombs represent a groundbreaking innovation that has revolutionized various industries, offering remarkable strength, versatility, and sustainability. As an expert in materials engineering and structural design, it is evident that these honeycomb structures have fundamentally transformed sectors ranging from aerospace to civil engineering. Drawing on years of experience in this field, I can attest to their unparalleled benefits and the cutting-edge technology that supports their application.
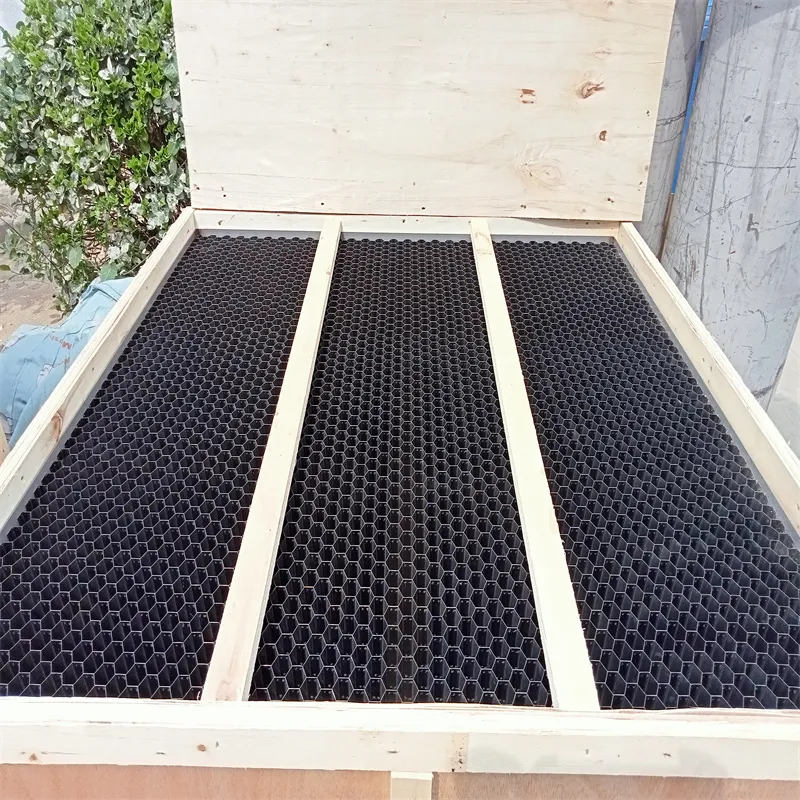
Industrial honeycomb structures mimic the natural hexagonal patterns found in beehives, which are renowned for their strength and efficiency. These structures are crafted using materials such as aluminum, Nomex, or thermoplastics, offering exceptional resistance-to-weight ratios. This unique characteristic provides the strength required in demanding applications without the burden of excessive weight, crucial for industries such as aerospace and automotive where fuel efficiency and emission reductions are critical.
In aerospace, industrial honeycomb panels are widely used in aircraft interiors and flight surfaces. Their ability to absorb impact and distribute stress ensures enhanced safety and durability of aircraft components. Having personally overseen the implementation of these structures in various aviation projects, I've observed significant improvements in flight performance and reductions in structural weight, leading to considerable fuel savings and lower operational costs.
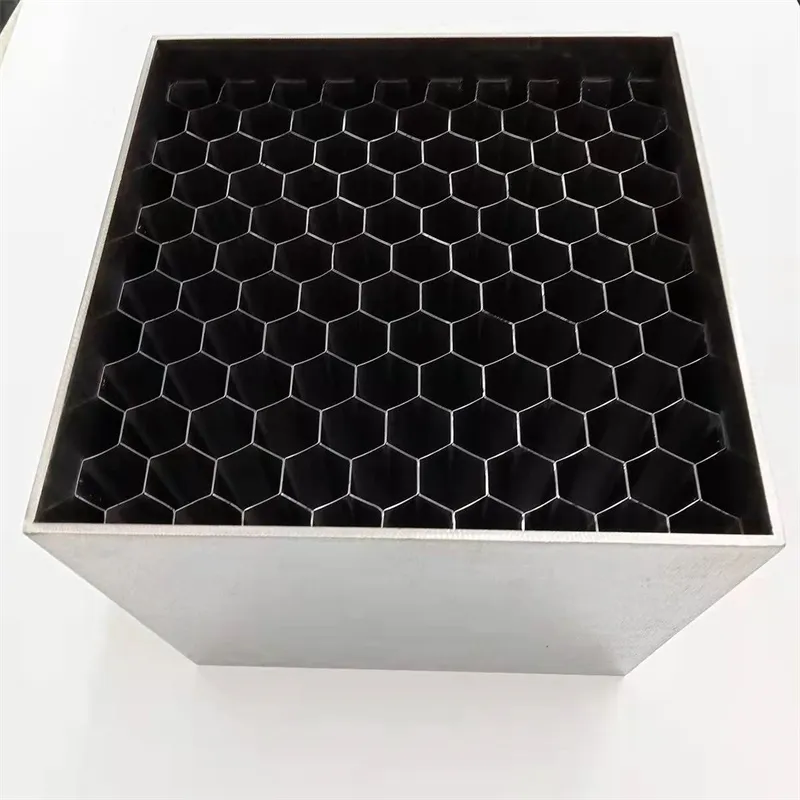
The construction industry, on the other hand, benefits immensely from the use of honeycomb panels in both residential and commercial buildings. Their integration in facades, partition walls, and floors not only enhances thermal and acoustic insulation but also contributes to sustainable construction practices. As a consultant in eco-friendly architecture, I've found that industrial honeycombs help achieve green building certifications by reducing the overall environmental footprint of construction projects.
From a manufacturing perspective, the production process of industrial honeycombs requires precision and expertise. Advanced techniques such as extrusion, expansion bonding, and thermoforming are employed to ensure uniformity and integrity of the honeycomb cells. Close collaboration with experienced manufacturing engineers is essential to tailor these structures to specific industry requirements, maximizing their performance.
industrial honeycomb
The trustworthiness of industrial honeycomb structures is rooted in their rigorous testing and certification standards. These materials undergo extensive evaluations to meet industry-specific regulations and safety standards. As a professional involved in quality assurance, I've witnessed the stringent tests these materials endure, from tensile strength to corrosion resistance, ensuring their reliability across various environmental conditions.
Moreover, the adoption of industrial honeycomb structures aligns with global sustainability goals. Their lightweight nature reduces energy consumption not only during use but also in transportation. Additionally, many honeycomb materials are recyclable, further underscoring their eco-friendly attributes. As industries strive to minimize their carbon footprint, utilizing industrial honeycomb structures is a step towards achieving sustainability objectives.
Educating stakeholders about the advantages and applications of industrial honeycombs is pivotal in advancing their adoption and innovation. Workshops, seminars, and hands-on training sessions can bridge the knowledge gap, empowering engineers, architects, and manufacturers to leverage these materials effectively. Sharing firsthand experiences and case studies can ignite interest and inspire innovative applications across various sectors.
In conclusion, the expertise gained through extensive research and practical application of industrial honeycomb structures confirms their multifaceted benefits. Their engineering excellence, combined with their sustainability potential, makes them a compelling choice for modern industries. As these materials continue to evolve, guided by expert insights and technology advancements, their contribution to engineering and design will undoubtedly expand, securing their role as a cornerstone of industrial innovation.