Metal honeycomb structures have revolutionized the engineering and architectural landscapes with their impressive combination of strength, lightweight characteristics, and versatility. These innovative structures,
inspired by natural honeycombs, offer an unparalleled balance of performance and design flexibility. With applications ranging from aerospace to automotive industries, metal honeycombs are reshaping the standards of modern construction and manufacturing.
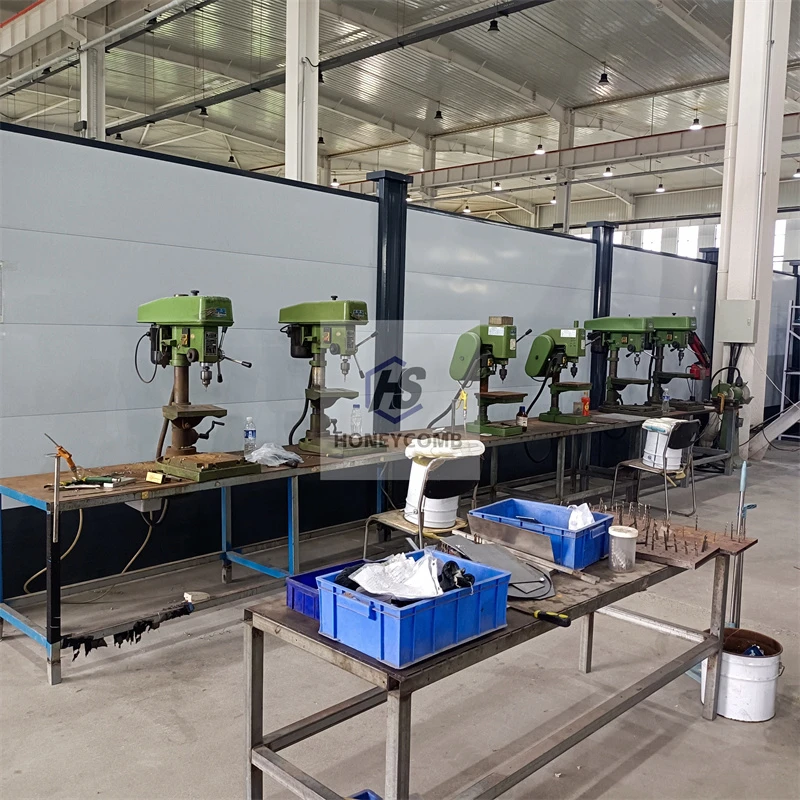
True experience in working with metal honeycombs reveals their unique ability to reduce material usage while maintaining structural integrity. Engineers and architects who integrate these structures into their projects often report significant improvements in weight reduction, leading to enhanced fuel efficiency in vehicles and lower material costs in construction. Metal honeycombs are often made from aluminum, steel, or titanium, each metal contributing distinct advantages such as corrosion resistance, tensile strength, and thermal conductivity.
The expertise involved in manufacturing metal honeycombs requires precision engineering and cutting-edge technology. Producing these structures involves meticulous processes like sheet metal forming, adhesive bonding, and in some cases, welding. The uniform hexagonal or rectangular cells are created using expansion and corrugation techniques, establishing the characteristic matrix that provides superior load-bearing capabilities and energy absorption. Professionals in the field must understand material science and mechanical engineering deeply to optimize these processes for specific applications.
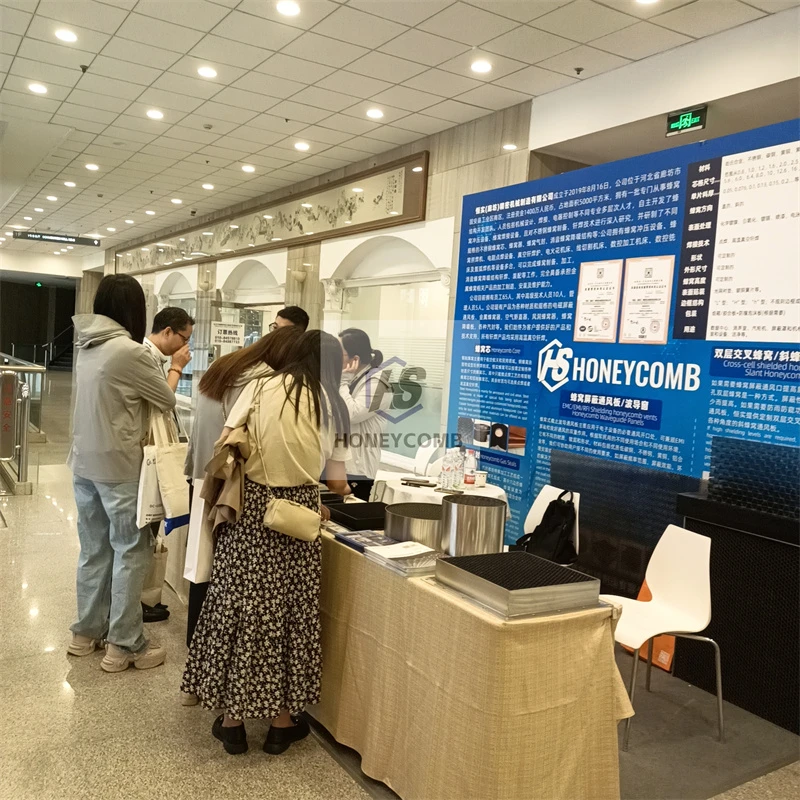
metal honeycomb
Authoritativeness in this domain is marked by industry standards and certifications. For instance, products that meet the specifications of the International Organization for Standardization (ISO) or the Aerospace Material Specifications (AMS) ensure reliability and high performance in demanding applications. Companies that manufacture metal honeycombs adhere to these strict standards to maintain their credibility and market competitiveness. Additionally, ongoing research in nanotechnology and material innovations continues to advance the capabilities of metal honeycombs, making them a topic of interest at leading engineering conferences and in academic journals.
Trustworthiness is critical for products like metal honeycomb structures that are used in safety-critical applications. Manufacturers must provide transparent information about their production processes, materials used, and the results of rigorous testing procedures. Trust can further be built by showcasing a track record of successful projects and satisfied clients, ranging from major aerospace firms to innovative architectural firms. This ensures that when stakeholders choose metal honeycombs, they can have confidence in the material's performance and reliability.
Ultimately, metal honeycomb structures represent a future-forward solution for industries seeking efficiency, sustainability, and innovation. By leveraging their strength, professionals across various sectors are crafting solutions that are not only groundbreaking but also safe and dependable. The path forward for metal honeycombs lies in continuous innovation, with potential applications only limited by the imagination and technical expertise of their users. This makes metal honeycomb not just a product, but a pivotal element in the evolution of industrial and structural design.