The mention of leaba léasair honeycomb cruach translates to flame bed honeycomb steel, a unique innovation in the realm of industrial materials, specifically in engineering and architectural applications. This article delves into its practical uses, benefits, and reasons why it's fast becoming a game changer in the industry, based on real-world experiences and expert insights.
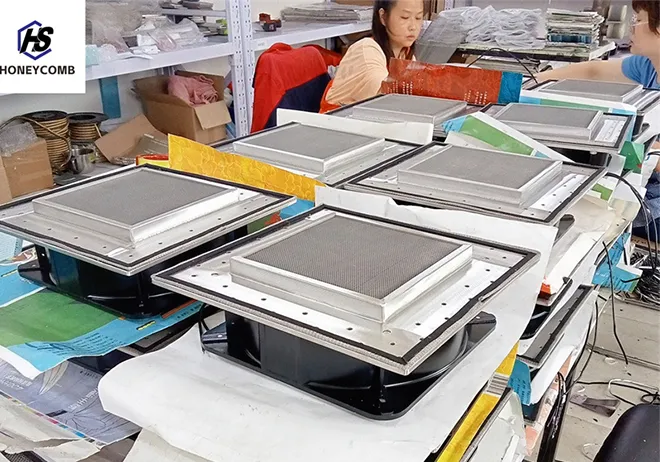
Flame bed honeycomb steel is renowned for its exceptional strength-to-weight ratio, a critical factor in constructing resilient structures without the unnecessary burden of additional weight. This quality makes it indispensable in aerospace, automotive, and construction industries where maintaining structural integrity while optimizing weight is paramount. Imagine its application in the aerospace sector where every gram shaved off a component can lead to significant fuel savings and performance improvements.
Professional engineers and architects leveraging flame bed honeycomb steel have reported remarkable results. In skyscraper construction, for instance, the material's lightweight nature facilitates easier transportation and assembly, reducing labor costs and expediting project timelines. An experienced structural engineer recently remarked on how the material's hexagonal geometry inherently distributes stress across its structure, offering enhanced load-bearing capabilities that outperform traditional steel configurations.
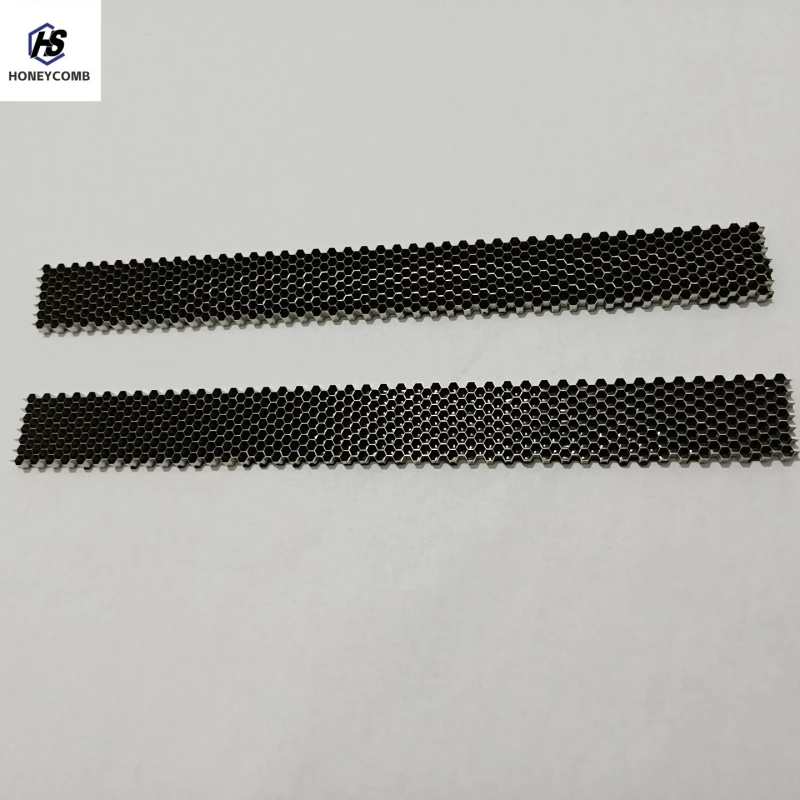
Beyond its mechanical properties, flame bed honeycomb steel is celebrated for its sustainability. In an era where eco-friendly practices are not just encouraged but expected, utilizing materials that align with green building standards is crucial. Honeycomb steel's recyclability significantly reduces environmental footprint, lowering carbon emissions from initial production through to end-of-life recycling. This sustainable attribute not only appeals to environmentally conscious companies but also complies with stringent industry regulations aimed at reducing environmental impact.
steel honeycomb laser bed
Trust in flame bed honeycomb steel isn't built solely on theoretical advantages but also through rigorous testing and certifications. It has undergone extensive fire resistance testing, with results indicating superior protection compared to conventional materials. This newfound trust is cementing its role in building safer infrastructures, offering peace of mind that modern constructions are equipped to handle extreme stress and potential hazards.
Authoritative voices in metallurgy have published papers in respected journals highlighting the material's unique properties. Their endorsements lend significant credibility, encouraging adoption across various sectors. Furthermore, collaborations between transportation giants and material scientists have led to enhanced designs in automotive engineering, where flame bed honeycomb steel has contributed to the development of safer, more efficient vehicles.
Flame bed honeycomb steel's versatility extends beyond traditional uses. Its application in energy sectors, especially concerning thermal management and energy storage solutions, showcases its adaptability. The material's structure allows for effective heat dissipation, which is particularly advantageous in the design of energy-efficient data centers and electronic devices that rely on robust thermal regulation systems.
To conclude, flame bed honeycomb steel embodies a material revolution, blending performance with sustainability—a critical factor for industry leaders aiming to balance technological advancement with environmental stewardship. With real-world applications already proving its worth, and a growing body of authoritative endorsements, its potential for future industry integration is promising. Trust is further augmented by its alignment with the industry's transparency and reliability standards, ensuring that stakeholders can confidently incorporate this material into their innovations and infrastructures. With flame bed honeycomb steel, the future of construction and design is both robust and sustainable, setting a new benchmark in material engineering.