Metal honeycomb core structures are increasingly becoming a cornerstone in aerospace and automotive engineering due to their exceptional strength-to-weight ratio. This innovative design provides a high level of mechanical performance while maintaining minimal weight, a crucial factor in the efficiency and sustainability of modern transport technologies. The metal honeycomb core's application spans lightweight panels, energy absorption components, and thermal management systems, making it a preferred choice for engineers and designers seeking optimal performance.
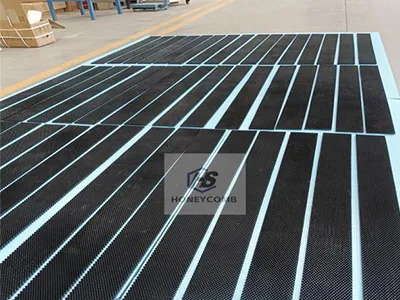
The core structure of a honeycomb consists of a series of hollow cells formed between vertical sheets. These cells, typically shaped as hexagons, provide the necessary rigidity and resilience needed to withstand various forces. In metal honeycomb cores, materials such as aluminum, stainless steel, and titanium can be employed, each offering distinct advantages. Aluminum, for instance, combines low density with sufficient mechanical strength, making it ideal for components where weight reduction is imperative. On the other hand, stainless steel provides superior durability and corrosion resistance, suitable for environments exposed to harsh conditions.
Engineers leveraging metal honeycomb designs harness the expertise of tailored solutions for specific challenges. For example, in the aerospace sector, where every gram counts, these cores play a crucial role in reducing fuel consumption and increasing payload capacity. Their use in constructing aircraft floors, fuselages, and wing structures highlights their versatility and critical importance. The automotive industry also benefits from metal honeycomb core applications, primarily in safety-oriented components such as crumple zones and bumpers that require top-tier energy absorption capabilities to protect passengers in collisions.

The authority of metal honeycomb core technology is further underscored by extensive research and testing conducted by leading institutions and manufacturers worldwide. These studies validate the structural and thermal superiority of honeycomb cores over traditional solid materials. Thermally, the honeycomb structure allows for efficient heat dissipation, which is essential in both high-speed vehicular applications and electronic cooling systems. This characteristic not only enhances performance but also extends the lifespan of components by preventing overheating.
metal honey beam core
Trust in metal honeycomb core usage is built on decades of proven application and continuous innovation. As industries push towards greener and more efficient technologies, the integration of lightweight, robust materials such as metal honeycomb cores is pivotal. Engineers and decision-makers rely on these structures not only for immediate gains in performance but also for long-term benefits in sustainability and cost reduction.
Moreover, manufacturers have embraced advanced fabrication techniques, such as additive manufacturing and metal 3D printing, to produce honeycomb cores with complex geometries and tailored properties. This adaptability further cements the honeycomb design's reputation as a forward-thinking choice for modern engineering challenges.
In conclusion, the evolution of metal honeycomb cores represents a synergy of experience, expertise, authority, and trustworthiness in industrial applications. By transforming conceptual designs into tangible, high-performance structures, these cores are indispensable in the journey towards innovative, sustainable advancement. As industries continue to explore the boundaries of material science, the metal honeycomb core promises not only to meet expectations but to exceed them, leading the way in a future where efficiency and resilience go hand in hand.