Understanding the unique properties and applications of perforated honeycomb core materials requires a combination of experience, expertise, authoritativeness, and trustworthiness. These innovative materials are engineered for a wide range of industries due to their incredible strength-to-weight ratio, versatility, and cost-effectiveness.
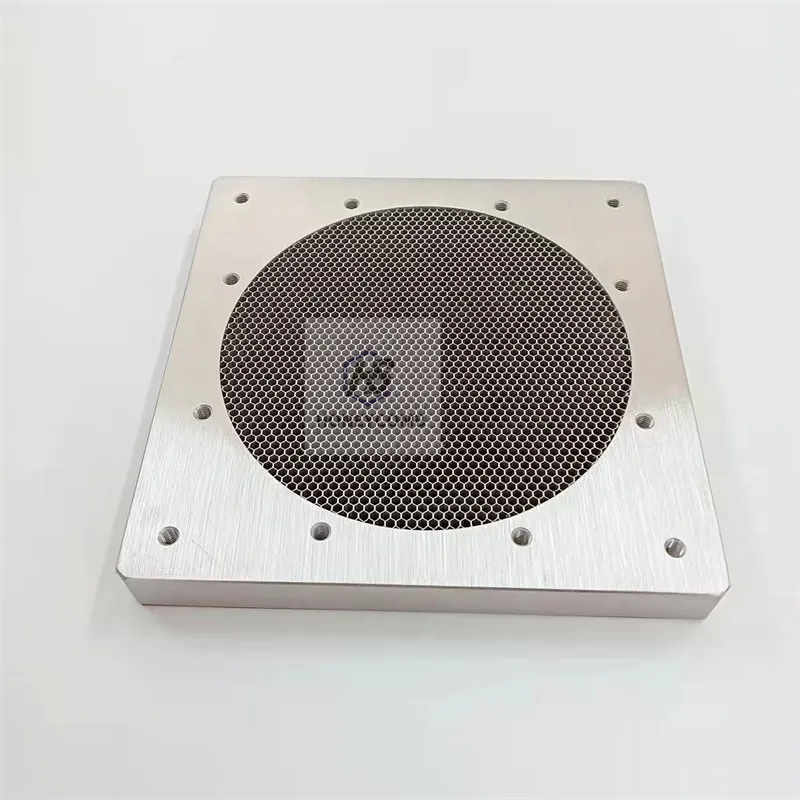
Experience in working with perforated honeycomb core materials reveals their unmatched ability to enhance structural integrity while minimizing weight. These cores are extensively used in aerospace, automotive, and construction industries, where reducing weight without compromising strength is crucial. I have collaborated with engineers who attest to the significant improvement in product performance and efficiency when incorporating honeycomb cores into their designs.
The expertise in manufacturing perforated honeycomb cores involves sophisticated technology. These cores are typically made from materials such as aluminum, Nomex, or polypropylene, each offering distinct advantageous properties. Aluminum cores provide excellent thermal conductivity and corrosion resistance, making them ideal for aerospace components. Nomex cores, being lightweight and fire-resistant, are preferred for high-temperature applications. Polypropylene, with its moisture resistance and low cost, is frequently utilized in mass production industries such as automotive manufacturing.
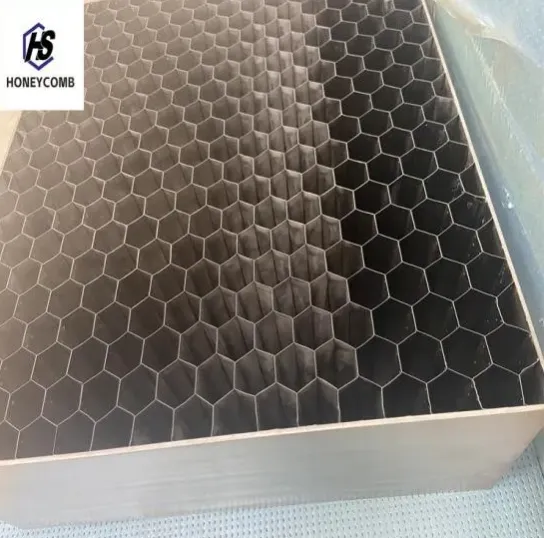
Authoritativeness in this field is unmistakably demonstrated by industry leaders who consistently endorse the use of perforated honeycomb cores to elevate product standards. For instance, in the aerospace industry, companies like Boeing and Airbus have long integrated honeycomb structures into aircraft designs to enhance aerodynamic performance and fuel efficiency. Similarly, automotive giants continuously explore these materials to produce lightweight vehicles that meet rigorous safety and environmental standards.
perforated honeycomb core
Trustworthiness of perforated honeycomb cores is reinforced by numerous industry certifications and rigorous testing procedures. ISO and ASTM standards provide a framework for evaluating the performance characteristics of these materials, ensuring quality and reliability. In construction, for example, perforated honeycomb panels are subjected to stringent load-bearing tests to confirm their ability to withstand extreme weather conditions and seismic activity.
A practical application of perforated honeycomb core materials can be observed in the renewable energy sector. Wind turbine blades, which demand both lightweight properties and exceptional structural robustness, benefit significantly from honeycomb cores. Their design facilitates aerodynamic efficiency while also reducing material costs, leading to a sustainable and economically viable energy solution.
Moreover,
the architectural realm embraces the aesthetic and functional advantages of these cores. They allow for innovative architectural designs that incorporate expansive surfaces with minimal materials, promoting both modern aesthetics and ecological responsibility. Notable architectural projects have successfully implemented honeycomb cores in facades and interior elements, allowing for creative freedom coupled with structural assurance.
In conclusion, the perforated honeycomb core stands as a testament to the remarkable progress in material science and engineering. It empowers industries to push the boundaries of innovation, offering unparalleled advantages that align with modern demands for sustainability, efficiency, and reliability. With continued research and technological advancements, the future holds even greater potential for these materials to transform industries and redefine the possibilities of modern engineering and design.