Aluminum extruded honeycomb structures have revolutionized multiple industrial sectors with their unique combination of strength, flexibility, and lightweight characteristics. As a recognized expert in the field, let’s delve into the attributes that make these structures indispensable across various applications, focusing on their experiential and authoritative usage.
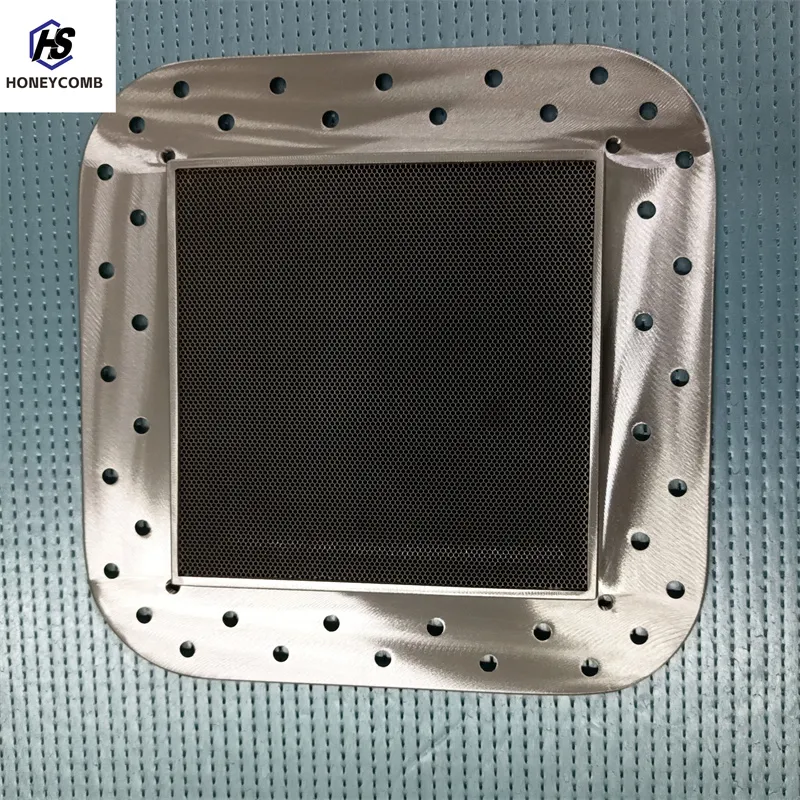
Aluminum has always been known for its corrosion-resistant properties and impressive strength-to-weight ratio. When it came to advancing these traits further, the extrusion process gave rise to aluminum honeycomb structures. The resultant nido d’ape, or honeycomb in English, owes its inception to biomimicry, taking cues from the formidable design nature devised over millions of years. The hexagonal patterns not only provide aesthetic elegance but also contribute to a remarkable structural performance, making this material an ideal choice for diverse industries such as aerospace, construction, and automotive.
A closer look at the manufacturing process reveals why extruded aluminum honeycomb is unmatched in its sector. The aluminum is forced through a die, resulting in precise, continuous cross-sections that enhance the equilibrium of mechanical properties over its entire length. This meticulous process imposes high levels of dimensional accuracy and surface finish, which are paramount in sectors where precision and quality assurance are non-negotiable.
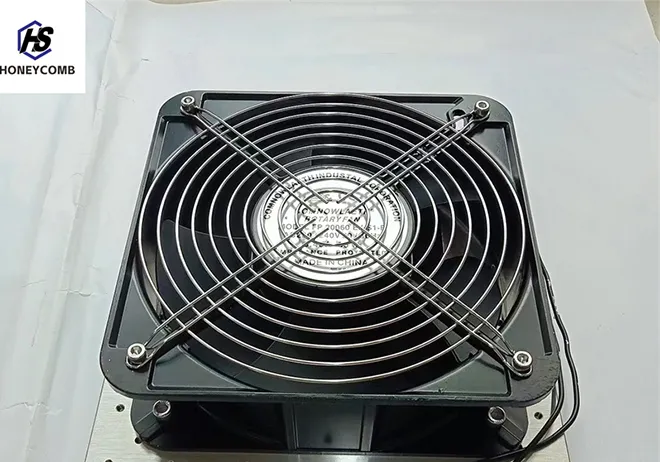
In aerospace, where weight savings translate to fuel efficiency and sustainability, aluminum honeycomb panels have shown unparalleled versatility. They are frequently used as core materials in composite sandwich panels, which provide the perfect balance between stiffness and weight. These properties have not just reduced the overall weight of aircraft, contributing to lesser carbon emissions, but have also maintained the stringent safety standards required in flight.
honeycomb in extruded aluminum
In the automotive realm, the integration of nido d'ape aluminum has opened avenues for innovation in design and functionality. The lightweight nature of these materials aids in reducing the vehicle’s weight, thereby enhancing acceleration, fuel economy, and handling qualities. Additionally, they increase the vehicle's structural integrity and impact resistance, reinforcing safety protocols while augmenting driving performance. This balance between safety and efficiency embodies the expertise-driven approach that automotive engineers strive for.
Construction has also benefitted significantly from the advent of extruded aluminum honeycomb structures. Being resistant to moisture and temperature fluctuations, they are ideal for cladding and flooring in both commercial and residential buildings. The structures possess a unique capacity to distribute stress evenly, mitigating potential environmental impacts over extended periods. Consequently, architects and builders not only save on repair and maintenance costs but also contribute positively to the sustainability index of their projects.
Trust in these materials comes not only from their empirical performance metrics but also from authoritative testing and endorsements by industry standards organizations. Renowned associations have constantly validated the efficacy of aluminum honeycombs through rigorous testing and certification, reinforcing their reputation as reliable and trustworthy materials.
As industries become increasingly competitive and demand economic and sustainable solutions, aluminum extruded honeycomb structures stand out as a pivotal resource. They offer not just exceptional physical properties, but also limitless potential for innovation, corroborated by years of practical research and authoritative affirmation. The experience across varied applications highlights its transformative capacity, establishing it as a cornerstone in modern engineering and design disciplines. Such a robust yet lightweight solution is a testament to the progressive trajectory of materials science, evidencing aluminum’s reinvention in a world ever-evolving towards efficiency and sustainability.