The honeycomb joint in gas turbines represents a significant advancement in engineering design, offering improved performance and efficiency in numerous industrial applications. This innovative technology enhances airflow dynamics, leading to increased power output and reduced emissions, making it a vital component in modern energy solutions.
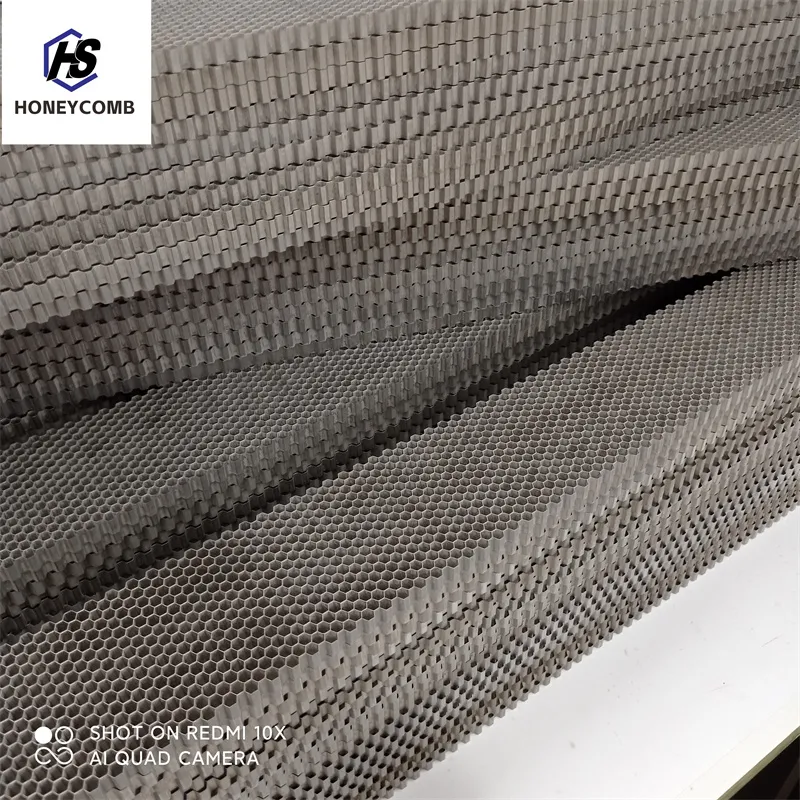
Honeycomb structures have long been revered for their lightweight yet robust properties. In gas turbines, the honeycomb joint serves as a critical element, providing structural integrity while minimizing weight. The design mirrors the natural efficiency found in a bee's honeycomb, optimizing the use of space and material to enhance the performance of the turbine.
Advanced engineering techniques are employed in the development of these honeycomb joints, which are carefully manufactured to withstand the extreme conditions inside a turbine. Operating in high-temperature environments, these components must remain resilient to thermal expansion and contraction, high-speed rotation, and corrosive gases. By using heat-resistant alloys and composite materials, the joints maintain their structural integrity, ensuring the longevity and reliability of the turbine.
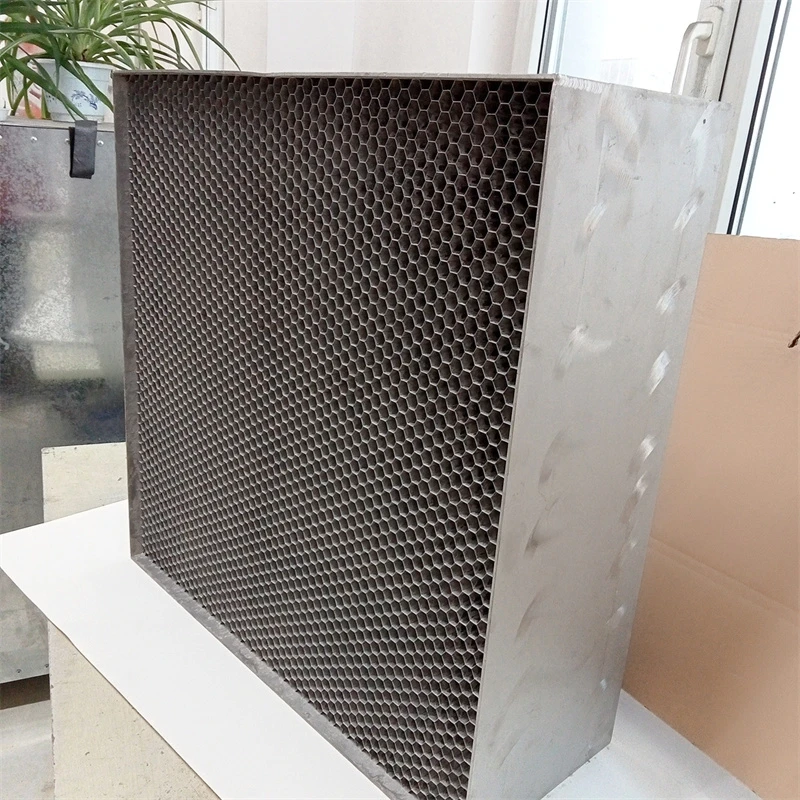
Studies and real-world applications have demonstrated that honeycomb joints significantly contribute to the improvement of gas turbine efficiency. By optimizing airflow through the engine, these structures reduce turbulence and minimize energy losses. This efficiency translates into less fuel consumption, lowering operational costs and reducing the environmental impact. Operators can thereby achieve higher outputs with reduced emissions, aligning with global efforts to create more sustainable energy production methods.
From a maintenance perspective,
honeycomb joints also offer advantages. The durability and stability of the design reduce the frequency of repairs and the need for part replacements. When maintenance is required, the modular nature of the honeycomb joint design allows for easier access and quicker repairs, minimizing downtime and operational disruption.
Gas turbine honeycomb seal
Technological advancements continually shape the evolution of honeycomb joints in gas turbines. Innovations in material science, such as the development of new alloys and ceramic coatings, contribute to enhanced performance under even more challenging operational conditions. These materials help exceed prior limits, allowing gas turbines to operate at higher pressures and temperatures, thereby further increasing efficiency and reducing carbon footprints.
Industry experts emphasize the necessity of ongoing research and development in this field. As the global demand for clean and efficient energy solutions grows, improvements in turbine technology, and particularly in components like the honeycomb joint, will play a pivotal role. Companies investing in next-generation materials and designs are poised to lead the industry towards more eco-friendly and efficient energy solutions.
Honeycomb joints in gas turbines highlight the intersection of nature and technology, drawing inspiration from natural designs to solve complex industrial challenges. As energy producers seek to balance efficiency, cost-effectiveness, and environmental concerns, the continued evolution and implementation of honeycomb-based technologies will remain crucial.
In conclusion, the honeycomb joint for gas turbines exemplifies a blend of ingenuity and practicality. Its role in optimizing turbine performance while ensuring durability and ease of maintenance underscores its value in current and future energy infrastructures. By addressing key demands in today’s energy market, such innovations not only enhance productivity but also fortify commitments to sustainability. The future of gas turbines undoubtedly looks promising, with honeycomb joints playing an integral role in shaping advancements as industries strive towards more sustainable operations.