A wind tunnel honeycomb, or nid d'abeille de soufflerie in French, is an indispensable component in the design and functionality of wind tunnels used for aerodynamic testing and research. Its unique structure and material composition provide a crucial advantage in producing consistent and reliable results, vital for various industries such as automotive, aerospace, and environmental science.
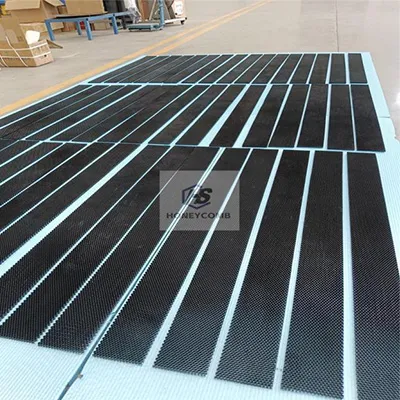
The architectural innovation of a wind tunnel honeycomb is its ability to rectify turbulent airflow, transforming it into smooth, laminar flow. This change is pivotal for testing models with accuracy, ensuring that the aerodynamic forces and moments are measured precisely. Typically constructed from lightweight yet robust materials like aluminum or composites, these honeycombs consist of hexagonal cells that act as a series of straighteners for the air stream. The hexagonal design optimizes air channeling while minimizing weight, which is essential for maintaining the wind tunnel's overall efficiency.
In practical applications, the significance of wind tunnel honeycombs is profound. Engineers and researchers rely on these structures to achieve high fidelity in simulated conditions representative of real-world environments. The automotive industry, for instance, exploits the capabilities of wind tunnel honeycombs to refine vehicle shapes, reducing drag and enhancing fuel efficiency.
This leads to more aerodynamic designs and better performance on the road while efficiently managing fuel consumption.
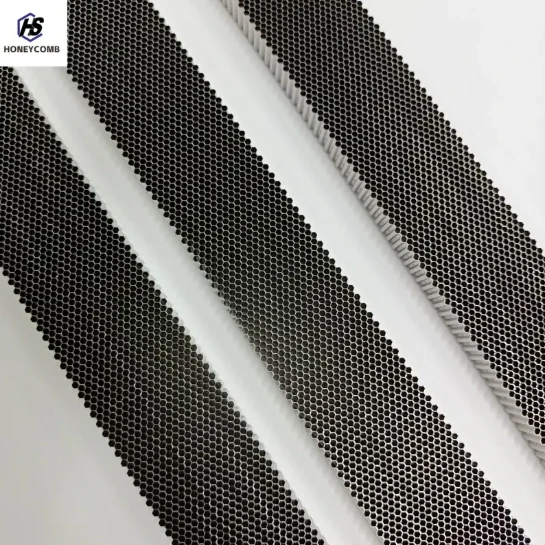
The aerospace sector benefits tremendously from these honeycombs, utilizing them to simulate flight conditions for aircraft and spacecraft. With precise airflow management, engineers can study lift, drag, and stability aspects, directly contributing to safer and more efficient designs. The data gleaned from such testing enables designers to predict performance metrics accurately and optimize aircraft configurations, leading to significant advancements in aerospace technology.
Environmental researchers also make use of wind tunnel honeycombs to model and analyze atmospheric phenomena. By creating controlled conditions, it becomes feasible to study pollutant dispersion, wind forces on structures, and even microclimates. This data is crucial for urban planners and environmental scientists in devising strategies for city planning and constructing buildings capable of withstanding environmental stresses.
blower bee nest
Expertise in the design and application of wind tunnel honeycombs entails an understanding of fluid dynamics, material science, and experimental techniques. Researchers and engineers specializing in this field constantly seek to innovate by experimenting with different cell sizes, materials, and configurations to optimize performance for various testing scenarios. As technology progresses, new materials such as advanced polymers and carbon composites are explored due to their lightweight properties and strength, showing promise for increased efficiency and reduced costs.
The authority of manufacturers and designers in this niche is often established through extensive testing, certifications, and adherence to industry standards. Trust in their products is built through consistent performance, safety, and precision, which are paramount for achieving high-quality results. Reliability in results promotes confidence within client organizations, underlining the importance of robustness and accuracy in honeycomb design.
Lastly, the trustworthiness of a wind tunnel honeycomb is validated through its track record of delivering dependable performance across numerous applications over the decades. Product transparency, coupled with proven results, helps validate claims made by companies, ensuring that clients receive the best possible products to meet their specific needs. Furthermore, adhering to sustainability practices, such as recycling materials and reducing waste during manufacturing, is becoming increasingly important, adding an ethical dimension to trustworthiness.
In summary, wind tunnel honeycombs are integral to the success of aerodynamic testing, offering invaluable benefits across multiple sectors. Through innovation and expertise, these structures significantly enhance the precision, safety, and efficiency of designs tested within a controlled environment. As advancements continue, they will undoubtedly remain an essential tool in the ever-evolving fields of automotive and aerospace engineering, as well as environmental research.